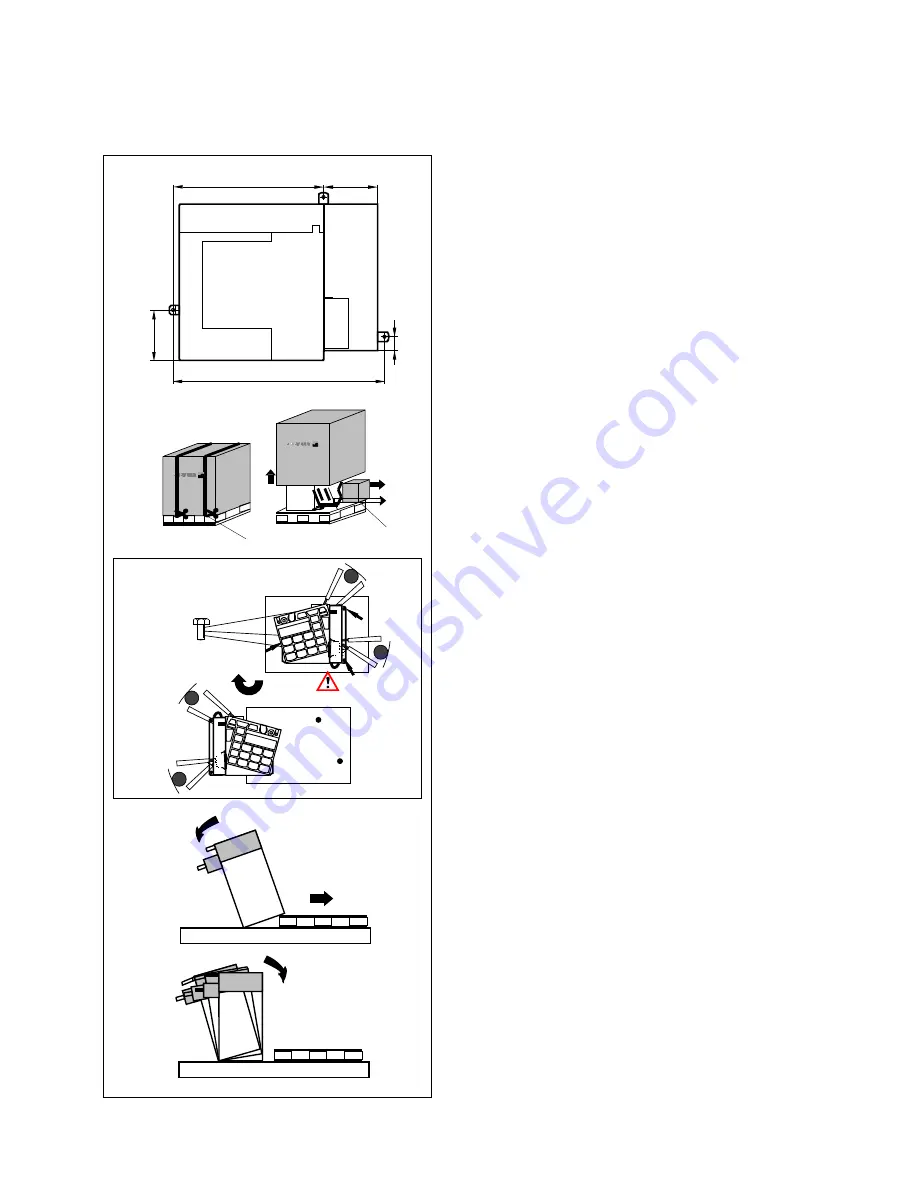
180
2
3
SW 13
4
5
6
523
1
736
190
2
49
Installation of the machine
2. Installation of the machine
When choosing the site, Health and Safety at Work regula-
tions and the regulations on working environment should be
taken into account.
The wheel balancer can be installed on any firm and level
ground. For the weight and space requirement of the machines
refer to § 15., Technical data. For installation on an upper floor,
observe permissible load capacity of the floor.
It is recommended, though not absolutely necessary, that the
machine be secured to the floor. For this purpose three holes
(Fig. 2)
are provided in the base of the machine by which the
latter is fixed on the floor with 3/8 ” anchor bolts. Fig. 2 shows
the center-to-center distance of the holes. Make sure that the
machine has a stable position, i.e. that it is supported on
three
seatings. If not, ensure three-point contact on ground by
inserting appropriate spacers between the floor and machine
base.
For ease of transport the wheel balancer is disassembled
into the following units and provided with special packing (on
pallets):
- Machine
- Wheel guard
2.1 Unpacking the machine
The machine should be unpacked by two persons.
Note
When unpacking the machine make sure that the pedal fitted
on the machine base and the whole pedal assembly is not
damaged.
•
Cut the strips of the packing (
Fig. 3, item 1)
, lift off the
packing, and set aside the wheel guard and the small
parts packed in the separate small box (
Fig. 3, item 2)
.
•
Unscrew the three hexagon screws (use a 1/2 ” wrench
to) which hold the machine on the pallet
(Fig. 4, ar-
row)
.
•
Lift the machine by tube of the vibratory system and
wheel guard arbor and turn around by 180 degrees on
the pallet
(Fig. 4)
.
•
Then lower one side of the machine laterally on the
floor
(Fig. 5)
.
•
Remove the pallet from underneath the machine and
gently lower the entire machine onto the floor
(Fig. 6)
.
2.2 Resiting the machine
If the machine is transported on site, gently tilt it, taking it by
weight box and wheel guard arbor, and push it gently on suit
-
able lifting or mobile industrial handling equipment (e. g. forklift
truck, platform truck).
Note
When lifting the machine bear in mind the centre of gravity of
the machine and avoid oscillating movements.
Operation manual geodyna 2600 EEWB703D
5