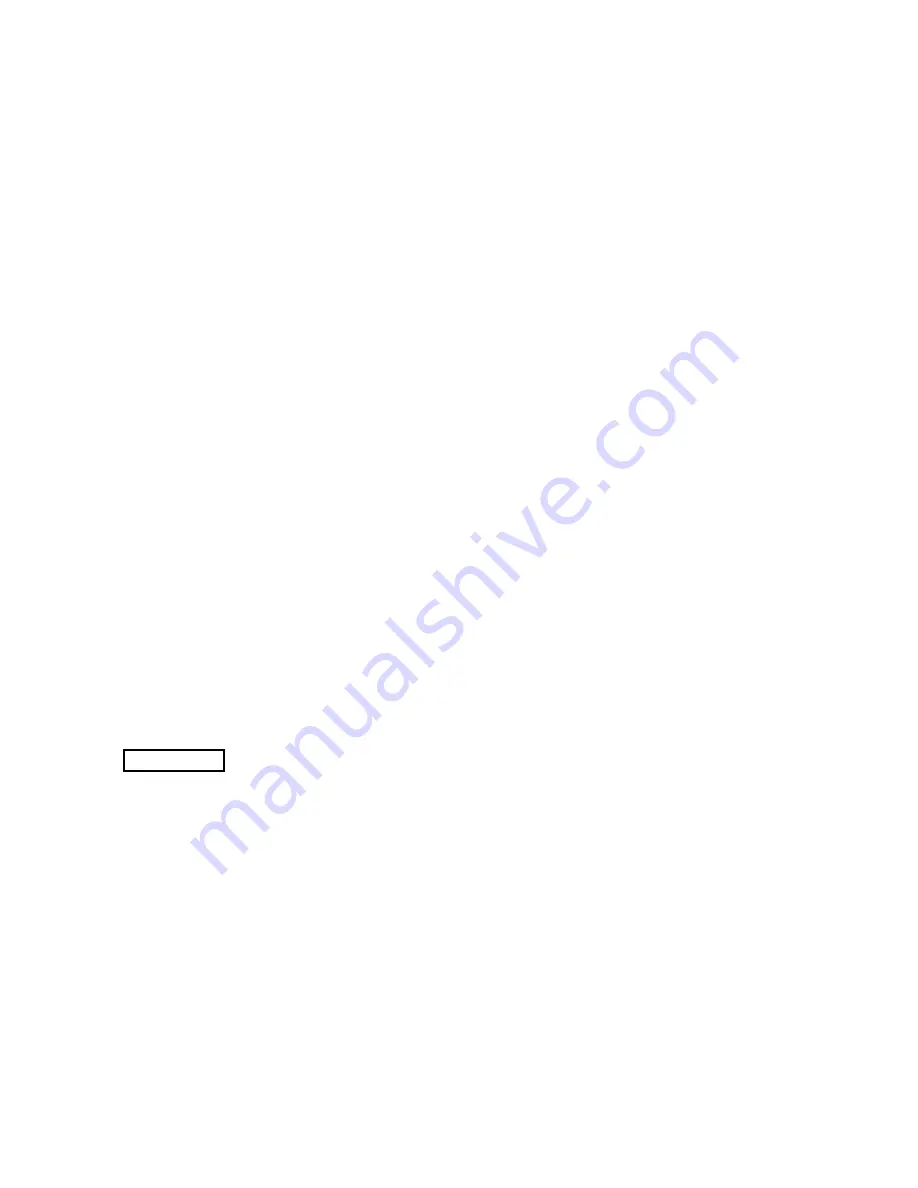
4.6.
Symptom: High Voltage Is Pre-
sent, But There Is No Power
Output
4.6.1.
PDM Kill Condition
Check the PDM Power Level reading on
the multimeter, and the status of the PDM
Kill LED on the front panel. If there is no
signal of a closure of the Run contactor
(K2), there will be a PDM kill condition.
