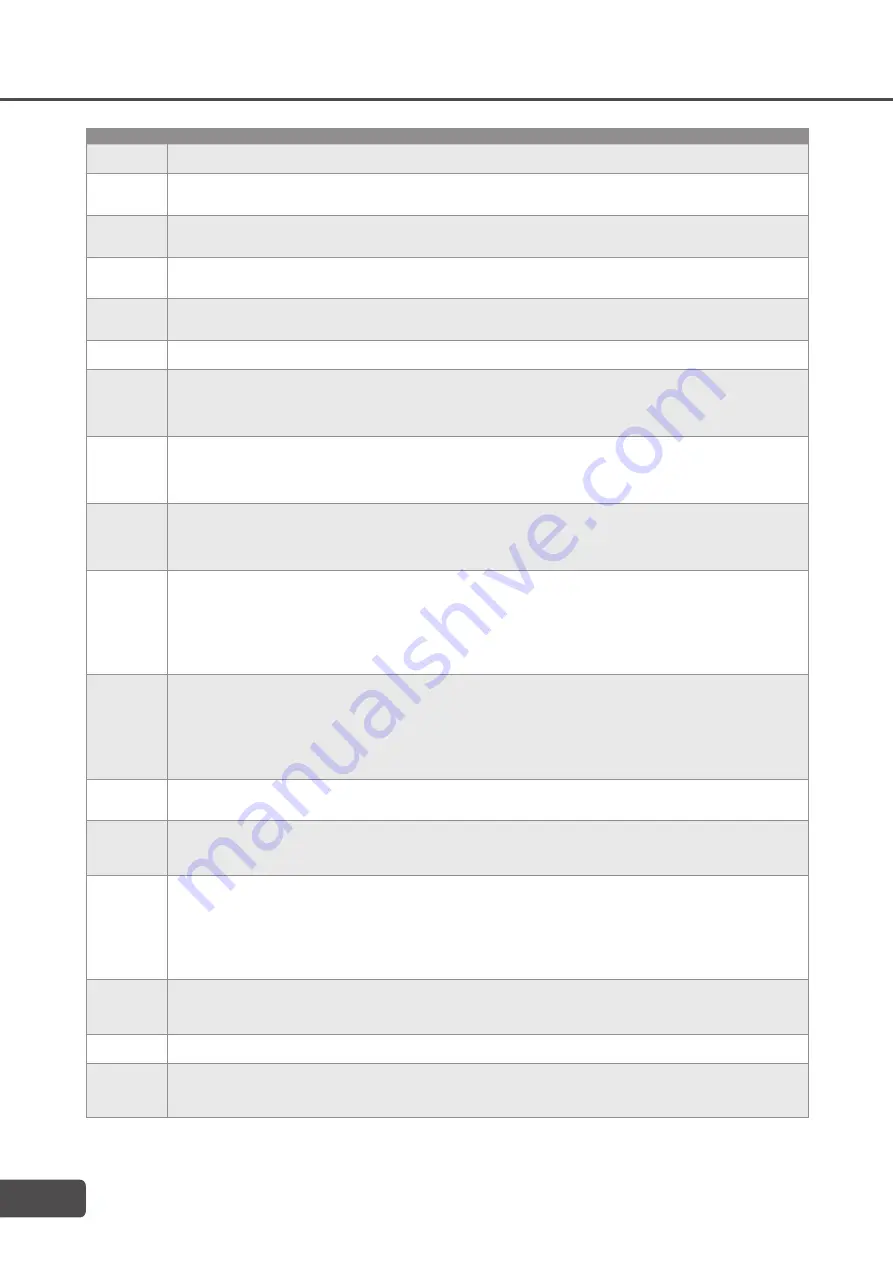
231135 rev.3 2019-06-26
Drester GP Filter eQ
ERROR CODE TEXT IN DISPLAY
ACTION IN DISPLAY
PROBLEM DESCRIPTION & SOLUTION
10
Board overheated
Contact Service Technician
Maximum permissible PCB temperature. Check and lower the
ambient temperature (Max. 40°C).
11
Fuse MF3 Overload
Check DI P8
Short circuit on digital input P8.
Fuse is self-resetting. Check cable and connected component. Re-
start the unit – if problems persist, contact a service technician.
12
Fuse MF4 Overload
Check DI P11-16
Short circuit on digital input P11-16.
Fuse is self-resetting. Check cable and connected component.
Restart the unit – if problems persist, contact a service technician.
13
Fuse MF5 Overload
Check DI P17-21
Short circuit on digital input P17-21.
Fuse is self-resetting. Check cable and connected component.
Restart the unit – if problems persist, contact a service technician.
14
Fuse MF6 Overload
Check DO P22-26
Short circuit on digital output P22-26.
Fuse is self-resetting. Check cable and connected component.
Restart the unit – if problems persist, contact a service technician.
1
Cannot Read NVM,
Restart Machine
Contact Service Technician
Internal memory failure on PCB. Reinstall software (see
"Software Update").
20
Upper Vessel Vacu-um
too High
Check Air Press./WW Drain blockage?
Maximum vacuum level setting exceeded. Remove any
blockage in the wheel washer filter strainer or drain hose
(position 6) between GP Filter eQ and the wheel washer. Under
certain conditions, the maximum vacuum level setting can be
raised by service technicians.
40
Bottom Cylinder not
Retracted
Check Bottom Cylinder Valve/Pos.
Pneumatic cylinder in upper vessel (position 1) is not returning.
Make sure the piston rod runs free. Check that the drain cone
is not stuck. Check the function and position of the position
.
Tips
: Use the self-test function in the "Self-test" submenu.
41
Bottom Cylinder not
Extended
Check Bottom Cylinder Valve/Pos.
sensor -
Pneumatic cylinder in upper vessel (position 1) is not extending.
Make sure the piston rod runs free. Check that the drain cone
is not stuck. Check the function and posi-tion of the position
sensor -.
Tips
: Use the self-test function in the "Self-test" submenu.
42
Dosing Cylinder not
Retracted
Check Dosing Cylinder Valve/Pos.
sensor -
Pneumatic cylinder in dispenser (position 2) is not returning.
Make sure the piston rod runs free. Remove dosing unit and
clean all moving parts. Check the function and position of the
position sensor -.
Tips 1
: Use the self-test function in the "Self-test" submenu.
Tips 2
: A quick clean can be done inside the upper vessel
(position 4) by removing the inspection hatch (position 3) and
using the wash brush provided.
43
Dosing Cylinder not
Extended
Check Dosing Cylinder Valve/Pos.
Pneumatic cylinder in dispenser (position 2) is not extending.
Make sure the piston rod runs free. Remove dispenser and
clean all moving parts. Check the function and position of the
position
Tips 1
: Use the self-test function in the "Self-test" submenu.
Tips 2
: A quick clean can be done inside the upper vessel
(position 4) by removing the inspection hatch (position 3) and
using the wash brush provided.
50
High Water Level in
Upper Vessel
Check Upper Vessel Drain/Fouling
Sensor (position 5) has an incorrect or constant signal. Make
sure the drain is not clogged or that dirt has built up inside the
upper ves-sel (position 4) at the sensor position.
51
High Water Level in
Wheel Washer
Clean WW Level Sensor/Level Tube
Blockage?
Sensor (position 13) has an incor-rect or constant signal. Make
sure that the sensor is not incorrectly aligned or has dirt on its
surface. Also clean the level tube including hose (position 12) if
there are any signs of contamination/foam.
52
Water Transfer Timeout
Check WW Drain Blockage/Vacuum
Lev-el/Vacuum Leaks
Maximum time allowed with vacuum activated is exceeded.
Make sure that the drain hose (position 6) between the wheel
washer and the filter unit is not blocked. Clean if necessary.
Make sure there is no vacuum leak when vacuum is activated.
The vessel including drain must not leak. Check/clean as
necessary the bottom outlet and check the gasket on the
inspection hatch.
Tips
: Use the self-test function in the “Self-test” submenu.
60
N/A
Check Flocculation Powder Level
Make sure the flocculation powder is not stuck or formed
obstructions in the tube (position 20). Fill up if necessary. For
longer inactive periods, it is recommended that powder be
removed in order not to absorb moisture.
61
N/A
“Check Filter”
A filter change is recommended. Filtering efficiency cannot be
guar-anteed on re-used filters.
70
Drain Pump Timeout
Check Drain Pump and Hose
Maximum permissible running time for drain pump (position
11) exceeded. Check pump function and that hoses are not
blocked Make sure that the pump level sensors (position 10) are
not short circuited.
14