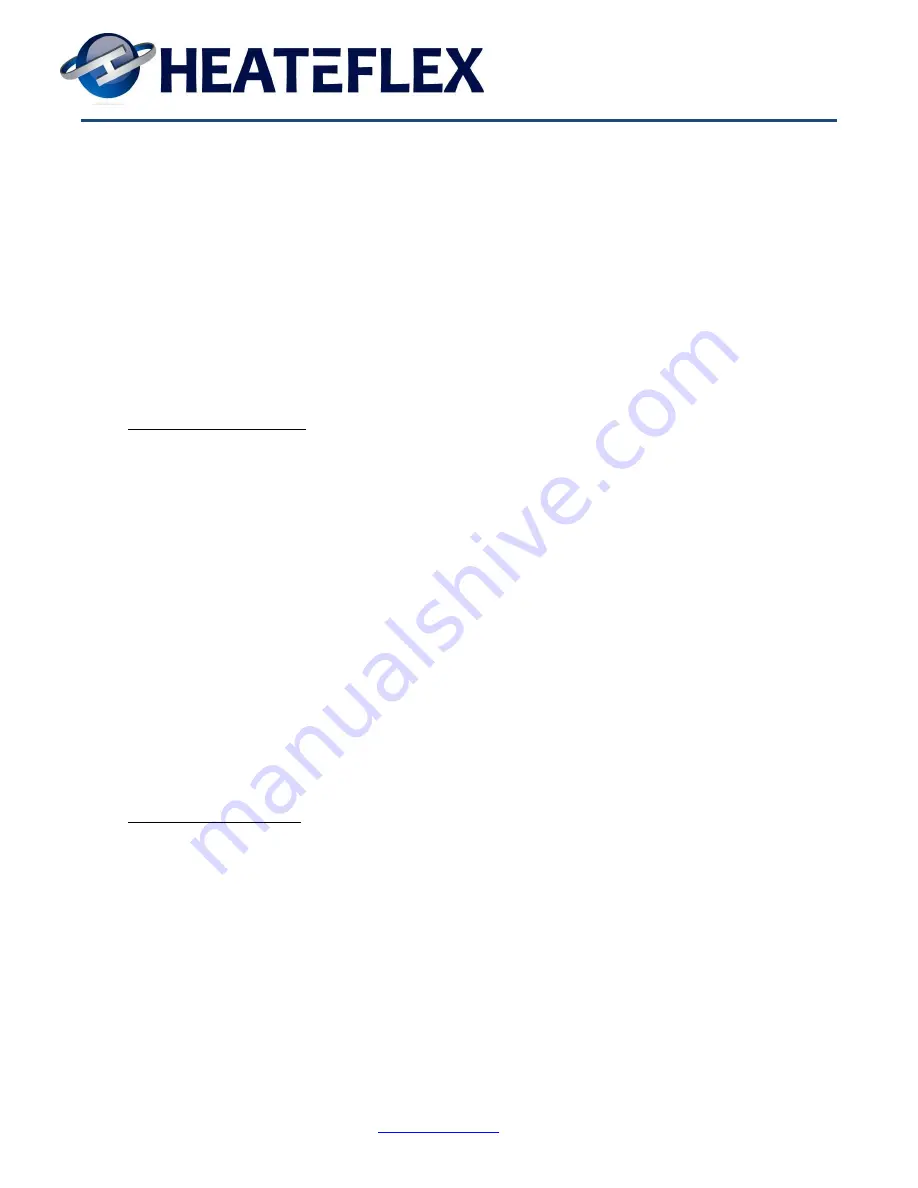
World Leaders in Ultra-Pure Heating
Revision 10
www.heateflex.com
01/17/13
405 E. Santa Clara St.
Arcadia, CA 91006-7218
Tel: (626) 599-8566 Fax: (626) 599-9567
_________________________________________________________
5.2.1 Repairing a Tube Failure
Repairing a failed tube in the literal sense is not actually possible. The final assembly of the
exchanger does not allow an easy replacement of individual tubes. Rather, if a tube failure is
present that specific tube is removed from service. This is done with a simple blocking
technique similar to the one used for conventional shell and tube exchangers.
The exchanger has been manufactured to be 10% larger in capacity than the net calculations
dictate. This allows for the blocking of several tubes without affecting the exchanger's ability
to meet the specified process requirements.
Detecting a Failed Tube:
A simple check can be done to confirm if a tube leak exists. First, however, the shellside of the
system MUST be cooled down. This is best achieved by switching the Steam Valve switch on
the System Status screen to the “Close” position while D.I. water continues to flow through the
unit. When the shellside temperature in the exchanger falls to below 50°C (122°F), leave the
D.I. water supply line pressure on, and close the unit‟s outlet valve first, followed by the inlet
valve. Next, open the valve fitted with a pressure gauge on the respective manifold on the top
of the unit (the pressure gauge may be stored inside the electrical enclosure). Note the pressure
and monitor same to see if the pressure goes down. If so, there is a leak in one of the
individual tubes in the exchanger
If a tube leak is suspected, close the manual isolation valves (standard configuration) on the
exchanger manifolds and the flow should stop. Note that the actual number of isolation valves
will vary from model to model. Next, open the inlet valve one at a time to isolate which part of
the exchanger has the leak. Note that the corresponding inlet and outlet headers are mirror
images of one another. For example, the very front and very rear manifold comprise the inlet
and outlet of one of the tube bundles in the exchanger shell. If the headers are numbered from
one to four, front to rear, then the corresponding pairs are 1/4 and 2/3.
Finding the Failed Tube:
As previously mentioned, repairing a tube leak actually consists of blocking the tube and
taking it out of operation. Before doing this, however, the exact tube which failed must be
identified. Note that the tools and test/repair parts referred to in this section are available from
the factory.
Loosen the nuts on the flare fittings across the exchanger manifold, and pull off the tubes, one
at a time, and cap both the tubing and the fitting with slip-on caps to maintain the purity of the
system. Taking the tubes in sequence across one header, pressurize each tube slowly using D.I.
water from a supply line fitted with a flare fitting until the slip-on cap on the corresponding
tube from the opposite manifold pops off. Note that on the four-head systems, the exchanger is
divided into two separate tube bundles. The corresponding pipe manifolds (inlet to outlet) are
inside to inside and outside to outside. The tubes are not always in exactly mirror-image