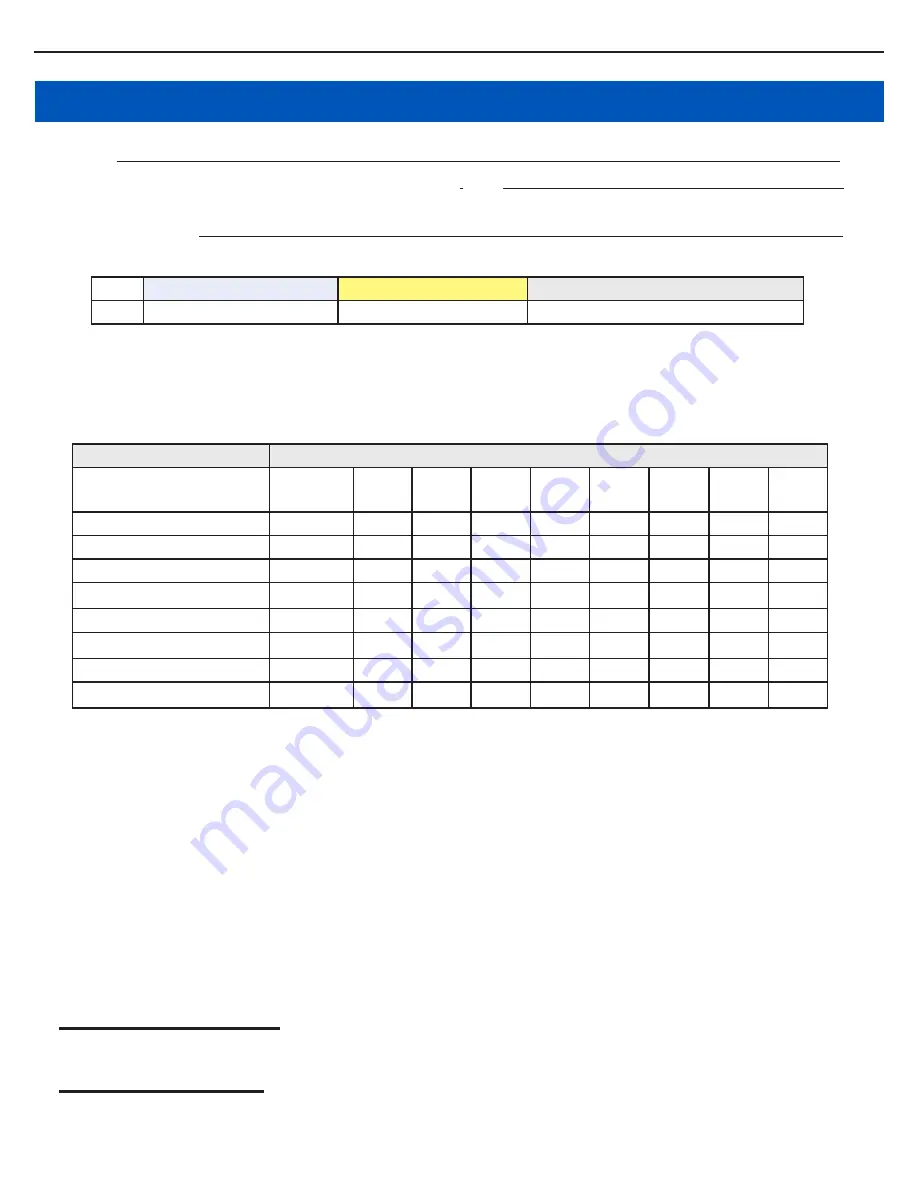
COMPRESSOR INSTALLATION & START-UP GUIDE
REVISION M
39
Hanbell Maintenance
Company ________________________________________________________________________________________________
Technician _______________________________________________ Phone _____________________________________________
Site Information
Installation Site Name ___________________________________________________________________________________
Unit Information - USE A SEPARATE SHEET FOR EACH COMPRESSOR
Model Number
Serial Number
Type Oil Used
Unit
Factory recommends that the oil filter cartridge should be checked and cleaned at 24 hours after startup.
Then checked or replaced at 10,000 hours then every 10,000 of run time.
It is important that the oil filter cartridge is not clogged; it might result in the malfunction of the lubrication systems,
bearings and capacity control system.
Recommended Maintenance Schedule
Check Point
Running Period
24
hrs.
1000
hrs.
2500
hrs.
5000
hrs.
10000
hrs.
15000
hrs.
20000
hrs.
25000
hrs.
30000
hrs.
Motor Insulation
0
0
0
Oil Filter Cartridge
0
0
0
0
Suction Filter
0
0
Piston Rings
0
0
0
0
0
0
/
Oil Level
0
0
0
0
0
0
0
0
0
Oil Change
0
0
Discharge PTC
0
0
0
0
0
0
Bearings
0
0
0
/
0
Check or Clean,
Replace
Note:
This is an estimated schedule to keep the compressor running at its highest efficiency and avoid compressor breakdown, not a basis
for any claim. The appropriate running period for each checkpoint will be vary from working conditions, applications, control logics,
refrigerant, lubricant, etc. Please contact Hanbell or local distributors/agents for more details.
Replacement of piston rings and bearings should be performed by HANBELL authorized technicians.
Every 5000hrs, please ensure the chiller unit keeps its target temperature when discharge superheat is between 10°C and
20°C; Please check vibration level of bearings in compressor every 10000hrs.
Oil Change; use only Hanbell authorized HBR lubricant and do not mix difference brands of the oil together. Oil remaining in the
compressor and system should be totally evacuated prior to changing the oil. It may be necessary to change the compressor oil a
second time to ensure that there is no oil mix.
It is critical to change the oil after a motor burned out because acid and debris may still remain inside the system. Check acidity of the
oil after several hours of operation and continue to perform periodic oil / filter-dryer changes until acidity drops to an acceptable level.
If the burn out is severe, a suction-line filter/dryer and an oversized liquid-line drier should be installed. The filters should be monitored
and replaced if a pressure drop across them is observed. Filters should be replaced until acidity drops to an acceptable level at which
time the suction-line filter can be removed.
Weekly Preventive Maintenance
Check oil level and color
Check the operation of oil heater and solenoid coil
Monthly Preventive Maintenance
Perform weekly preventive maintenance
Check compressor suction pressure
Check compressor discharge pressure
Check entering water temperature
Check leaving water temperature
Measure ambient temperature
Check compressor amp.
Chapter - 19. Hanbell Maintenance Forms
Содержание RC2 Series
Страница 8: ...COMPRESSOR INSTALLATION START UP GUIDE REVISION M 8 Chapter 5 Wiring Procedures Y Delta Part Winding...
Страница 10: ...COMPRESSOR INSTALLATION START UP GUIDE REVISION M 10 Figure 5 A Motor Wiring...
Страница 16: ...COMPRESSOR INSTALLATION START UP GUIDE REVISION M 16 Chapter 8 RC2 100 140 Installation Guide...
Страница 17: ...COMPRESSOR INSTALLATION START UP GUIDE REVISION M 17 Chapter 9 RC2 170 580 Installation Guide...
Страница 18: ...COMPRESSOR INSTALLATION START UP GUIDE REVISION M 18 Chapter 10 RC2 710 930 Installation Guide...