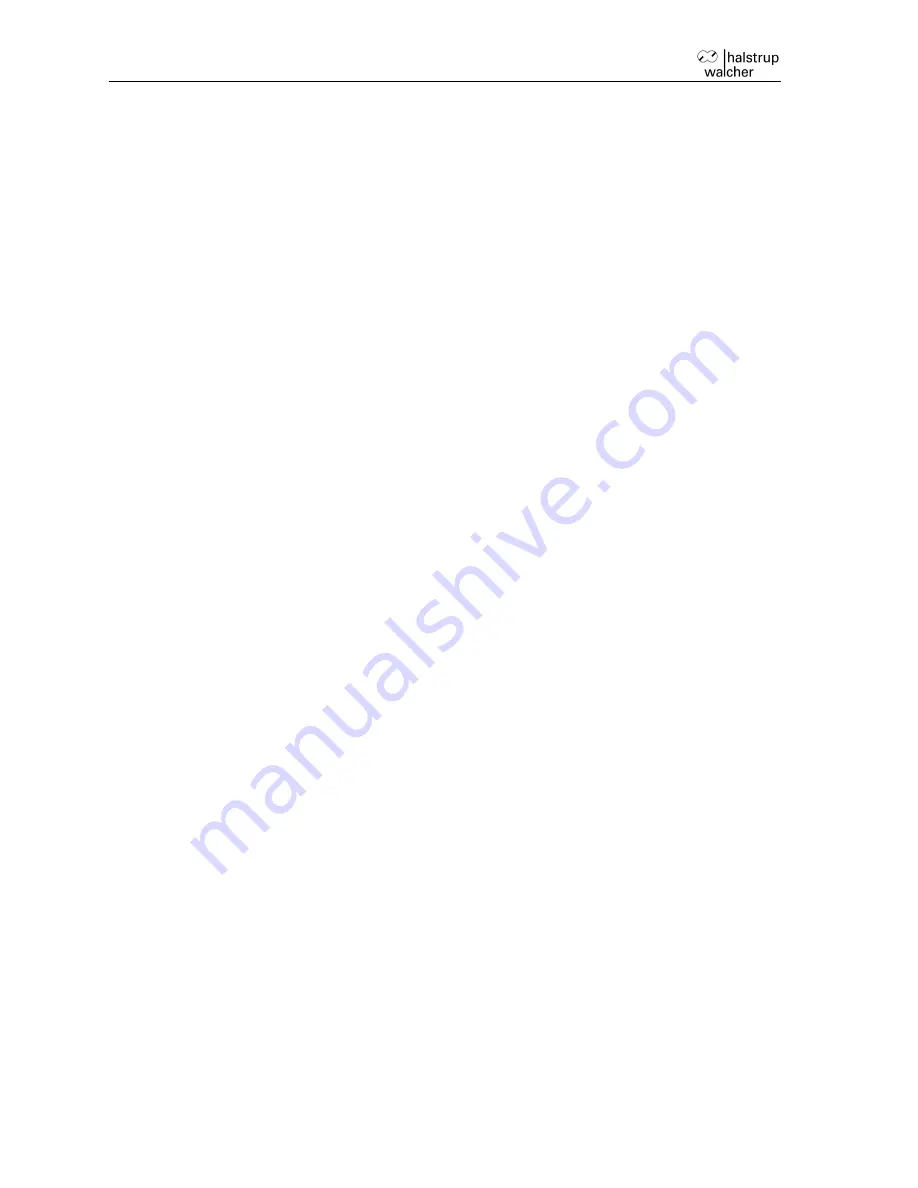
PSx3xxDP Instruction Manual
22
7.5.19 Holding torque
For many applications, the drive requires a level of holding torque greater than the very low self-
holding torque generated by the drive’s EC motor. This parameter allows the user to set that
holding torque value.
Current is then supplied to one of the motor windings when the drive is not operating. The level of
holding torque should be entered as a percentage of the nominal torque. The smallest possible
level of torque should be selected in order to prevent the drive from heating up unnecessarily,
which would reduce the OT.
7.5.20 Drag error
Because the load profile changes over the course of a positioning run, it sometimes happens that
the drive fails to reach its target rpm. This can lead to problems for applications involving the
synchronous operation of two drives. The ‘drag error’ bit will be set in the status byte if, over the
course of the run, the drive falls short of its theoretical position (target rpm * run time) by more
than the distance speci
fied by the ‘drag error’ parameter. The control unit can then often take
steps to correct the situation. If relatively short distances are involved, the drive itself will attempt
to compensate for the discrepancy by raising its speed by a small amount (+/- 1 rpm). This
corrective function can be deactivated by setting the drag error distance to zero.
7.5.21 Min. rpm for detecting an obstacle
The drive registers an obstacle if the actual rpm = 0 or if the drive speed falls below a certain
percentage of the target rpm for a specific amount of time. This parameter allows the user to set
that percentage value. If the instrument detects an obstacle, the current positioning run will be
aborted and the ‘positioning error’ and ‘positioning run aborted’ bits are set in the status byte.
7.5.22 Time required to detect an obstacle
This parameter specifies how long the drive speed must be less than the minimum rpm described
above before the instrument registers an obstacle.
7.5.23 Wait time between runs
The parameter specifies the minimum amount of time (in ms) that the drive will pause before
reversing its course.
7.5.24 Min. supply voltage
This parameter indicates the voltage at which the ‘motor supply voltage’ bit in the status byte is
activated. No positioning runs can be executed if this bit is not activated. When setting the
voltage level, it is important to consider that, due to a number of different components, the power
supply to the motor is lower than the voltage applied externally. The positioning sequence will not
be aborted if the power supply falls below the required voltage by only a small amount during a
run.
7.5.25 Filter value for voltage monitoring
This parameter allows operators to bridge brief voltage dips, such as may occur as a result of the
initial current. The ‘motor supply voltage OK’ bit is only set when the voltage dip lasts longer than
the amount of time specified in this parameter.
Содержание PS*3**DP series
Страница 31: ...PSx3xxDP Instruction Manual 31...