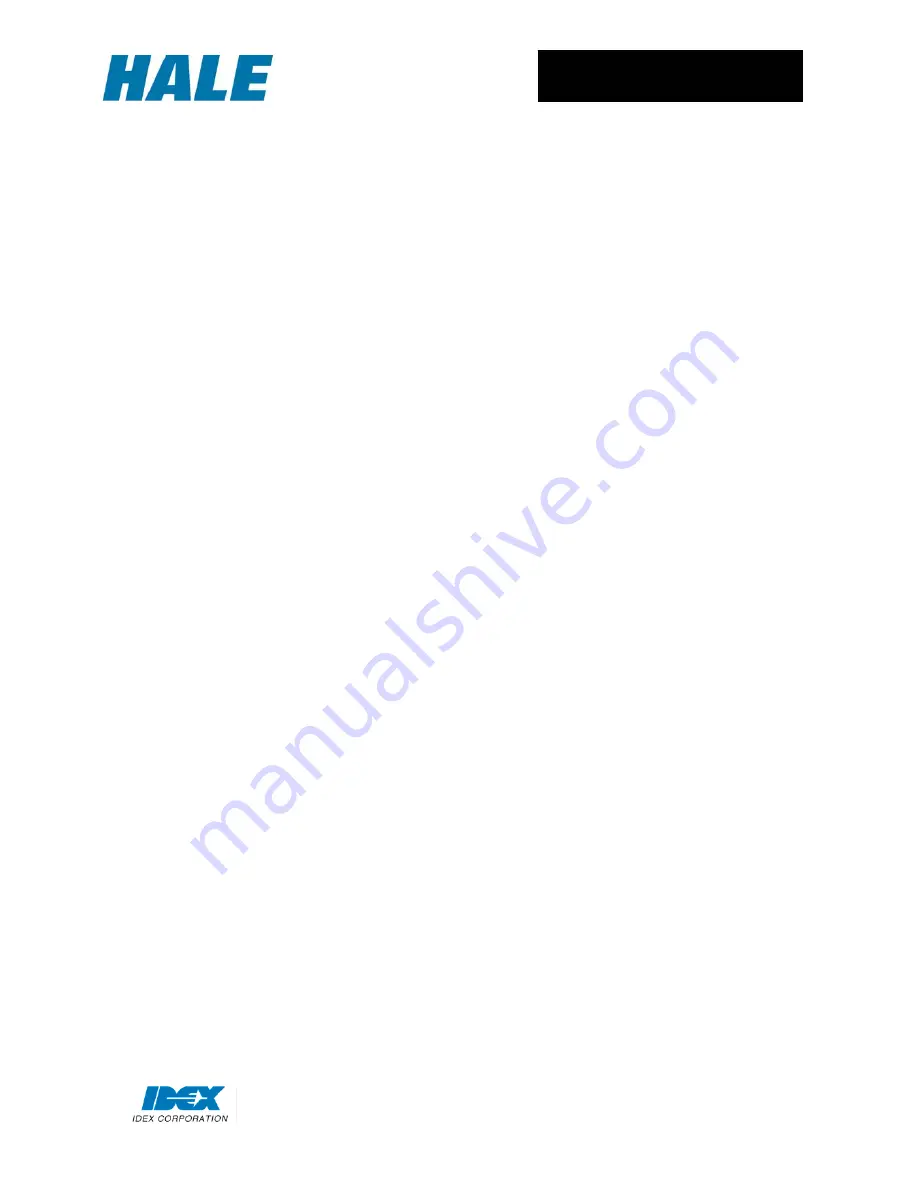
13
MiniCAFS 2.1A Operating Manual
GP/211/05 Issue 2. April 2005
©Hale Products Europe. Our policy is one of continuous development. We therefore
reserve the right to amend specifications without notice or obligation.
5. Connect a water supply of 4-10 bar pressure from the main pump to the inlet connection
on the MiniCAFS manifold. This should be of
φ
50, flexible, non-kinking hose. An isolating
valve must be provided between the vehicle pump and the MiniCAFS unit to prevent the
unit being pressurised when not being used.
6. Fill the engine with engine oil & fuel as per the Briggs & Stratton manual.
7. Fill the compressor with the correct grade of oil until the sight glass is 3/4 full.
8. Remove the battery, fill with electrolyte, fully charge to 12 volts and reconnect.
Note the battery connection leads, positive (+) is the red lead
(H),
the negative (-) the
black lead
(I)
,
9. The exhaust silencer of the MiniCAFS unit is provided with a DIN socket for an exhaust
extension hose. With the aid of such a hose, the exhaust gases can be conducted out of
the body of the vehicle and led away from the unit.
Caution
: Pressurised water must be supplied to the unit any time the engine
is run and must be circulating before the engine is switched on.
Caution:
The exhaust extension and the exhaust gases are very hot.
10. Following the Briggs & Stratton operator’s manual (attached at back of manual), start the
engine and run for 30 seconds to circulate the oil.
Note
: The engine has an electric start button located above the rocker ignition
switch and a recoil rope back-up starter for manual operation.
11. If the engine should stall after starting (especially from cold) it may be necessary to
relieve the pressure in the compressor by pressing the air dump valve (5, Page 7).
12. Shut the unit down and allow the oil to settle for 5 minutes.
13. Add additional oil as necessary to the engine to keep the oil level between the Max. and
Min. marks on the dipstick.
14. Add additional oil as necessary to the compressor to keep the oil at least 3/4 full in the
sight glass.
15. Note the location of the drain taps
(K)
for draining the system of water after use and
before storage, this is particularly necessary if freezing weather is expected.
The unit is now ready for commissioning of the foam proportioning and CAFS system.