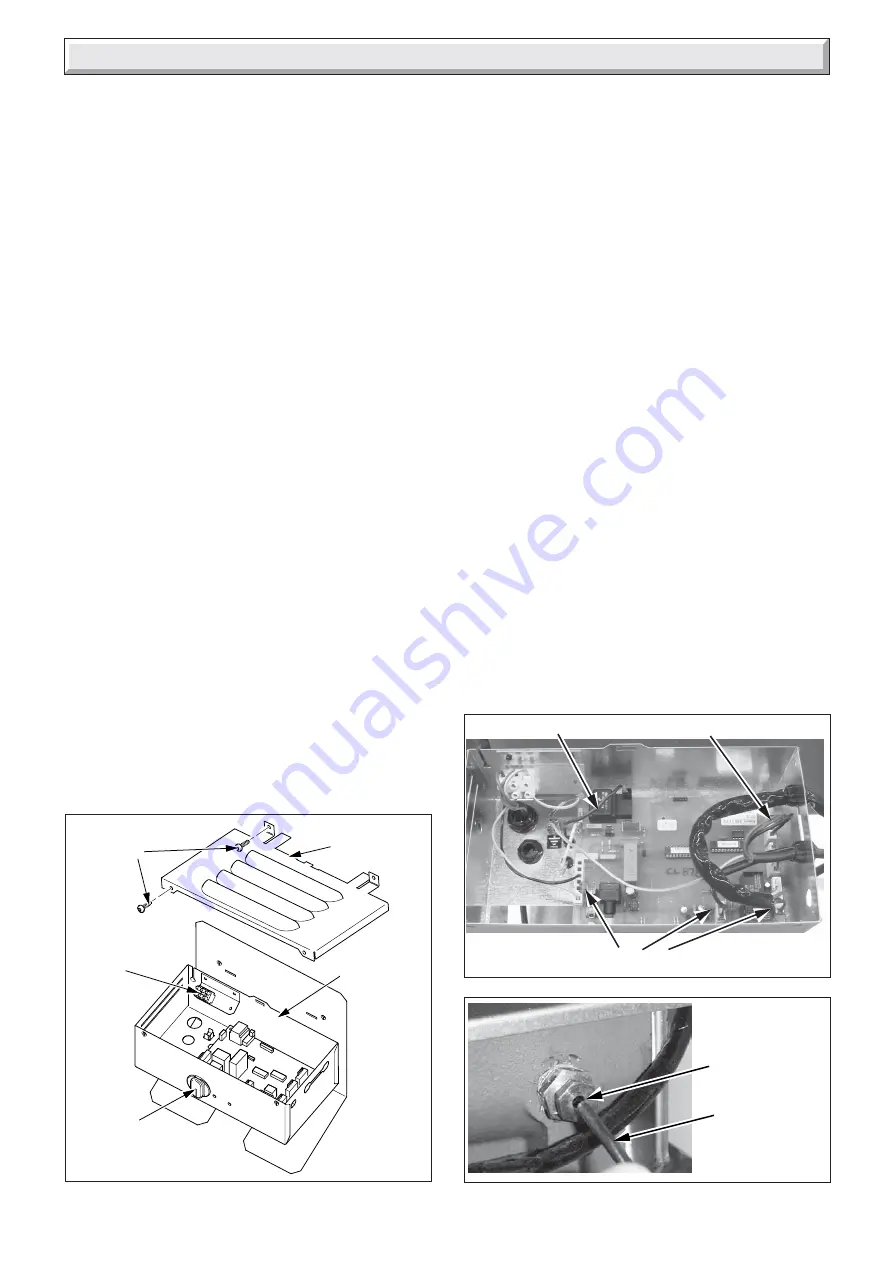
25
20000225117B
10 Replacement of Parts
Important notes
REMEMBER, When replacing a part on this appliance, use only
spare parts that you can be assured conform to the safety and
performance specification that we require. Do not use
reconditioned or copy parts that have not been clearly authorised
by Halstead Boilers Ltd.
Replacement of parts must only be carried out by a competent
person.
Before removing or replacing any parts, turn off the gas supply at
the gas service cock, see diagram 8.2 and isolate the electrical
supply to the appliance.
Unless stated otherwise, all parts are replaced in the reverse
order to removal.
After replacing any parts always test for gas soundness and if
necessary carry out functional check of controls.
10.1 Electrical Thermistor
Remove front panel to gain access, see section 6.8.
Remove control box cover by undoing the four securing screws
(two on control box, two on the heat shield) and lift off, see
diagram 10.1.
Remove thermistor lead from retaining clip, located on the control
box support bracket, see diagram 8.3.
Release strain relief grommet securing thermistor lead at the side
of control box.
Disconnect the thermistor electrical plug from the control board
(P.C.B) slightly bending back the retaining latch to allow
withdrawal, see diagram 10.2.
Remove the retaining wire and withdraw the electrical thermistor
from its phial, see diagram 10.3.
Draw the thermistor lead followed by the thermistor out though
the control box case.
Re-assembly note. When fitting the thermistor make sure it is
fully inserted into the phial, see diagram 10.3. Take care when
re-threading retaining wire so as not to damage thermistor.
10.2 Control Board (P.C.B)
Remove front panel to gain access, see section 6.8.
Remove control box lid by undoing the four securing screws
(two on control box, two on the heat shield) and lift off, see
diagram 10.1.
Carefully pull the boiler temperature control knob away from the
P.C.B.
CONTROL
BOX
COVER
CONTROL
BOX
SECURING
SCREWS
TERMINAL
BLOCK
Diagram 10.1
9905
ELECTRICAL PLUGS
Diagram 10.2
PCB
Diagram 10.3
PHIAL
POCKET
THERMISTOR
BOILER
TEMPERATURE
CONTROL
Disconnect the electrical plugs from the control board (PCB)
slightly bending back the retaining latches to allow withdrawal,
see diagram 10.2.
Disconnect the ignition, sensing and earth leads.
Carefully pull the board away from its supports bending back
slightly the retaining latches.
When refitting refer to wiring diagram 9.4.
Take care when replacing the burner temperature control knob
by supporting the potentiometer on the P.C.B.
NOTE: Ensure jumper is in position 'B', refer to wiring diagram
9.4.
10.3 Ignition & Sensing Electrodes
Remove front panel to gain access, see section 6.8.
Refer to the relevant paragraphs of the servicing section to
remove the burner from combustion chamber.
To remove the electrode, unscrew from the retaining bracket,
see diagram 8.12.
Take the electrode out from below and disconnect the lead.
When removing and replacing the electrode take care not to
damage it.
When refitting, check spark gap, see diagram 8.12, 9.3 and 9.4.
10.4 Multifunctional Control
Remove front panel to gain access, see section 6.8.
Remove the securing screw and disconnect the electrical plug,
see diagram 10.4.
Disconnect the gas cock, on the left hand side.
Support the multifunctional control, remove the four screws (2
long, 2 short) from the flanged connection at the right hand side.
Remove and discard the original “O” ring from the flanged
connection and fit the new “O” ring supplied, into recess, before
fitting the replacement multifunctional control.
After assembly test for gas soundness and purge in accordance
with the current issue of BS6891or in IE, the current edition of
I.S.813 "Domestic Gas Installations".
ELECTRICAL PLUG