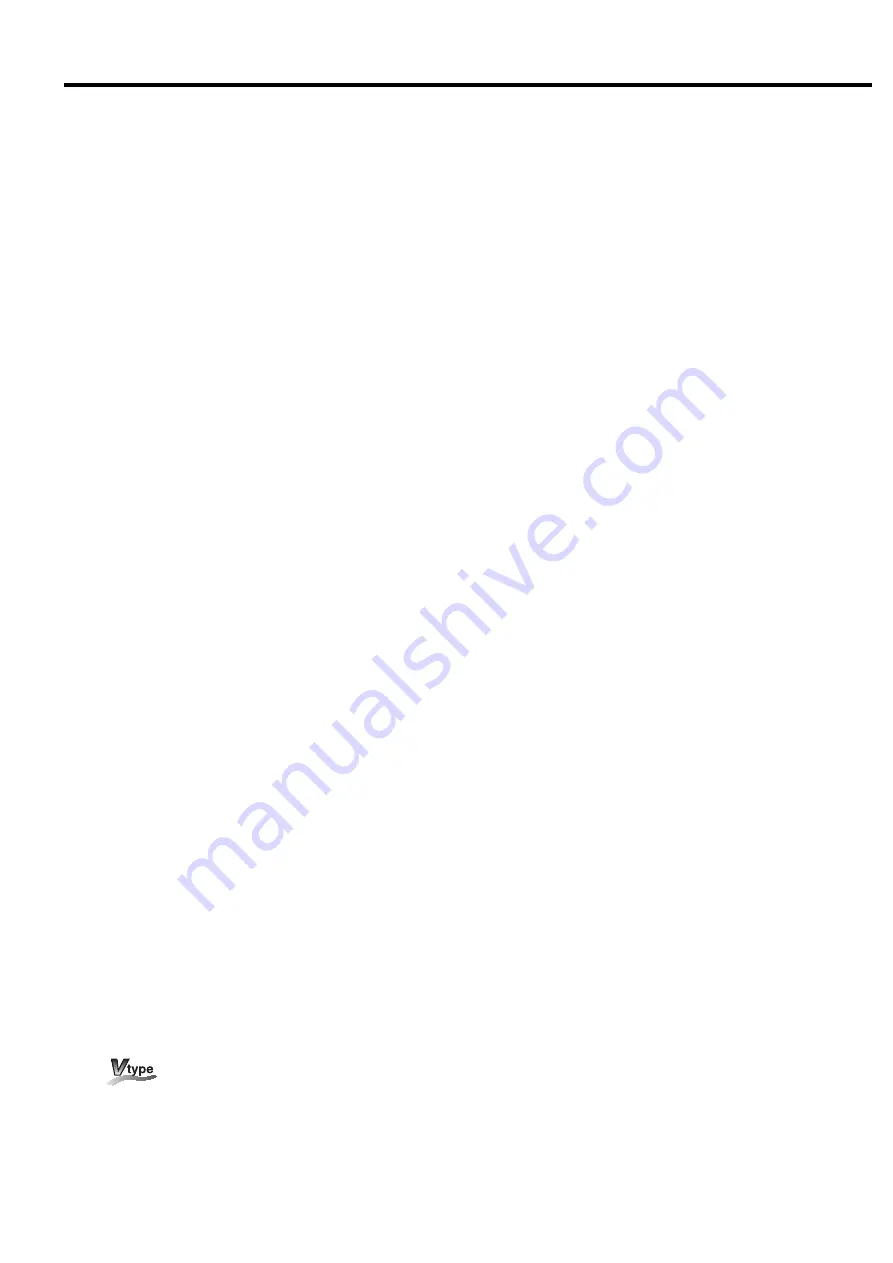
57
8. STANDARD COMPONENTS AND SUBSYSTEMS
⑴
Air End
A pair of screw rotors rotates while the timing gear
keeps a very small gap between them. This non-con-
tacting, high-speed rotation of the rotors compresses
the intake air. Because oil is not injected onto the
rotors during the compression, an oil-free air is dis-
charged.
The air end consists of the following parts:
⑴
Rotor s:
The surfaces of both the male and
female rotors are finished with a special
heat-resistant coating for maintaining the
minimum gap between the rotors.
⑵
Beari ngs:
The larger-load male rotor is support-
ed by the bearings that are larger in diame-
ter, that is, longer in service life.
⑶
Case
:
A cooling water jacket is provided on the
case to absorb the compressing heat.
⑷
Timin g Gears:
A pair of the precision-finished
timing gears is mounted on the ends of the
screw rotor shafts. It keeps a very small gap
between the rotors and allows them a non-
contacting rotation.
⑸
Shaft Seal:
The sealing mechanism consists of
the air seals and the visco-type seals. The
air seals prevent the compressed air from
leaking from the compression chamber while
the visco-type seals the oil that lubricates
the gears and bearings from entering the
compression chamber.
⑵
Compressor Drive Train
The
DSP
employs a high efficient, 2-pole, totally
enclosed, fan-cooled motor for the model. The motor
speed is increased to a rated level, each of the first
and second-stage air ends, by the stepup gears in the
gear case.
⑶
Capacity Control System
When a demand of compressed air decreases, the sys-
tem closes the suction throttle valve and at the same
time blows off the internal compressed air to the out-
side; thus the
DSP
unloads. For more information,
see page 53.
When demand of the compressed air decreases, the
system reduces the motor speed and purges the
compressed air to atmosphere simultaneously.
⑷
Intercooler
The
DSP
employs a shell-and-tube type of water-
cooled intercooler. The intercooler cools the hot,
compressed air of about 0.20MPa (29 psi) that is dis-
charged from the first-stage air end. After reducing
the compressed air temperature down to less than
the cooling water tempe 15 to 20
℃
(59
℉
to
68
℉
)
,
the intercooler separates the condensed water
from the compressed air. The cooled, compressed air
flows into the aftercooler.
⑸
Aftercooler
The
DSP
employs a shell-and-tube type of water-
cooled Aftercooler. Located after the check valve, the
Aftercooler cools the hot, compressed air that is dis-
charged from the second-stage air end.
After reducing the compressed air temperature down
to less than the cooling water tempe 10 to
20
℃,
the Aftercooler separates the condensed water
from the compressed air.
⑹
Check Valve
Located downstream the second-stage air end, the
check valve prevents the discharge air from flowing
back.
⑺
Lubricating Subsystem
Lubricating subsystem consists of the oil pump, oil
strainer, oil filter, oil cooler, and oil temperature con-
trol valve. The oil pump circulates the oil in the gear
case oil sump through the lubricating subsystem and
thereby lubricates the bearings, gears, etc.
⑻
Air Intake Filter
The
DSP
employs a dry-type air intake filter that is
easily cleaned and replaced.
⑼
Cooling Fan
The small cooling fan cools the inside of the package,
and exhausts the internal compressed air that is
released to atmosphere during the unloading process.
⑽
Starter
Either starter employs a printed circuit board on
which a microprocessor is mounted, and thereby you
can easily choose an operation mode and control func-
tion. Both the models come standard with the termi-
nals for a remote operation.
⑾
Enclosure
The enclosure panels are attached with the sound
absorbing materials. The front enclosure panel
includes a door that eases your maintenance services.
8.1 Standard Components