Listen for the closure of K2. It should be
heard closing after K1 has closed. Clean the
auxiliary contacts of K2.
A PDM Kill can also come from an exter-
nal device such as an RF contactor in a
phasor. Check for an external kill signal and
make sure that all RF contactors in the
antenna system are fully seated.
4.6.2.
PDM Level
Check the PDM Level reading on the Mul-
timeter. If it is zero for all power levels, there
may be a failure on the Controller board.
Refer to the troubleshooting information in
Section J on the Controller.
4.7.
Possible Causes For Overloads
4.7.1.
Supply Voltage Overload
4.7.1.1.
Supply Voltage Too High
Check the Supply Voltage reading on the
Multimeter. If the transmitter will stay on
long enough, compare this reading with the
value recorded on the factory test data. Also
check the Supply Voltage Set reading on the
Multimeter. This is the threshold at which
an overload should occur. This is read on the
same scale as the Supply Voltage, and is
normally 290 volts. This value is deter-
mined by the ratio of resistors R10 and R52
on the Controller board.
WARNING
ENSURE ALL AC VOLTAGE HAS BEEN
REMOVED FROM THE TRANSMITTER
AND THAT THE GROUNDING STICK IS
USED TO REMOVE ANY RESIDUAL VOLT-
AGE THAT MAY BE PRESENT BEFORE
THE TAPS ON THE HIGH VOLTAGE
TRANSFORMER ARE CHANGED.
If the present Supply Voltage reading is
significantly higher, remove all AC voltage
being supplied to transmitter and re-tap the
high voltage power supply transformer to a
higher primary setting. For example, if the
transformer is presently tapped to 240/0,
change the tapping to 240/+11. This will
reduce the supply voltage by about 5%.
If the transmitter has been operating with
the proper supply voltage for some time,
and only recently increased, check to see if
the power line voltage has increased.
4.7.2.
Power Supply Current Over-
loads- At Turn On
4.7.2.1.
Supply Short
If the transmitter does not try to operate at
a reduced power, there may be a High Volt-
age Supply short. There are two protection
modes: The normal response of the protec-
tion circuitry is to perform a momentary
PDM interrupt. If the high current condition
remains, an OFF command is given.
A short of the Supply may be caused by
mechanical failure of the safety switch
which is normally opened by installation of
the rear panel.
Another cause could be a shorted High
Voltage filter capacitor.
4.7.3.
Power Supply Current Over-
loads, Continuous Cycling and
Automatic Cutback
4.7.3.1.
PDM System Problem
If the over current problem is affected by
the PDM interrupt, but exists upon return of
PDM, the transmitter will step to the next
lower power. This Automatic Cutback ac-
tion can continue until the transmitter cy-
cles all the way OFF, or the current drops
below a safe value.
Check the Supply Current Set reading on
the Multimeter to be sure it is at a normal
value as indicated on the factory test data
sheet. This reading should not change un-
less a change has been made to the overload
adjustment.
Check the actions of the PA AMPS and
Power Output meters at turn on. If they
deflect upwards at turn on, it is evident there
is current actually flowing in the PA.
Check the PDM Power Level reading on
the Multimeter. If the Multimeter is pinned,
there is a problem on the Controller. Refer
to Section J concerning troubleshooting of
the Controller. If the PDM Power Level
reading is okay, the problem is in the PDM
system.
4.7.3.2.
PDM Generator Outputs High
Check the outputs of the PDM Generator
at the right side of R45, R46, R62, and R63
with a scope or voltmeter. If any of the
outputs are continuously high (12 to 14
volts) a PDM Generator problem is indi-
cated. You may also isolate the problem by
disconnecting the output (P2) from the
PDM Generator. Refer to the troubleshoot-
ing procedures in Section F on the PDM
Generator if the results indicate the problem
resides there.
4.7.3.3.
PDM Amplifier Shorts
If the Outputs of the PDM Generator are
okay, there may be some short(s) on the
PDM Amplifiers. Observe the PDM Fault
sensing LEDS on the front panel, and refer
to Section G, Troubleshooting the PDM
Amplifiers.
