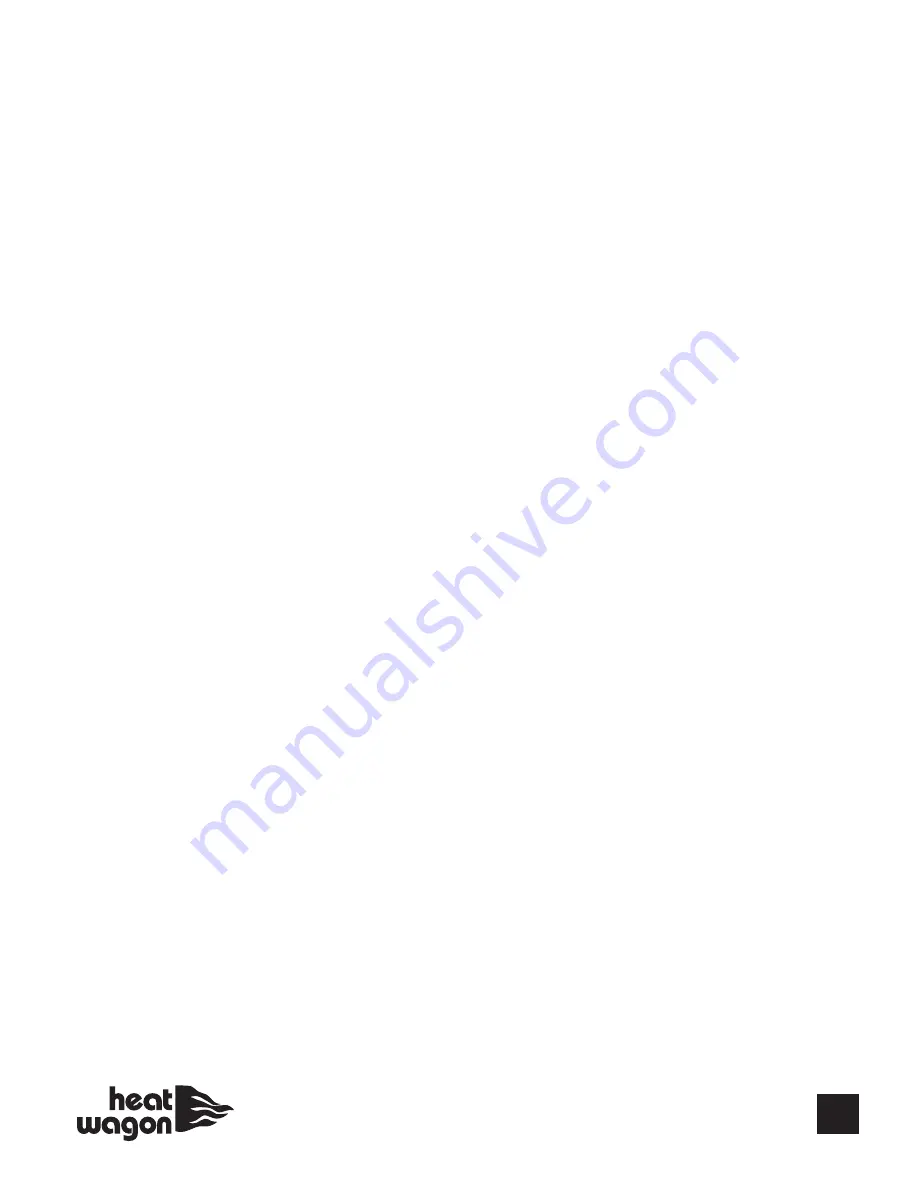
7
Common Installation & Operational Problems
1.
Low Voltage-
This is one of the most common problems and is usually the result of the supply
cord having too small a wire gauge for its length. Low voltage results in the motor overheating,
burnt relay contacts, or a relay that will not make contact.
2.
Supply line undersized. (Refer to page 15-16)
3.
Insufficient Vaporization at Supply-
Normally caused by undersized supply tank.
4.
Improper Gas Supply Pressure
- Usually a result of supply pressure being too high because of
improper or no regulation.
5.
Dirty Gas Supply -
Dirty gas can cause strainers to plug or form a buildup in the burner orifice.
6.
Lack of Preventative Maintenance -
Heaters must be cleaned as required, especially when used
in a dirty environment.
7.
Improper Supply of Fresh Air -
It is normally recommended that the intake air of the heater
be taken from outside the enclosed area. This provides a slight pressurization and prevents any
problems associated with recirculation.
On-Site Safety Problems
1.
Shorting out of defective components
This is a very common problem which saves short term expense at the risk of a large future cost.
Any heaters found in this condition should be removed immediately.
2.
Improper enclosures
When heaters are installed partially to the outside for fresh air intake, strict adherence must be
made to the minimum clearance to combustibles given on the instruction plate. Wood framing
around a heater is a request for trouble.
3.
Supplying liquid propane to heater
This problem has occurred from time to time. To minimize the damage, shut off the gas supply
and let the heater run until all of the liquid in the lines has been burnt.