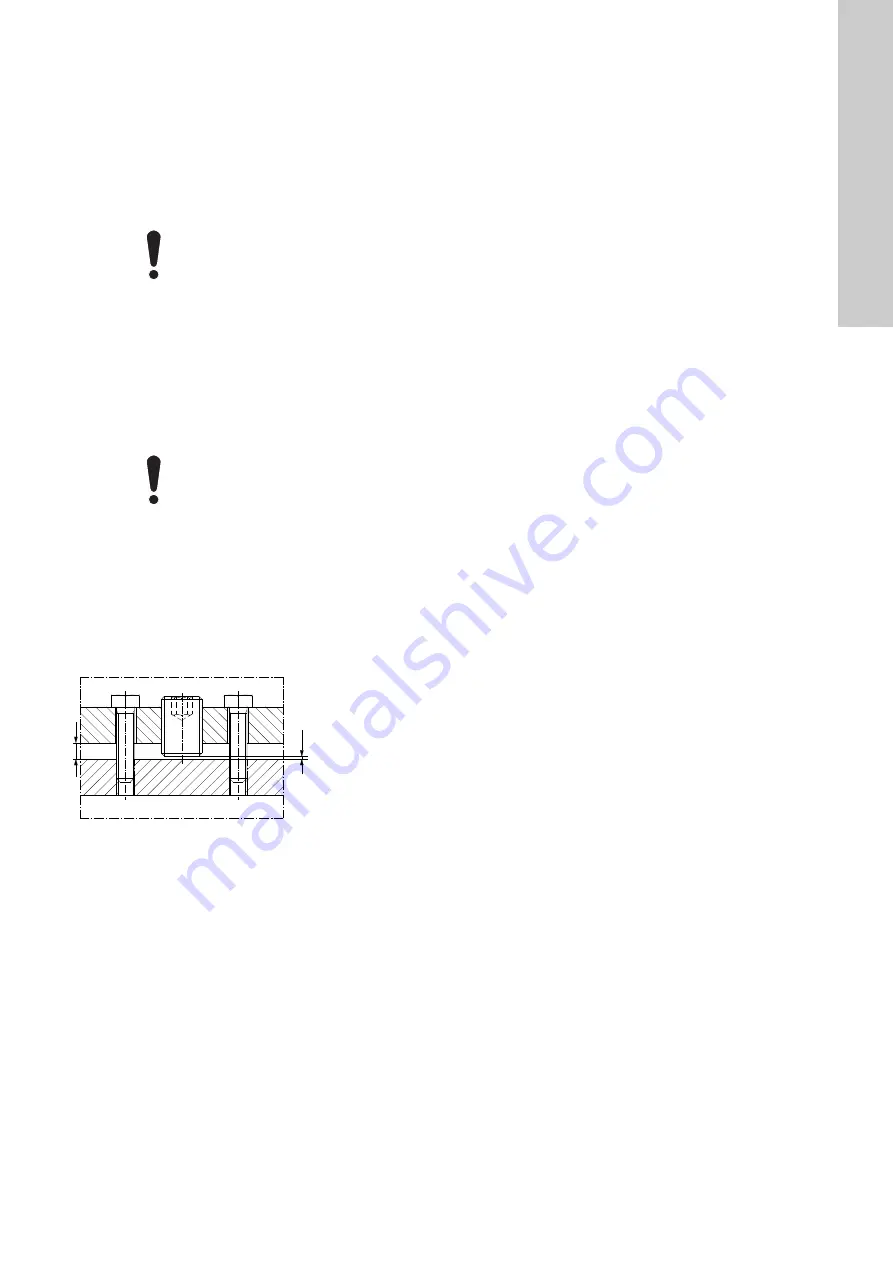
English (GB)
29
8.4.2 Dry-installed pumps, installation types D and H
Depending on the pump range, there are two ways to set the
impeller clearance. Method 1 is for ranges 50-54 and method 2
for ranges 58-70.
Method 1
1. Loosen the set screws by two full turns each.
2. Close the impeller clearance by lightly tightening the fastening
screws diagonally until the impeller touches the pump
housing.
3. Loosen the fastening screws to make an 0.7 mm gap under
the heads of the fastening screws. See fig.
4. Tighten the set screws tightly.
5. Tighten the fastening screws diagonally.
Method 2
1. Loosen the six fastening screws and close the impeller
clearance by tightening the three set screws. Tighten the
screws diagonally to move the inlet cover evenly.
2. Measure the distance "L" between inlet cover and pump
housing at three points next to the set screws, using feeler
gauges or callipers, and make a note of the distance.
3. Loosen the set screws and draw back the inlet cover by
between 0.5 and 0.9 mm using the six fastening screws
(approx. one 270 ° turn of an M12 fastening screw) and the
distance "L" as reference. See fig.
.
4. Tighten all set screws and check that the distance "L" at the
three reference points is stable at the new value.
Fig. 35
Impeller clearance adjustment
8.5 Pump cleaning and visual inspection
A simple maintenance measure is to clean the pumps at regular
intervals. Lift the pumps out of the wet pit and clean the pumps on
site. Hose down the pump externally using a high-pressure jet
cleaner at maximum 100 bar. Remove caked dirt from the motor
to ensure good heat conductivity. A mild detergent approved for
disposal into the sewage system may be used. The pumps may
be scrubbed, using a soft brush, if necessary.
Visual inspection of the pump must include the following points:
• Search for cracks or other external damage.
• Check the lifting bracket and lifting chain for wear and
corrosion.
• Inspect the motor cables for cracks or lacerations in the
sheath, for kinks or for other damage.
• Inspect visible parts of the cable entries for cracks.
• Check that the cables are firmly connected to the motor top
cover.
• Check all visible screws for self-loosening and tighten, if
necessary.
The pumps are fitted with a vent valve at the top of the cooling
jacket. The valve may be removed and cleaned, if necessary.
Clean the vent hole before refitting the valve after cleaning.
Do not use too much force when
tightening the fastening screws
as this may damage the bearings.
The movement is usually 1 to 3
mm.
Do not use too much force when
tightening the fastening screws
as this may damage the bearings.
The movement is usually 1 to 3
mm.
TM0
5
191
6
3
9
11
0.
5 -
L
Set screw
Fastening screw Fastening screw