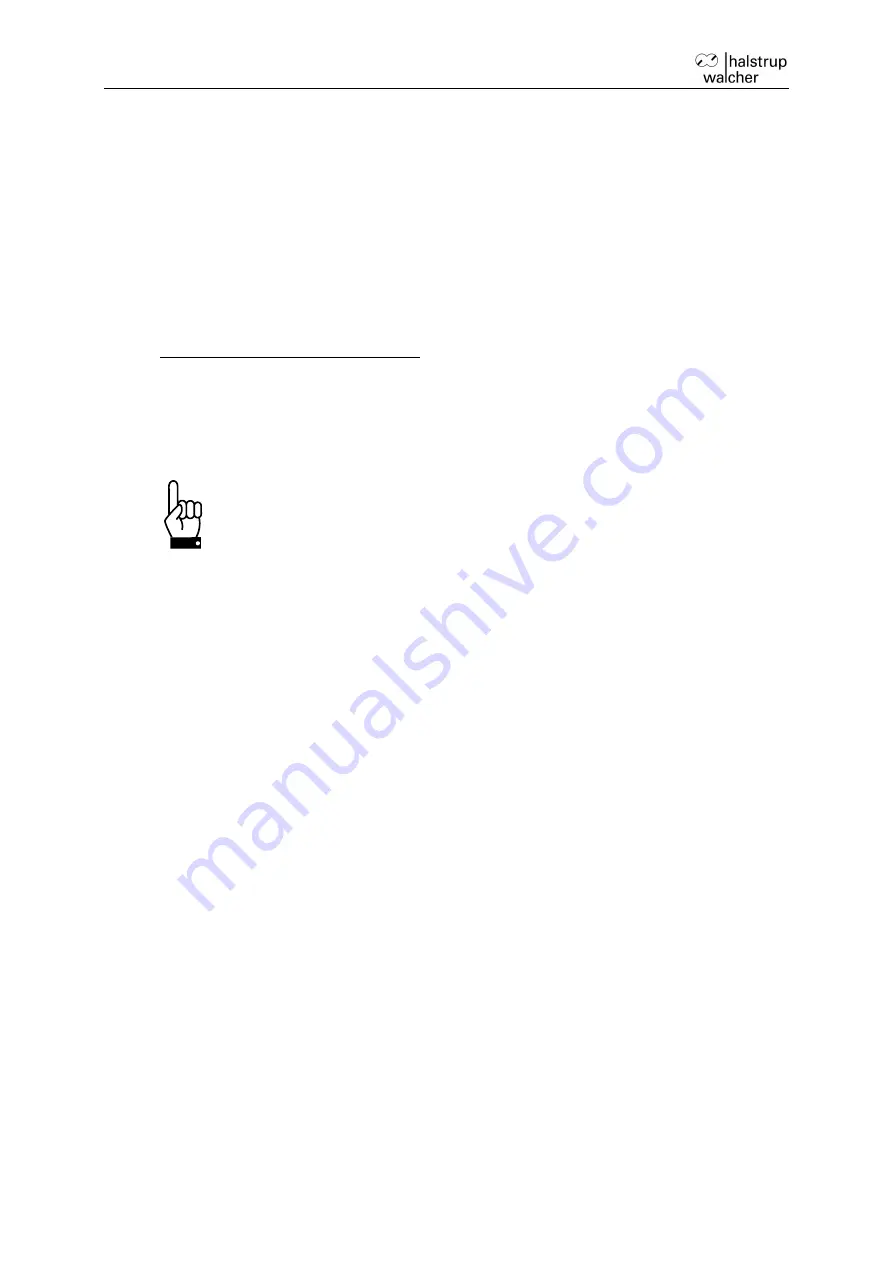
Instruction Manual PSE2xxDN
8
2.
New position value is smaller than the current value: The device reverses an
additional 5/8 of one rotation and approaches the exact position after resuming
forward motion.
3.
New position value after reverse run without loop: The device always approaches
the position by moving in forward direction; if necessary, it will first reverse by 5/8
of a rotation.
Once the target position has been reached, the device compares it to the internal
absolute encoder status. If a discrepancy is detected, the device then sets
the “Flash
memory or encoder error
” bit (bit 9 in the status word).
Positioning sequence (without loop)
The “positioning without loop” mode is used primarily for moving the small distances
involved in fine adjustments. In this case, each position is approached directly. This
does NOT eliminate any play present in the spindle in question. The PSE2xxDN
internal gear backlash does not play a role in this case, as position data are acquired
directly at the output shaft.
Runs which involve specifically a block run (e.g. reference runs on block),
may only be started with reduced torque (max. torque max. 10% of the
nominal torque).
2.7
CAN Bus
A DeviceNet protocol corresponding to ODVA CIP Networks Library Volume One
Edition 3.1 and Volume Three Edition 1.3 is the protocol used for the CAN bus
interface:
A group 2 server with UCMM support
2 explicit connections to the master
4 fixed mapping assemblies
I/O messages via poll, bit strobe and change-of-state/cyclic
Multicast poll is not supported
Heartbeat, default = inactive
DeviceNet LED that displays status as follows:
off:
either the device is switched off or no CAN bus is connected
green, steady:
CAN communication OK, device operational
green, flashing:
either no UCMM connection to the master or no learning run has been
performed
red, flashing:
relatively minor error, at least one I/O connection has timed out
red, steady:
major error, e.g., bus conflict with another station
red-green, flashing:
communication error