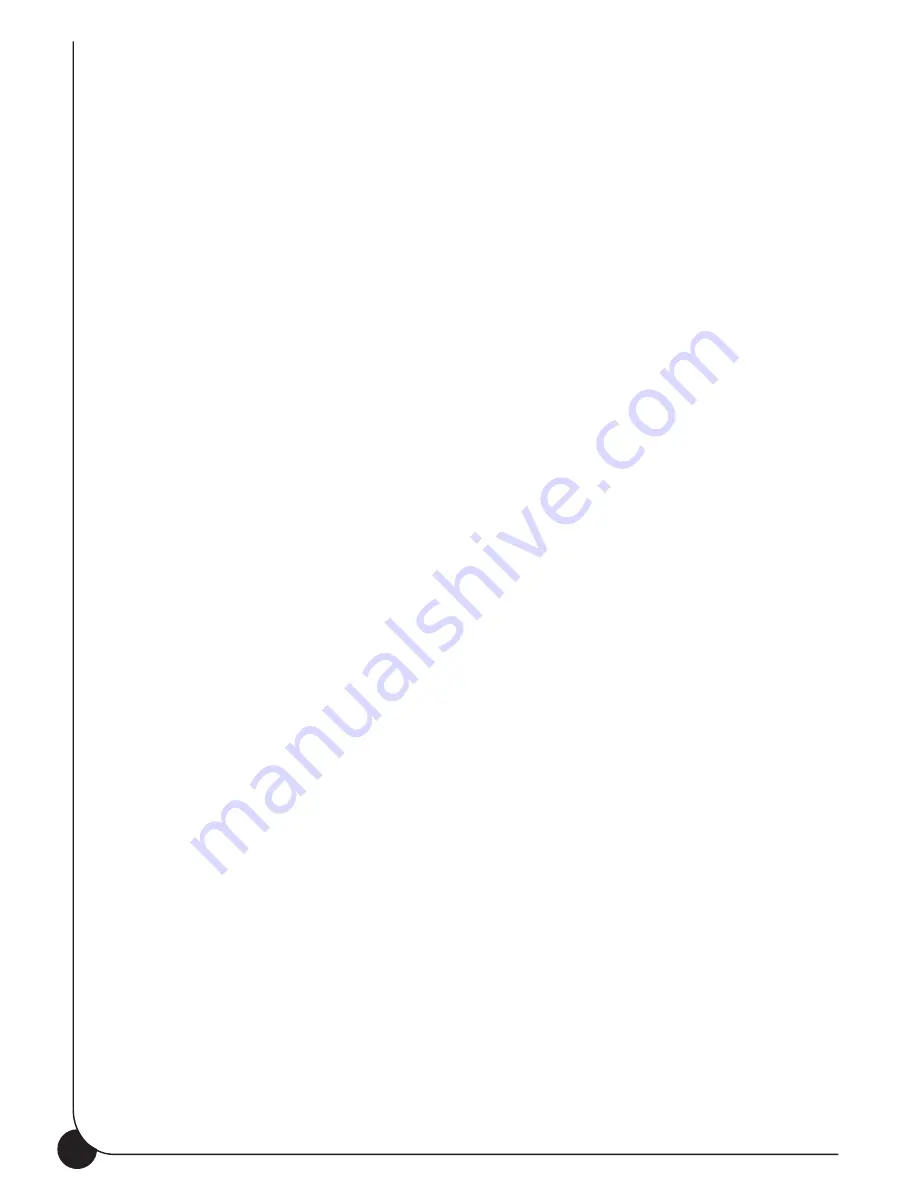
1.
Power switch indicator: This green LED lights when the welding machine is ON and is ready to work.
In the event of an overvoltage supply the green LED blinks and the red LED (3) is ON.
2.
Thermal overload indicator: If the yellow LED is ON it indicates that the welder has overheated and
the machine has automatically shut down. This may be a result of having exceeded the welders duty
cycle or that normal cooling air flow has been interrupted. Check to confirm that the cooling fan is
running and that air flow is not blocked. Do not turn off the welder as this will stop the cooling fan.
