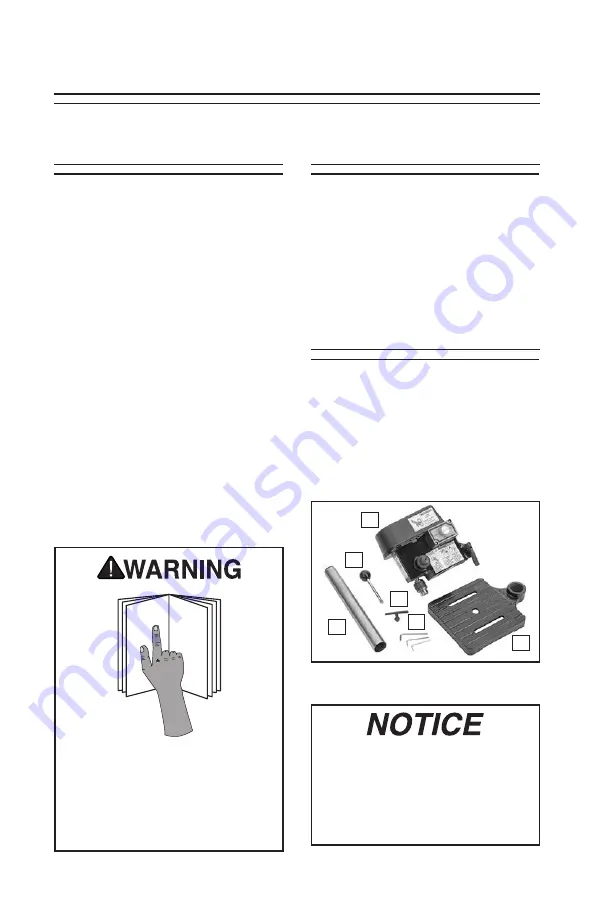
Model T32006 (Mfd. Since 01/20)
-12
-
Inventory
Your tool was carefully packaged for
safe transportation. Remove the packag-
ing materials from around your tool and
inspect it. If you discover the tool is dam-
aged, please immediately call Customer
Service at (570) 546-9663 for advice.
Save the containers and all packing mate-
rials for possible inspection by the car-
rier or its agent. Otherwise, filing a freight
claim can be difficult.
When you are completely satisfied with
the condition of your shipment, inventory
the contents.
If any non-proprietary parts are missing
(e.g., a nut or a washer), we will gladly
replace them; or for the sake of expedi-
ency, replacements can be obtained at
your local hardware store.
Unpacking
This
tool
presents serious injury
hazards to untrained users. Read
through this entire manual to
become familiar with the controls
and operations before starting the
tool!
Needed for Setup
The following items are needed, but not
included, for setup/assembly of this tool.
Safety Glasses ................................... 1 Pr.
Description
Qty.
Inventory (Figure 4)
A. Headstock Assembly .........................1
B. Column ...............................................1
C. Downfeed Handle ..............................1
D. Chuck Key ..........................................1
E. Hex Wrenches 2, 2.5, 4mm ........ 1 Ea.
F. Table ..................................................1
If you cannot find an item on this
list, carefully check around/inside
the tool and packaging materials.
Often, these items get lost in pack-
aging materials while unpacking or
they are pre-installed at the factory.
SECTION 4: SETUP
B
Figure 4. Inventory.
A
F
E
D
C
B
Содержание T32006
Страница 32: ......