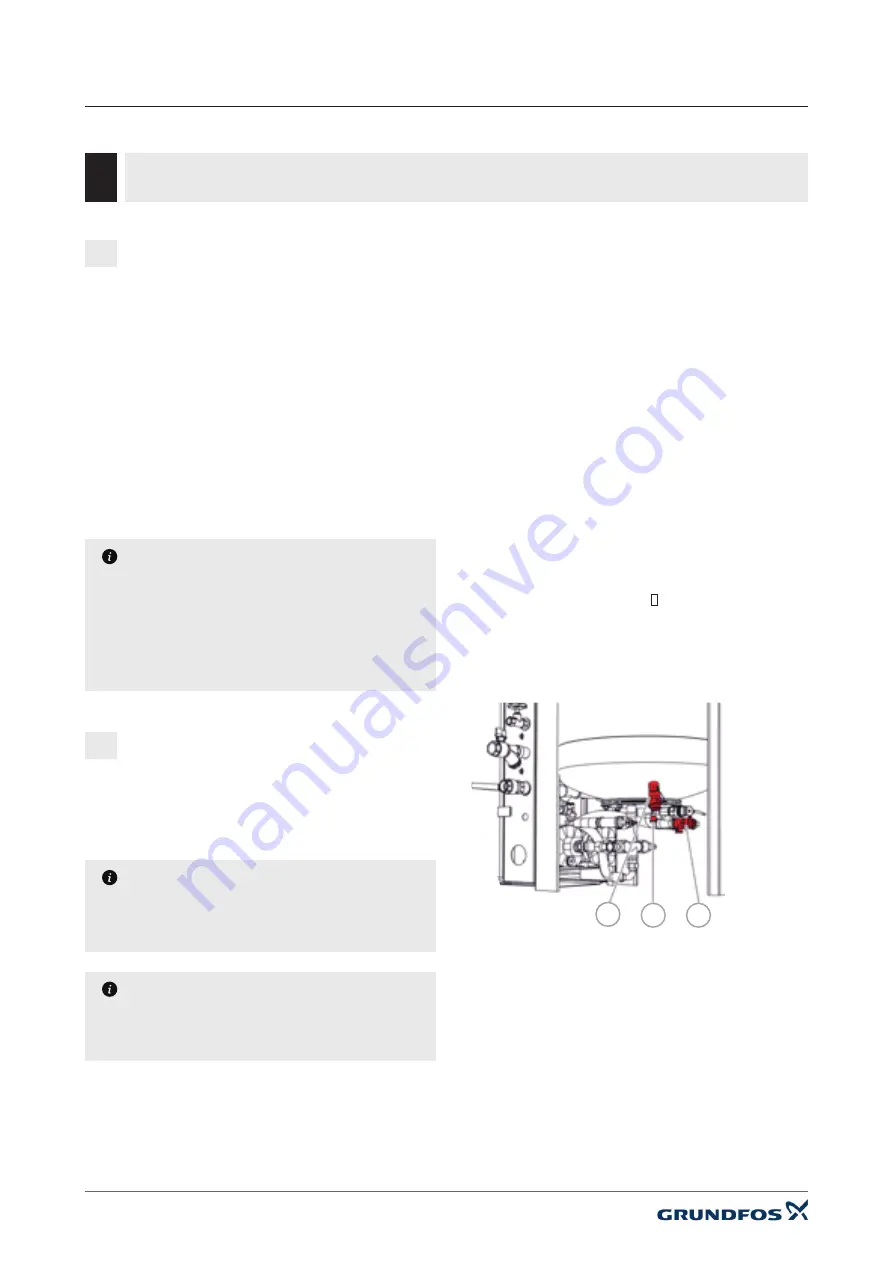
PHP A-1 Instruction Manual /
Cleaning and maintenance
8
Cleaning and maintenance
8.1 Cleaning
During operation, mud particles will be caught inside the
filter of the mud flap which is mounted at the connection
of the expansion overflow pipe. Due to these impurities the
flow rate through the mud flap decreases. This decrease
could lead to malfunctions of the device.
So the mud particles must be removed in periodic intervals
by dismantling and cleaning of the filter of the mud flap. This
check and cleaning of the mud flap must be done at least
two times a year. If any problems appear at the pressure
maintenance device, you should clean the mud flap at first.
Any problems or malfunctions caused by missing this
cleaning are excluded from any warranty.
8.2 Maintenance
Maintenance is required at least once a year or if the warning
W3 is displayed. The operator has do take care that this
maintenance will be done effectively.
RECOMMENDATION.
If problems with impurities appear frequently, further
tasks must be considered (e.g.) changing and flushing
of the plant media, installation of additional filters or
mud separators,...)
These measures affect positively to the entire plant, not
only to the pressure maintenance device.
NOTE
If this maintenance can‘t be done resp. isn’t intended to
be done by the operator himself, an adequate expert or
the Grundfos customer service must be assigned to do it.
INFORMATION
We recommend that the maintenance is executed by the
Grundfos customer service. In this case a conclusion of a
maintenance contract is highly recommended.
Any problems caused by missing the required maintenance
or maintenance intervals are excluded from any warranty.
Works that must be done in the course of a maintenance:
• Check and record, if the periodic cleaning acc. to 8.1 hast
been done, record the last cleaning. Clean the device
acc. to 8.1 in every case.
• Ask the operator and record, of there occurred
abnormalities or problems since the last maintenance.
If possible, resolve these problems.
• Look for the correct closure of the check valve(s).
• Look for the correct function and closure of the
overflow valve.
• Elutriate the vessel via the tap at the lower vessel flange
(1) resp. in the overflow pipe at the vessel.
• Open the drain tap (2) and discharge eventually existing
medium. If medium discharges permanently, the
membrane could be damaged Check the membrane.
• Flush the connection of the vessel pressure transmitter
(3). Open the black plastic plug and flush out of the vessel
until any impurities are removed. Then close the plug.
3
2
1
43
Содержание PHP A-1 4.0
Страница 1: ...PHP A 1 4 0 5 6 6 6 8 1 Instruction manual UK version original instructions...
Страница 5: ...PHP A 1 Instruction Manual Mounting 05 Figure 1 Changing the positions of the hydraulic connections...
Страница 12: ...PHP A 1 Instruction Manual Wiring diagrams 4 Wiring diagrams 12 4 1...
Страница 13: ...PHP A 1 Instruction Manual Wiring diagrams 13...
Страница 14: ...PHP A 1 Instruction Manual Wiring diagrams 14...
Страница 51: ...PHP A 1 Instruction Manual Appendix 51...
Страница 52: ...PHP A 1 Instruction Manual EC declaration of Conformity 52 13 EC declaration of Conformity...