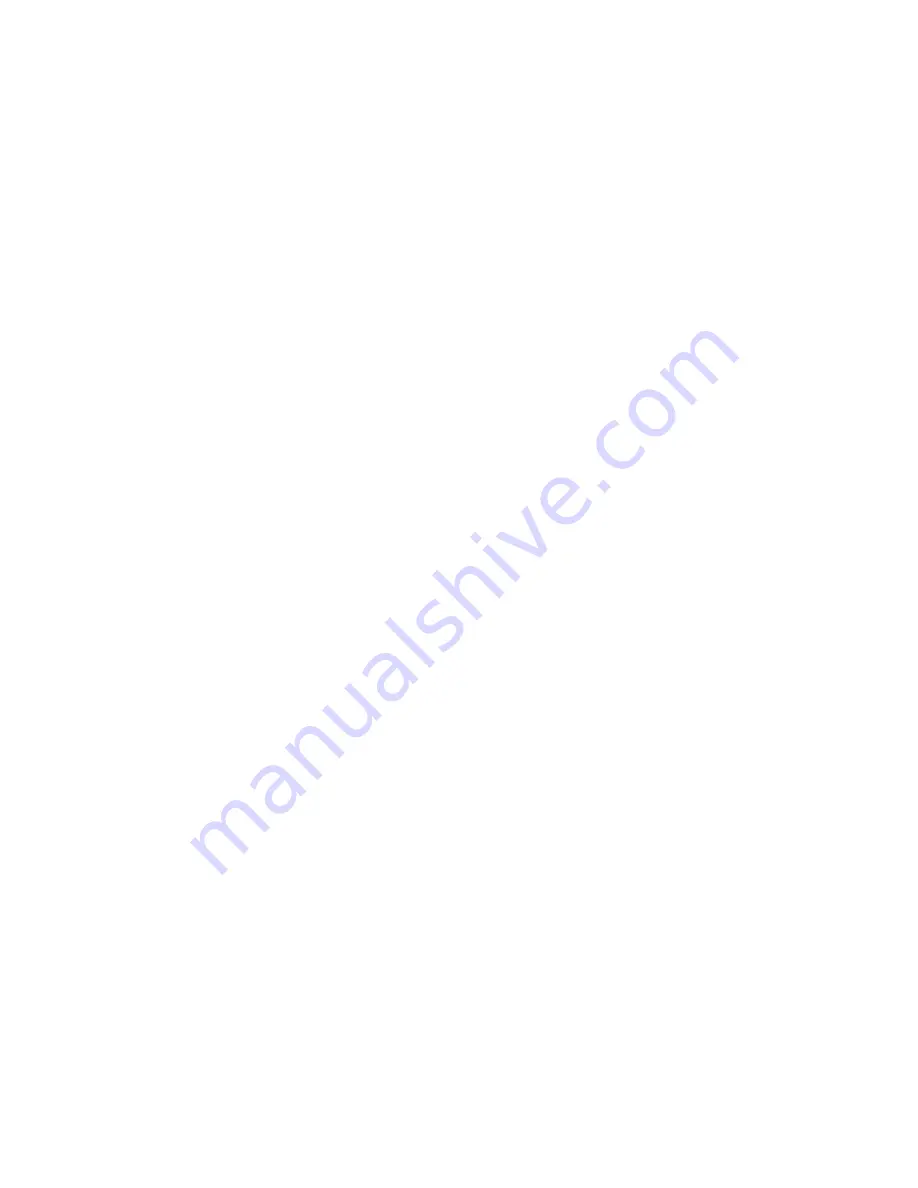
25
DEFECTS
Any good manufacturing process requires a good inspection and control system to judge the quality
and consistency of results and to take appropriate action when quality falls below a pre-set standard. Spot
welding is a good production tool which will yield consistency of result in the same order of magnitude as
results for latches, screw machines or punch presses. Unfortunately, the means of testing spot welds are
not as simple as the use of a micrometer caliper and the results noted are not as easy to interpret and to
correct for.
Under certain conditions, the following defects can be found in spot welds:
1. Surface burning or spitting.
2. Expulsion.
3. Excessive indentation.
4. Distortion.
5. Porosity.
6. Cracking.
7. Intergranular melting (coring)
8. Mis-placed nugget.
9. Mis-shaped nugget.
10. Low strength.
SURFACE BURNING CAN BE CAUSED BY:
1. Dirty material or fouled electrodes.
2. Too much penetration of nugget.
3. Improper machine sequence.
Usually simple visual inspection will be sufficient to observe surface burning. To eliminate, clean the
material or replace the electrode, or reduce the current, or see that the current is turned off before the
machine pressure is released.
EXPULSION CAN BE CAUSED BY:
1. Welding to near edge.
2. Welding on dirty material.
3. Welding with too little pressure or too much current.
4. Using the machine pressure to form the parts.
Simple visual examination, particularly at the time of welding, will disclose expulsion, although it can be
seen and tensile shear teats and in other destructive tests. To eliminate, use a wider flange and be careful
of fit of parts; clean the material, decrease the current or increase the pressure and use the proper electrode
diameter and contour for the material being welded
EXCESSIVE INDENTATION CAN BE CAUSED BY:
1. Too long of welding time.