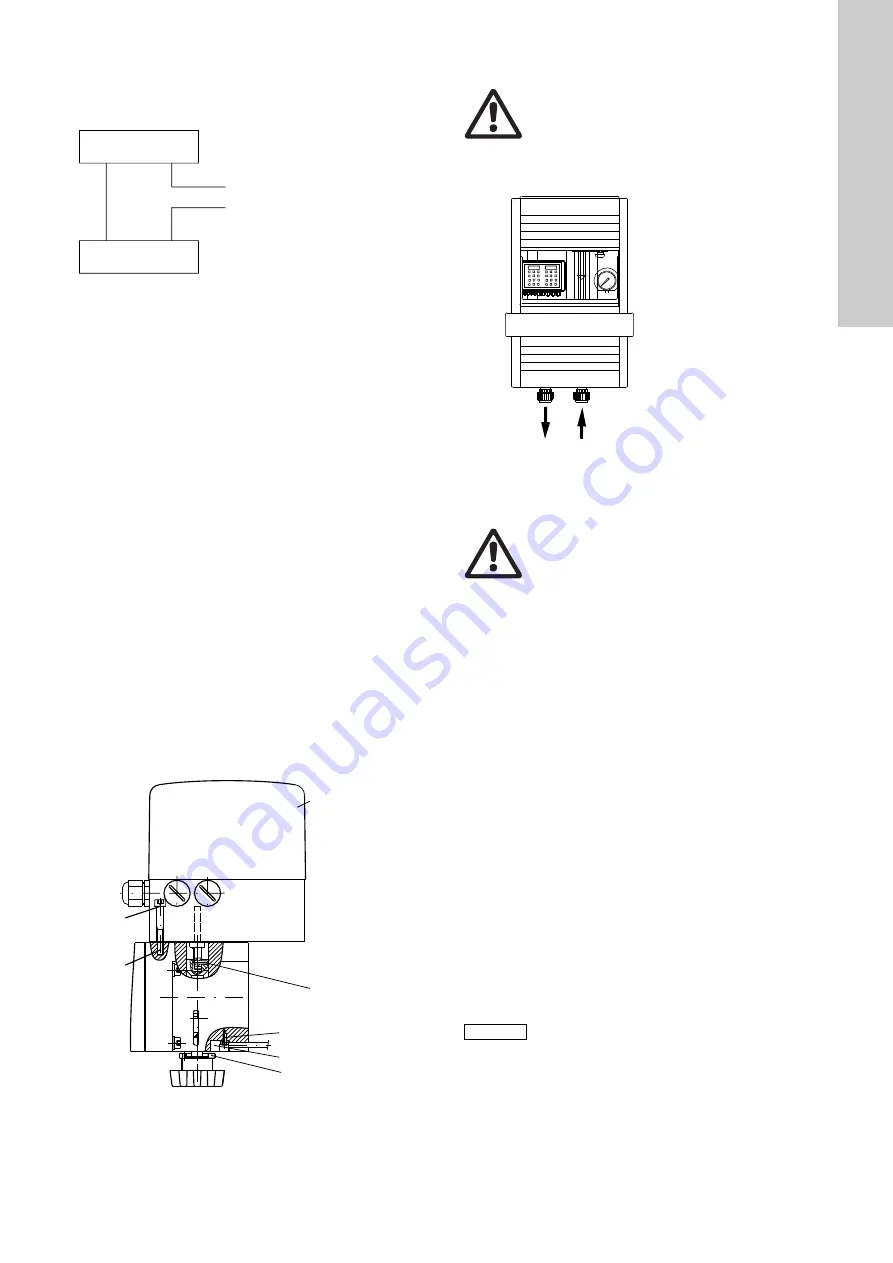
English (GB)
17
Measuring transducer (option)
• Connect the terminals of the plug with the corresponding
terminals of an external evaluation device according to the
connection chart.
Fig. 24
Connection chart of measuring transducer
5.1.3 Measurement and Control Electronics Conex (option)
• see operation manual of measuring amplifiers and controller
Conex
®
DIA-2Q or controller Conex
®
DIS-2Q
5.1.4 Chlorine measuring cell (option)
• see operation manual of the chlorine measuring cell
5.1.5 Mounting the manual/automatic position remote
indication at the rate valve
This indication shows e.g. in the switch room, if the optional
servomotor is engaged and thus able to convert the incoming
signals.
• Loosen the cover of the adjustment knob with a big
screwdriver; take off the adjustment knob.
• Put the magnetic bridge sensor (item 5.6) into the lower cavity
of the gearbox bearing and fasten using the two recessed
head screws (item 5.7).
• Disassemble the adjustment knob by fully screwing out the
clamping nut.
• Insert the adjustment knob tongs into the washer disc (item
5.5) in a way that the tongs collar is in the washer disc.
• Apply the washer disc to the adjustment knob enclosure so
that the holding pin of the enclosure dips into the hole of the
washer disc.
• Slide the spring washer over the adjustment knob tongs and
screw the clamping nut onto the tongs.
• Put the adjustment knob onto the gearbox spindle as far as it
will go and tighten the clamping nut.
• Fit the cover of the adjustment knob again.
Fig. 25
Manual/automatic position indication
5.1.6 Gas connections
• Connect line from vacuum regulator
• Connect line to injector
Fig. 26
Gas connections of gas dosing systen VGS
5.2 Checks before commissioning
Check tightness of the total plant before start-up
5.2.1 Checking the gas solution lines and the diapgragm non-
return of the injector
• Observe the manual of the injector!
5.2.2 Checking the tightness of the vacuum lines
Vacuum lines are all lines between vacuum regulator and injector.
• Close all container valves
• Close the rate valve
• Open the shut-off valve at the injection unit
• Open motive water valve
• Switch on the booster pump
• Open the rate valve
Floater shows gas flow or vacuummeter shows more than -
9 m w.c. =>
Leakage in vacuum line!
• Close rate valve
• Switch off booster pump
• Close motive water valve
• Close the shut-off valve at the injection unit
• Check the vacuum lines and the connection. If necessary,
• carefully re-tighten them.
• Check tightness again!
– Floater shows no gas flow, vacuummeter shows -9 m w.c. or
less => Vacuum lines are tight.
TM
04
08
15
09
08
TM
04
0
859
09
08
24 V DC
+
-
2
1
4-20 mA
+
-
5.1
5.14
5.13
5.12
5.7
5.6
5.5
Warning
Ensure that all container valves are closed before
connecting!
Only use the intended gas lines!
TM
04
08
16
09
08
Warning
Check the tightness not until the total plant is ready
for start-up.
Danger of chlorine break-out!
Note
More possible reasons for insufficient operating
vacuum
• injector layed out too weakly or defective
• injector obstructed
• booster pump layed out too weakly or defective
to injector
from vacuum regulator