4.7.3.4.
Supply Current Calibration
If you have just installed a new Controller
board, the Supply Current calibration may
have been overlooked. Check this, per the
procedure outlined in Section J on the Con-
troller.
Check the Supply Current Set reading on
the Multimeter. It would need to be adjusted
only if you have just installed a new Con-
troller board.
Also check the condition of the power
supply current shunt resistor A19R7, lo-
cated on the right side wall above the PDM
Filter boards. Loose hardware or an open
shunt wire would result in Supply Current
overloads.
4.7.4.
Random Supply Current Over-
loads With Modulation
4.7.4.1.
Sub-audible Signals
Random Power Supply current overloads
are most likely caused by significant levels
of sub-audible signals on the transmitter
audio input. The GATES Series™ of trans-
mitters and some modern day audio equip-
ment can pass sub-audible signals. Check
your audio sources and the setup of your
audio processing.
4.7.5.
Underdrive Fault
4.7.5.1.
Low/No Drive
Check the RF Drive reading on the Mul-
timeter. If low or zero, there is a problem in
the RF Drive system.
Oscillator Output. Having no RF drive
could be caused by failed RF Oscillator.
Check the status of the green RF Output
LED on the Oscillator board. If it is not lit,
refer to Section A, Troubleshooting the RF
Oscillator.
4.7.5.2.
IPA and PA Transistors
Another cause for low/no drive may be
failed IPA transistors, abnormally low IPA
supply voltage, or several shorted PA tran-
sistors. Refer to Sections B and C covering
the IPA and PA.
4.7.6.
VSWR Overload- Continuous
VSWR Cycling
4.7.6.1.
Bad Load Impedance
Continuous VSWR cycling resulting in
the Automatic Cutback operation indicates
a severe change in the impedance into
which the PA is operating. The transmitter
will probably stay on at a reduced power,
but the VSWR Detector Null reading will
be high, depending upon the extent of the
problem.
4-2
888-2314-001
Rev. T: Jan. 1996
WARNING: Disconnect primary power prior to servicing.
Содержание Gates Five 994 9204 002
Страница 4: ......
Страница 6: ...iv 888 2314 001 Rev X WARNING Disconnect primary power prior to servicing...
Страница 8: ...vi 888 2314 001 Rev X WARNING Disconnect primary power prior to servicing...
Страница 28: ...2 12 888 2314 001 Rev AC 2 29 00 WARNING Disconnect primary power prior to servicing...
Страница 40: ...Figure 5 1 PDM Flow Diagram 5 2 888 2314 001 Rev T Jan 1996 WARNING Disconnect primary power prior to servicing...
Страница 42: ...Figure 5 2 PDM Loop 5 4 888 2314 001 Rev T Jan 1996 WARNING Disconnect primary power prior to servicing...
Страница 43: ...Figure 5 3 RF Flow Rev T Jan 1996 888 2314 001 5 5 WARNING Disconnect primary power prior to servicing...
Страница 76: ...C 6 888 2314 001 Rev AE 03 05 2002 WARNING Disconnect primary power prior to servicing...
Страница 82: ...E 4 888 2314 001 Rev AE 03 05 2002 WARNING Disconnect primary power prior to servicing...
Страница 88: ...F 6 888 2314 001 Rev AE 03 05 2002 WARNING Disconnect primary power prior to servicing...
Страница 96: ...H 2 888 2314 001 Rev AA 8 18 1999 WARNING Disconnect primary power prior to servicing...
Страница 104: ...K 2 888 2314 001 Rev AE 03 05 2002 WARNING Disconnect primary power prior to servicing...
Страница 105: ...Figure K 1 Interface Board Rev AE 03 05 2002 888 2314 001 K 3 WARNING Disconnect primary power prior to servicing...
Страница 108: ...L 2 888 2314 001 WARNING Disconnect primary power prior to servicing...