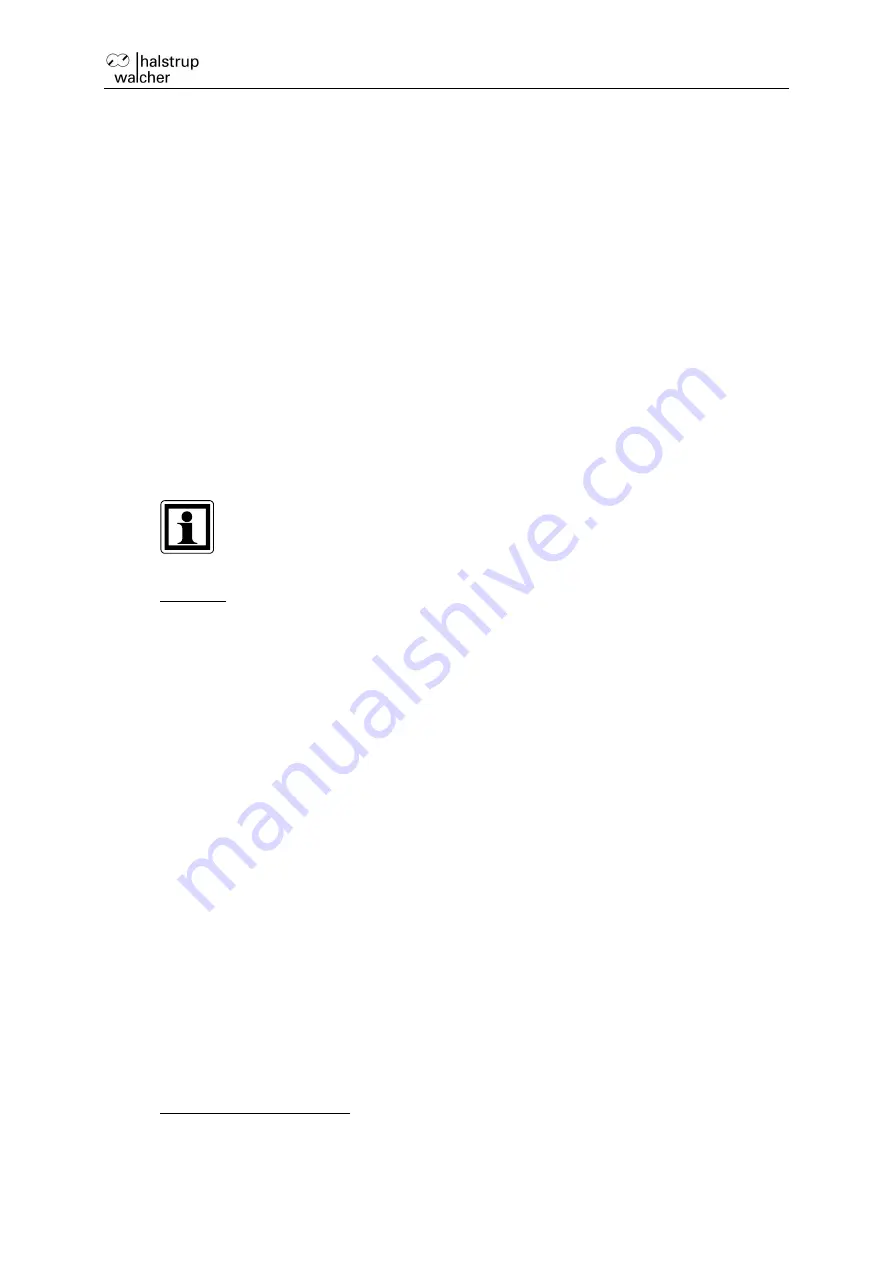
Instruction Manual PSE2xxDN
25
or if the actual position value changes during standstill. The value is available after
power up without further commands.
There are two cases that cause the counted turns to be invalid:
1) The output shaft is externally displaced during control power off for more than 36°.
2) Control power is turned off while the PSE2xxDN is turning.
In these cases attr. 42 of the PSE object (class 100, instance 1) has value 0
(“actual
position is not consistent”).
Now there are three possible ways to continue depending on the amount of
displacement during control power off:
1) No special actions have to be taken if the displacement has been less than 180°
(½ turn): The actual position value is still correct.
2) If the displacement has been more than 180° (½ turn), the correct actual position
value has to be sent to the PSE2xxDN (by writing to attr. 3).
3) First move to a reference position, then write the actual position value with attr. 3
(if the displacement has been more than ½ turn and the actual position is not
available otherwise).
The removal of the
motor
power supply has no affect on the internal
measuring system.
Remarks:
1) The 3 attributes referencing value (attr. 4), actual value assessment, numerator
(attr. 16) and actual value assessment, denominator (attr. 17) have an influence on
the increment and position values: With the help of the referencing value a shift
can be reached, with the help of the actual value assessment numerator and
denominator a stretching or distension can be reached (see below).
2) When changing the direction of rotation (attr. 44), the referencing value (attr. 4)
and the upper and lower limit (attr. 22 and 23) are set to delivery state.
3) When changing the actual value assessment numerator (attr. 16) or denominator
(attr. 17), the target value, the actual value, the referencing value, the upper and
lower limit, the positioning window (attr. 6) and the length of loop (attr. 31) are re-
calculated.
4) When changing the referencing value (attr. 4), the target value, the actual value
and the upper and lower limit are re-calculated.
5) If the user wants to go over any automatic re-calculation of values when setting up
the device, the optimum order of transfering the parameter is the following:
a) direction of rotation (attr. 44),
actual value assessment, numerator (attr. 16),
actual value assessment, denominator (attr. 17)
b) referencing value (attr. 4)
c) upper limit (attr. 22),
lower limit (attr. 23),
positioning window (attr. 6),
length of loop (attr. 31)
6) In order to save the settings permanently in the EEPROM, write 1 to attr. 79. As
soon as reading of attr. 79 shows 0, the saving is finished.
Referencing value (attr. 4):
The referencing process affects all transferred values, i.e., the target value, actual
value and upper and lower limit.
There are two ways of setting the referencing value: