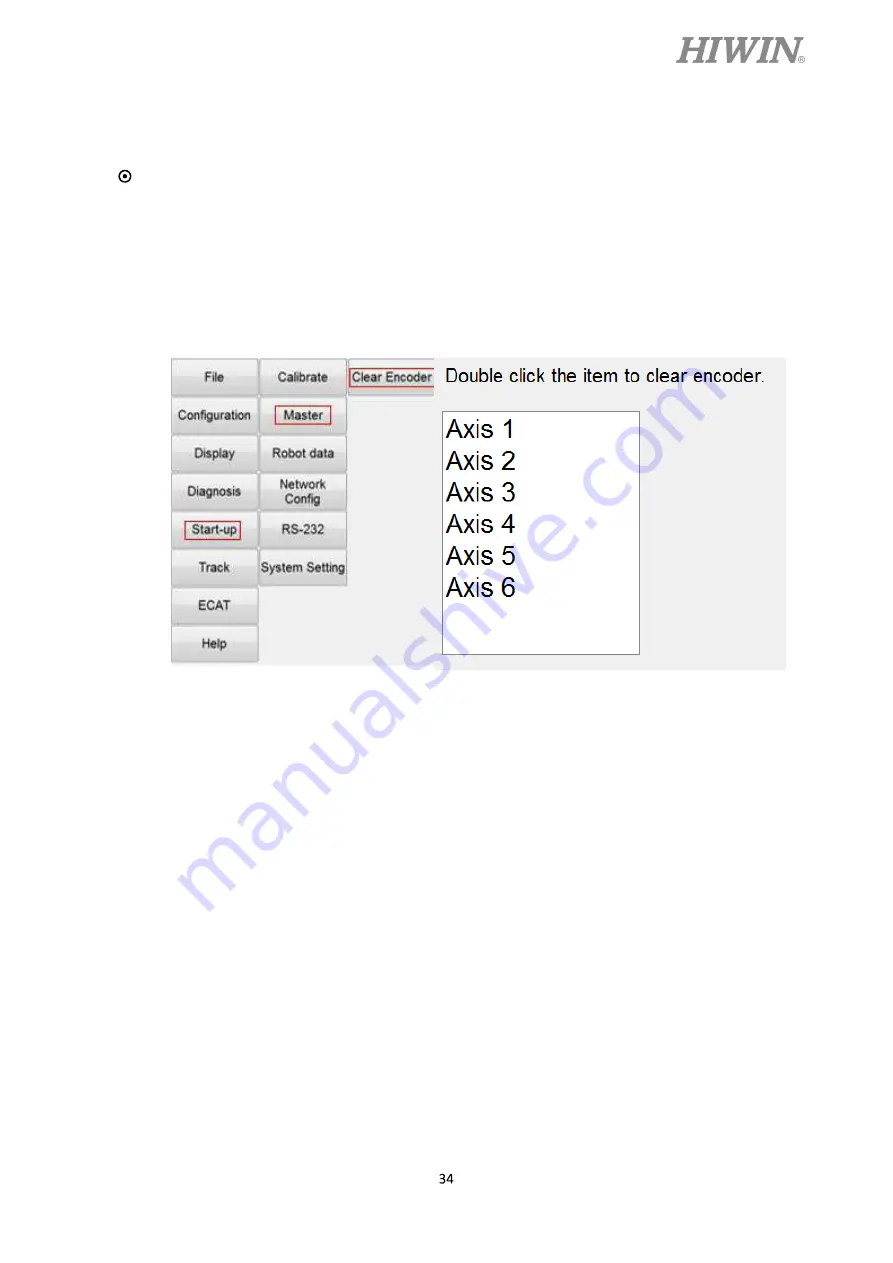
C18UE001-1804
Clear encoder by HRSS
Step1.
Select the “JOINT” as the coordinate system.
Step2.
Move the robot to the Zero-position. (Refer to section 4.1)
Step3.
Click Main Menu>>Start-up>>Master>>Clear Encoder.
(As shown in Figure 4-8)
Step4.
Double click the axis to clear encoder. (As shown in Figure 4-8)
Figure 4-8 Clear encoder by HRSS
Содержание RT605 Series
Страница 1: ......
Страница 14: ...C18UE001 1804...
Страница 26: ...C18UE001 1804 Figure 2 4 RT605 909 GB Motion range...
Страница 50: ......
Страница 51: ......