When the welder has cooled sufficiently the yellow LED will go out and the welder is ready to weld.
3.
Alarm indicator: This red LED lights when there is a working abnormality such as an over voltage
supply.
4.
Left Display: During welding it displays the actual value of the output current (AMP).
When the machine is not welding, (no load), the display shows the value of the parameter selected
with the Left Knob (8):
a.
In STICK and TIG mode it shows the selected current value.
b.
In MIG MANUAL mode the display shows the selected wire speed in m/min.
c.
In MIG SYNERGIC mode the display shows wire speed balance; possible variation is +/-40%
on the base value adjusted by default ( “0” on the display, central position).
5.
Right Display: during welding it displays the actual arc voltage.
When the machine is not welding (no load) it displays the value of the parameter adjusted with the
Right Knob (7):
a.
in STICK mode it displays the Hot Start over-current value expressed as a percentage of the
base welding current selected with the left knob (8). The over current value is variable from 0 to 50%
of the base current. Maximum Hot start value of 50% can be adjusted up to 120Amp of welding
current. On the display the value of Hot Start is shown as “H” and the value of the over current in %.
b.
In TIG Mode the display is not active.
c.
In MIG MANUAL it displays the selected arc voltage from 12V to 26V.
d.
In MIG SYNERGIC it displays the thickness of the material to be welded expressed in mm.
6.
Selector switch for the Welding Modes Selection: MMA, TIG, MIG manual, MIG Syn.
7.
Right Knob: it is used to adjust the following welding parameters.
a.
in STICK Mode it adjusts the over-current value of the electric arc (Hot Start), variable from 0
to 50% on the current value adjusted with the Left Knob (8).
b.
In TIG Mode is not active.
c.
In MIG manual it adjusts arc voltage value (no load) from 12V to 26V.
d.
In MIG Synergic it selects the thickness of the material to be welded.
8.
Left Knob: it is used to adjust the following welding parameters.
a.
In STICK Mode it adjusts the current value from a minimum of 20Amp to a maximum of
170Amp.
b.
In TIG Mode, it adjusts the current value from a minimum of 5 Amp to a maximum of
170Amp. .
c.
In MIG manual it adjusts the wire speed.
d.
In MIG Syn it adjusts the wire speed; possible variation is +/-40% on the base value adjusted
by default ( “0” on the display).
9.
Negative Dinse socket:
a.
in STICK welding for the connection of the ground cable connector (check for correct polarity
for the electrode you are going to use, refer to the information on its box);
b.
in TIG Welding for the TIG torch cable connection;
c.
in MIG welding (with gas) for the connection of the ground cable connector.
10. Positive Dinse socket:
a.
in STICK welding, for the connection of the working cable connector (check for correct pola-
rity for the electrode you are going to use, refer to the information on its box);
b.
in TIG Welding for the connection of the ground cable connector;
c.
in MIG Flux Core Welding (FCAW), for the connection of the ground cable connector
11. Euro connect for attaching the MIG torch cable. In MIG Flux Core welding (FCAW), change the
polarity of the Euro socket using the terminals on the polarity change board located inside the wire
spool compartment above the wire feeder -18-.
12. Input power cable (back panel)
13. ON/OFF Switch
14. Gas Hose connector (back panel)
15. 2 roll Aluminum wire feeder
16. Slope up Time regulation potentiometer
17. Burn Back Time Regulation Potentiometer (B.B.T.)
18. Polarity Change Terminals for the Euro Socket:
a.
positive polarity for MIG/MAG Welding;
b.
negative polarity for No Gas Welding.
19. Spool holder
8
Содержание TP 195
Страница 1: ...TP 195 OPERATING MANUAL ...
Страница 2: ......
Страница 15: ...15 Figure 9 ...
Страница 16: ...13 0 WIRING DIAGRAM 16 ...
Страница 17: ...17 ...
Страница 18: ...18 ...
Страница 19: ...19 ...
Страница 20: ...77611864 ...