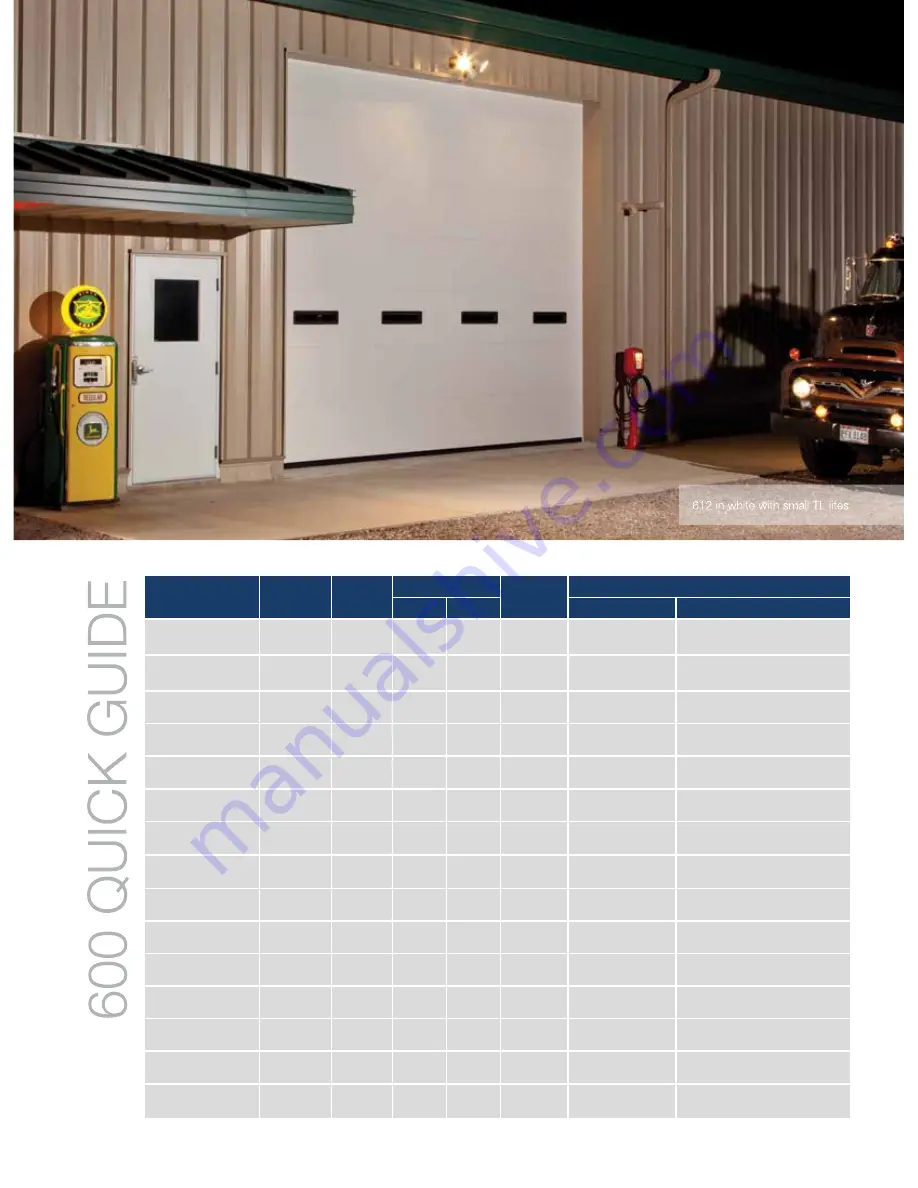
Model
Door
Thickness R-Value*
Max. Door Size
End Stile
Type
Section Skins
Width
Height
Inside
Outside
610
1-3/8”
(34.9mm)
13.45
18’-2”
16’-0”
Extruded
End Cap
26 GA V-Groove
Woodgrain Steel
26 GA Flush
Woodgrain Steel
612
1-3/8”
(34.9mm)
13.45
18’-2”
16’-0”
Extruded
End Cap
26 GA V-Groove
Woodgrain Steel
26 GA V-Groove
Woodgrain Steel
614
1-3/8”
(34.9mm)
13.45
18’-2”
16’-0”
Steel
26 GA V-Groove
Woodgrain Steel
26 GA Flush
Woodgrain Steel
616
1-3/8”
(34.9mm)
13.45
18’-2”
16’-0”
Steel
26 GA V-Groove
Woodgrain Steel
26 GA V-Groove
Woodgrain Steel
632
1-3/8”
(34.9mm)
13.45
18’-2”
16’-0”
Steel
26 GA V-Groove
Woodgrain Steel
20 GA Flush
Smooth Steel
633
1-3/8”
(34.9mm)
13.45
18’-2”
16’-0”
Steel
26 GA V-Groove
Woodgrain Steel
20 GA V-Groove
Smooth Steel
632-20
1-3/8”
(34.9mm)
13.45
18’-2”
16’-0”
Steel
20 GA V-Groove
Smooth Steel
20 GA Flush
Smooth Steel
633-20
1-3/8”
(34.9mm)
13.45
18’-2”
16’-0”
Steel
20 GA V-Groove
Smooth Steel
20 GA V-Groove
Smooth Steel
660, 672, 682
1-3/8”
(34.9mm)
13.45
18’-2”
16’-0”
Extruded
End Cap
26 GA V-Groove
Woodgrain Steel
26 GA Ribbed Short Panel
Woodgrain Steel
661, 671, 681
1-3/8”
(34.9mm)
13.45
18’-2”
16’-0”
Extruded
End Cap
26 GA V-Groove
Woodgrain Steel
26 GA Recessed Short Panel
Woodgrain Steel
663 673
1-3/8”
(34.9mm)
13.45
18’-2”
16’-0”
Extruded
End Cap
26 GA V-Groove
Woodgrain Steel
26 GA Recessed Long Panel
Woodgrain Steel
664 674
1-3/8”
(34.9mm)
13.45
18’-2”
16’-0”
Extruded
End Cap
26 GA V-Groove
Woodgrain Steel
26 GA Ribbed Long Panel
Panel Woodgrain Steel
670
1-3/8”
(34.9mm)
13.45
18’-2”
16’-0”
Extruded
End Cap
26 GA V-Groove
Woodgrain Steel
26 GA Ranch Panel
Woodgrain Steel
680
1-3/8”
(34.9mm)
13.45
18’-2”
16’-0”
Extruded
End Cap
26 GA V-Groove
Woodgrain Steel
26 GA Raised Panel
Woodgrain Steel
690
1-3/8”
(34.9mm)
13.45
18’-2”
16’-0”
Extruded
End Cap
26 GA V-Groove
Woodgrain Steel
26 GA Sculptured Panel
Woodgrain Steel
*calculated R-Value
Содержание 610
Страница 1: ...COMMERCIAL COMMERCIAL SERIES OPERATION MAINTENANCE MANUAL COMMERCIAL 600 SERIES ...
Страница 2: ......
Страница 3: ......
Страница 5: ......