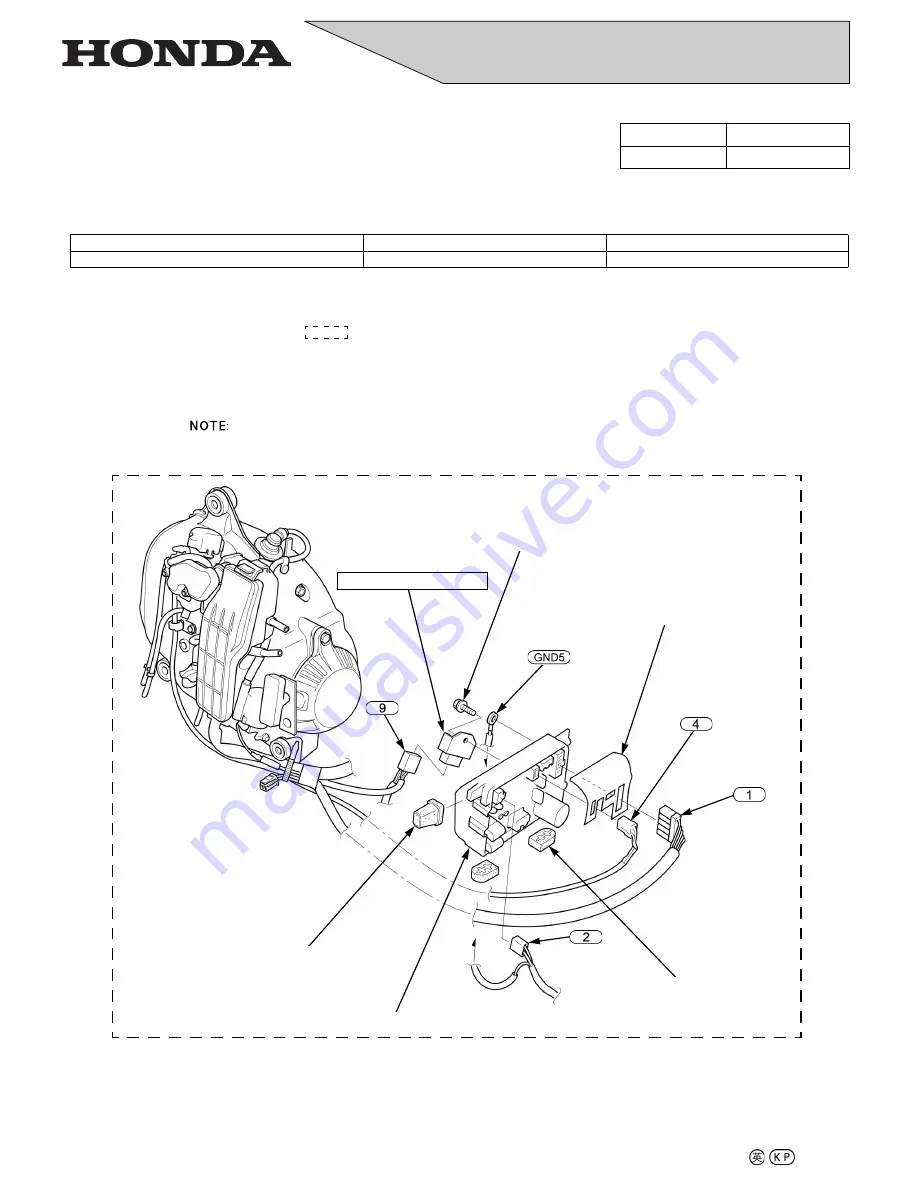
Shop Manual News
GENERATOR
News No.
Issue Date
P/P-388
Mar. 2014
1
Honda Motor Co., Ltd.
Service Publication Office
Power Equipment
SOME PARTS OF CHANGES
CHANGE LOCATION
The changed instructions are shown in
.
Applicable Information
Publication No.
Applicable Page
EU10i
62Z4000
8-9, 8-10
INVERTER UNIT REMOVAL/INSTALLATION
Remove the fuel tank (page 6-3).
• When installing, route the wire harness properly (page 2-8).
INSPECTION: page 8-9
RECTIFIER
INVERTER MOUNTING
RUBBER B
INVERTER UNIT
INVERTER MOUNTING
RUBBER A (2)
WATER PROOF SEAT
BOLT (6 x 12 mm)
2014.03
Содержание EU10iT1
Страница 15: ...MEMO dummyhead dummyhead ...
Страница 33: ...MEMO dummyhead dummyhead ...
Страница 47: ...MEMO dummyhead dummyhead ...
Страница 53: ...MEMO dummyhead dummyhead ...
Страница 55: ...6 2 dummyhead dummyhead FUEL SYSTEM FUEL SYSTEM TOOL Float level gauge 07401 0010000 ...
Страница 67: ...MEMO dummyhead dummyhead ...
Страница 69: ...8 2 dummyhead dummyhead GENERATOR CHARGING SYSTEM GENERATOR CHARGING SYSTEM TOOL Flywheel puller 07935 8050004 ...
Страница 100: ...12 1 12 dummytext 12 MUFFLER MUFFLER REMOVAL INSTALLATION 12 2 ...
Страница 115: ...MEMO dummyhead dummyhead ...
Страница 130: ...16 1 16 dummytext 16 WIRING DIAGRAM HOW TO READ A WIRING DIAGRAM RELATED INFORMATION 16 2 WIRING DIAGRAM 16 3 ...