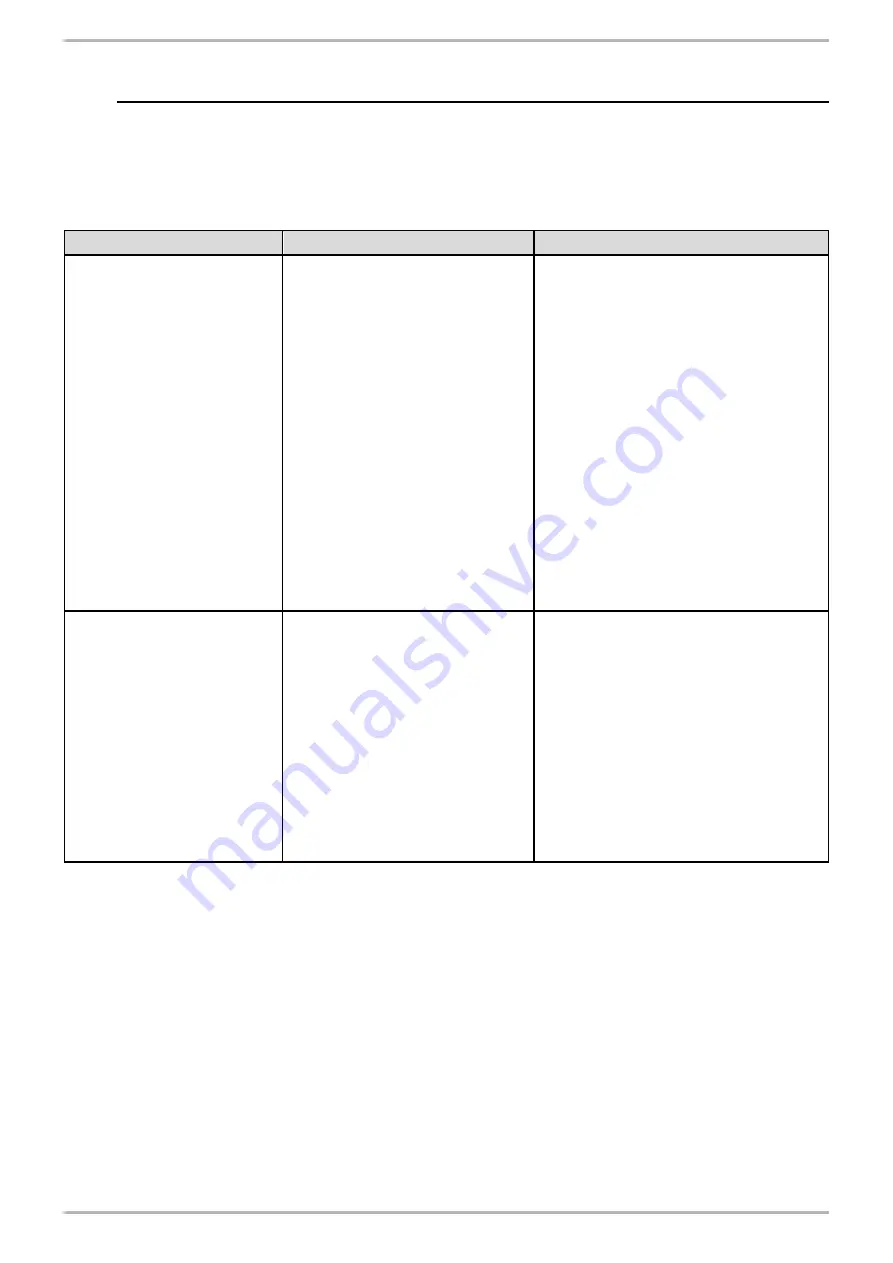
MELBURY HE 3800-10000 -
Installation, Use and Maintenance
Page 32 / 36
410821-V11
6.3. First steps to take in case of failure
In the event of system operational failure, perform the
checks in the table below. Also check the governor set-
up. If the failure cannot be eliminated, call a reliable
engineer or your support service.
Problem
Possible cause
Solution
Burner not functioning
No power.
Check fuse, switch on main or safety
switch. Connect supply and burner plug.
Burner LED is on.
Press burner reset button.
No oil.
Add oil.
Gas pressure insufficient.
Call the gas board.
Overheat temperature LED is on.
Safety thermostat has come into
operation.
Fix the cause, wait until temperature has
dropped below overheat setpoint then
reset the safety thermostat by pushing the
pin.
External default LED is on.
Fix the cause.
No heat release to consumers Incorrect operation type setting on
governor.
Circulation pump blocked.
Water level or system pressure.
Shut-off elements on supply and
return lines closed.
Set up type of operation and heating
program.
Remove locking screw, turn shaft until no
more resistance is left.
Top up and ventilate.
Open them.