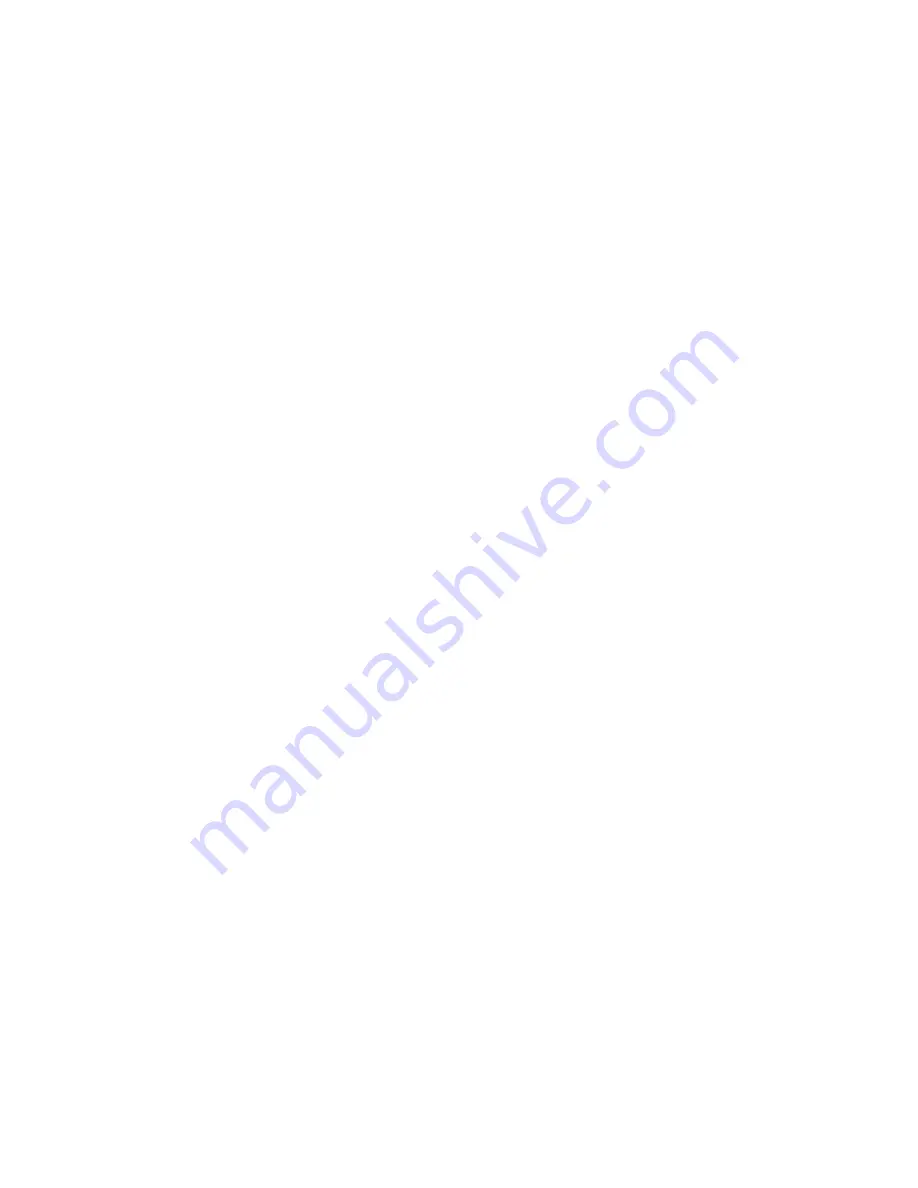
6
I N S T A L LA T I O N:
The control is usually mounted on the right side of the machine on the upper head or beside the main
transformer to maintain high quality earth ground on both machine and controller. The earth ground is best
achieved when an eight foot copper rod is driven into wet earth and #6 solid copper wire connects
the rod with the controller cabinet.
The P280 was designed with a PSIO board, which can be mounted piggy-back on the rear of the controller
or mounted externally, using the ribbon cable. (The revised versions have deleted the ribbon cable). A
small transformer is mounted on the PSIO board to allow only 120 volts AC to be present on the terminal
strip, not 240 or 480 volts AC. The higher voltage levels can now be kept away from the control and away
from operators when they enter the controller area.
The Interconnecting cables normally pass through the head of side skin. Therefore, no holes are punched
in the cabinet so each installation can be flexible. For control unit only, a 1.5 inch hole is ample for passage.
Control with SCR pack will require at least a 3 inch hole for signal cables as well as #4 cable or larger to
connect SCR, transformer, and line power input.
In the SEAM mode, an isolation relay will be required and may be mounted in the P280 cabinet or
externally. The relay must have a 120 vac coil and contacts capable of the requirements as needed for the
seam drive motor.
The signal and control wires for interconnections may be in the range of 22 to 18 gauge and stranded. These
circuits will require small current levels in the range of 5 vac. to 120 vac. The current required through the
firing device and the welding transformer will demand such larger cables and the correct size can be
obtained from the H&H Service Department. All wiring should avoid pinching or rubbing against moving
parts.
A key operated Program Lock can be provided to prevent unauthorized access to programs in memory.