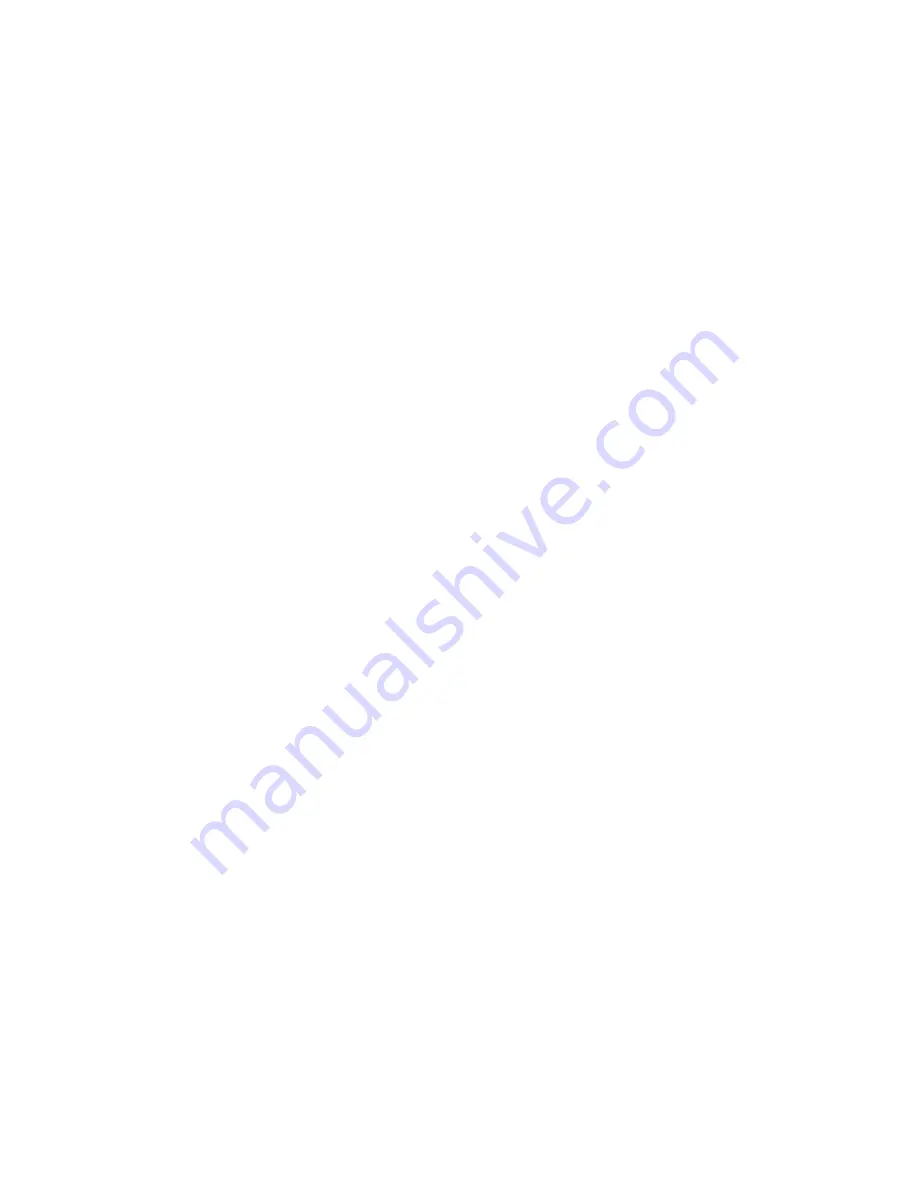
XPM 200HR™
Thermal Printer Family
HENGSTLER
®
Part No. D 690 074
Mod. No. 4 300113 LEV
page 28 of 32
11. Repair
All Hengstler printers are repaired at our facility in Aldingen, Germany. For details, and to arrange for
the return of a printer for repair, please contact us at:
HENGSTLER GmbH
Uhlandstrasse 49
78554 Aldingen / Germany
Tel. +49 (0) 7424-89 0
Fax +49 (0) 7424-89 500
eMail: [email protected]
www.hengstler.com
12. Buying Paper
12.1. Sourcing Paper
In order to maintain your warranty, use only paper that conforms with XPM 200HR™ Paper
Specification D 689 xxx. Use of paper that does not conform with this specification may
adversely affect the performance of your XPM 200HR™ printer and/or damage your printer.
Please note that the XPM 200HR™ can use either roll or fanfold paper. When using fanfold
paper, care must be taken to configure the printer, black mark, and positioning so that the cut
always occurs
after
the fanfold bend, not on it or before it. Failure to do so will cause cutting
problems and will likely increase paper jams.
12.2. Converting Paper
Thermal paper is usually purchased through paper converters. These companies buy large,
jumbo rolls of specific paper types from the few true paper manufacturers in the world and
then cut it and roll it to your specifications. You may elect to have preprinting or black marks
added at this time, as well. Please make sure that any paper a converter wishes to supply
you for use with your XPM 200HR™ printer conforms with XPM 200HR™ Paper Specification
D 689 112.
12.3. Black Mark Sensor Location
The Black Mark sensor (which also functions as a “paper present” sensor) on the XPM
200HR™ printers can be located in numerous positions during manufacturing. Figure 13
shows where the black marks should be located in order to be detected when a reflex sensor
is used. The default (standard) sensor positions are so marked.
The XPM 200HR™ printer is designed to allow for numerous Paper Entrance/Black Mark
sensor locations during manufacturing. (The location of this sensor cannot be changed once
the printer is built.) Also, two different sensor types can be used. One is the reflex or
reflective sensor, where the light source and detector are located on a single chip. Basically,
the light strikes the white paper surface and reflects back into the sensor. If enough light
reflects to activate the sensor, the printer reports that paper is present. If there is not enough
light reflected, the printer assumes that this area is black, meaning the printer is on a black
mark or the printer is out of paper. Black marks must be located on the back (non-coated)
side of the thermal paper. There are 19 different possible positions for this sensor. The
positions of these sensors are detailed in Figure 13. (Please note that sensor positions 1, 7
and 16 are not usable due to a lack of an open position to their left.) The default (standard)
positions are so marked. Paper suppression guides are small inserts with mushroom-shaped
heads that are used to ensure that the paper is at the correct distance to be detected properly
by the sensor. Please also note that sensor locations other than the default location are
intended for OEM applications.