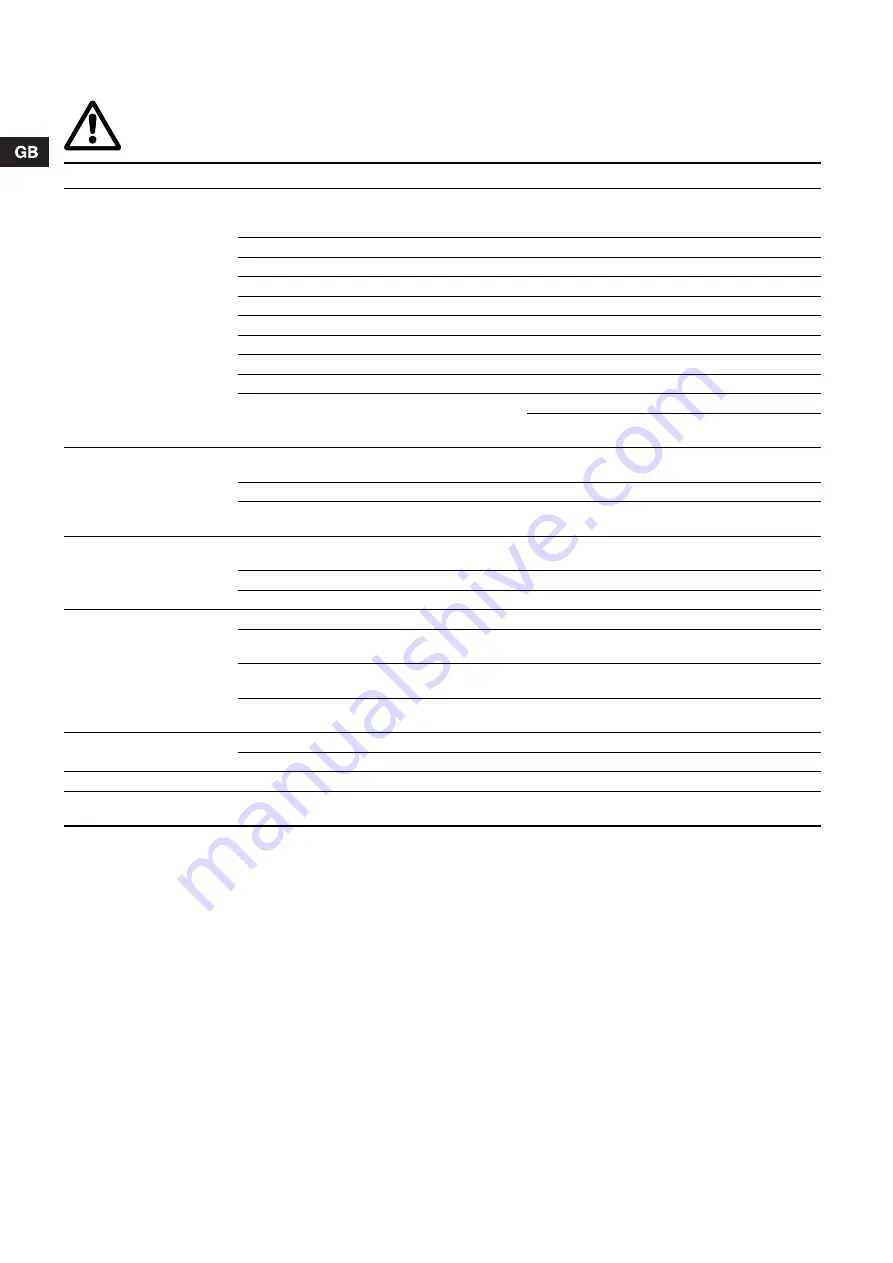
12
14. Fault finding chart
For faults not listed in this fault finding chart, please refer to the installation and operating instructions for the pumps.
15. Related documentation
For further information about Hydro Multi-S, see WebCAPS on
Grundfos’ homepage, www.grundfos.com.
16. Disposal
This product or parts of it must be disposed of in an
environmentally sound way:
1. Use the public or private waste collection service.
2. If this is not possible, contact the nearest Grundfos company
or service workshop.
Warning
Before making any work on the booster set, make sure that the electricity supply has been switched off and that it
cannot be accidentally switched on.
Fault
Cause
Remedy
1. The Hydro Multi-S does
not run when started.
a) The actual pressure is higher than or equal to
the cut-in pressure set.
Wait until the pressure has dropped, or lower the
pressure on the discharge side of the Hydro Multi-
S. Check that the booster set starts.
b) Electricity supply disconnected.
Connect the electricity supply.
c) Automatic circuit breakers cut out.
Correct the fault, and cut in the circuit breakers.
d) Motor protection activated.
Contact Grundfos.
e) Circuit breaker defective.
Replace the circuit breaker.
f)
Pressure switch defective.
Replace the pressure switch.
g) Fuse defective.
Correct the fault, and replace the fuse.
h) Pump blocked.
Remove the cause of the blocking.
i)
Motor defective.
Repair or replace the motor.
j)
Electronic circuit-board failure.
Replace the fuse, if defective.
Switch to emergency operation, and replace the
electronic circuit board, if defective.
2. Pump starts, but stops
immediately afterwards.
a) Incorrect setting of pressure switch.
Increase the cut-out pressure and/or differential
pressure.
b) Wrong diaphragm tank pre-charge pressure.
Check the pre-charge pressure.
c) Dry-running protection activated.
Check the inlet conditions, and make sure that
liquid flows freely to the pumps.
3. Frequent starts and stops. a) Incorrect setting of pressure switch.
Increase the cut-out pressure and/or differential
pressure.
b) Wrong diaphragm tank pre-charge pressure.
Check the pre-charge pressure.
c) Diaphragm tank defective.
Repair or replace the diaphragm tank.
4. Pumps are running, but
deliver no water.
a) Suction pipe/pumps blocked by impurities.
Clean the suction pipe/pumps.
b) Foot or non-return valve blocked in closed
position.
Check and repair the valve.
c) Air in suction pipe/pumps.
Vent the pumps. Check the suction pipe for
leakages.
d) Motors running with wrong direction of rotation. Change the direction of rotation (interchange two
phases of the electricity supply).
5. Pumps run backwards
when switched off.
a) Leakage in suction pipe.
Repair or replace the suction pipe.
b) Foot or non-return valve is defective.
Repair or replace the valve.
6. Shaft seal leakage.
a) Shaft seal defective.
Replace the shaft seal.
7. Noise.
a) The pumps are cavitating.
Check the suction conditions (pump, pipe, valves
and the suction strainer, if any).
Subject to alterations.