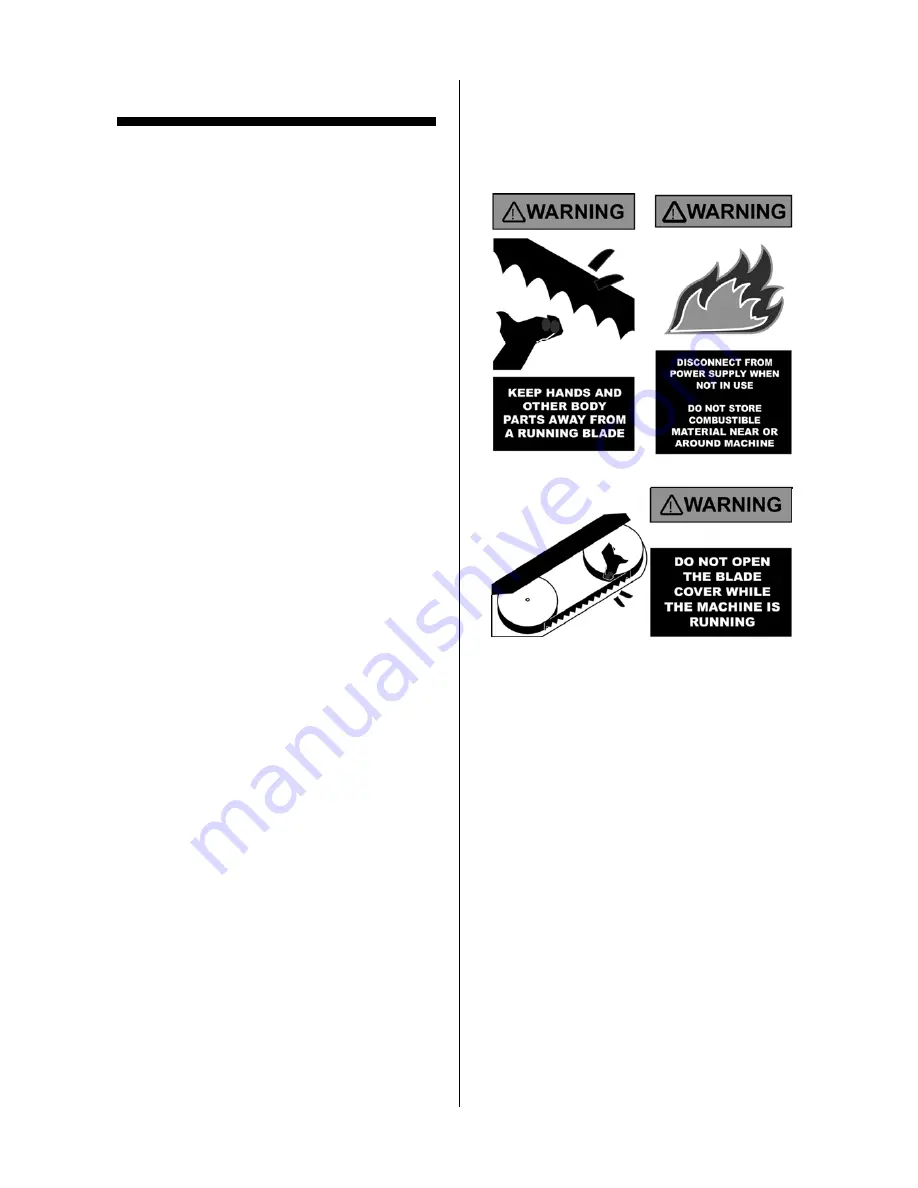
- In the event of a power cut, the specific start-up
button must be reset.
1
ACCIDENT PREVENTION AND
SAFETY REGULATION
- The machine has been tested in conformity with
point 20 of EN 60204
This machine has been designed to comply with
national and community accident- prevention
regulations. Improper use and/or tampering with
the safety devices will relieve the manufacturer of
all responsibility.
1.1
Advice for the operator
- Check, the line voltage is the same as the
voltage required by the machine’s motor.
- Check the efficiency of your electric supply and
grounding system; connect the power cable of
the machine to the socket and the ground lead
(yellow- green in color) to the grounding system.
- When the machine is in suspended mode (or
stopped) the blade must not move.
- Only the blade section used for cutting must be
kept unprotected. To remove guards to expose
more of the cutting blade adjust the blade
guides.
- It is forbidden to use the machine without its
shields
- Always disconnect the machine from the power
socket before blade change or carrying out any
maintenance job, even in the case of abnormal
machine operation.
- Always wear suitable eye protection.
- Never put your hands or arms into the cutting
area while the machine is operating.
- Do not shift the machine while it is cutting.
- Do not wear loose clothing like: shirts with
sleeves that are too long, gloves that are too big,
bracelets, chains or any other object that could
get caught in the machine during operation. Tie
back long hair.
- Keep the area free of miscellaneous object; i.e.
equipment, tools, etc…
- Perform only one operation at a time. Never
have several objects in your hands at the same
time. Keep your hands as clean as possible.
- All internal operations, maintenance or repairs,
must be performed in a well-lit area or where
there is sufficient light from extra sources to
avoid the risk of accidents.
1.2
The electrical equipment according to
European Standard" CENELEC EN
60204-1"
1.3
Warning labels
- The electrical equipment ensures protection
against electric shock as a result of direct or
indirect contact. The active parts of this
equipment are housed in a box to which access
is limited by screws that can only be removed
with a special tool; the parts are fed with
alternating current as low voltage (24V). The
equipment is protected against splashes of
water and dust.
- Protection of the system against short circuits is
ensured by means of rapid fuses and grounding;
in the event of a motor overload, protection is
provided by a thermal probe.
Replace warning labels if they become obscured
or removed.
- Keep hands and other body parts away from a
running blade.
- Do not open the blade cover while machine is
running.
- Do not store combustible materials near or
around machine.
- Always wear approved safety glasses/face
shields while using this machine.
- Keep machine guards in place at all times.
- Do not wear gloves.
- Remove loose clothing and confine long hair.
- Keep the work area clean and free
miscellaneous objects.
1.4
Emergencies according to European
Standard “CENELEC EN 60204-1”
- In the event of incorrect operation or a danger
condition, the machine may be stopped
immediately by pressing the red mushroom
shaped button.
NOTE: Resetting of machine operation after each
emergency stop requires resetting the emergency
stop button.
3
Instruction Manual for BS-460AS (B035)
31/03/2016
Содержание BS-460AS
Страница 17: ...17 Instruction Manual for BS 460AS B035 31 03 2016 ...
Страница 18: ...18 Instruction Manual for BS 460AS B035 31 03 2016 ...
Страница 19: ...19 Instruction Manual for BS 460AS B035 31 03 2016 ...
Страница 25: ...UE 460DSA 1000307 V4 25 Instruction Manual for BS 460AS B035 31 03 2016 ...
Страница 26: ...UE 460DSA 1000307 V3 26 Instruction Manual for BS 460AS B035 31 03 2016 ...
Страница 27: ...UE 460DSA 1000307 V3 27 Instruction Manual for BS 460AS B035 31 03 2016 ...
Страница 28: ...UE 460DSA 1000307 V3 28 Instruction Manual for BS 460AS B035 31 03 2016 ...
Страница 29: ...UE 460DSA 970912 V2 29 Instruction Manual for BS 460AS B035 31 03 2016 ...
Страница 30: ...UE 460DSA 1000622 V1 30 Instruction Manual for BS 460AS B035 31 03 2016 ...