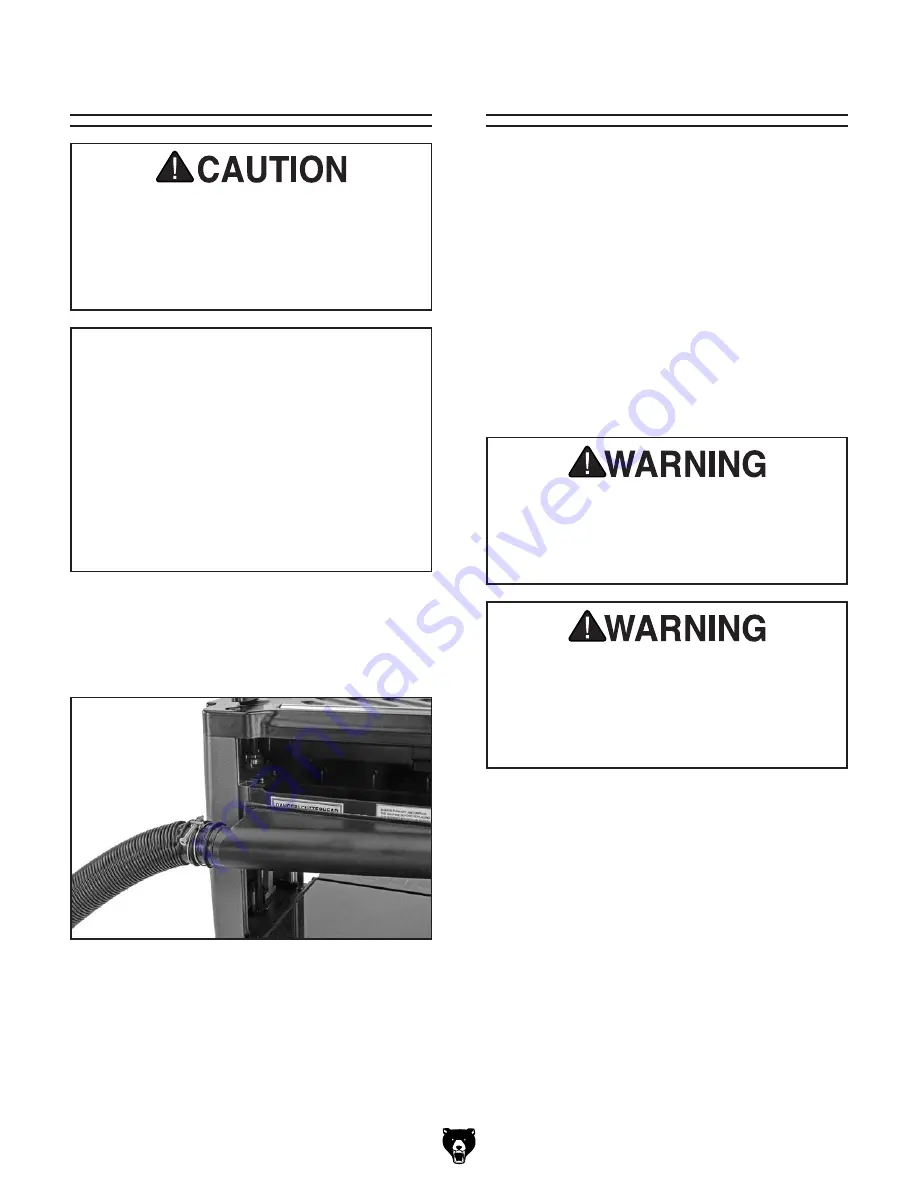
Model G0939/G0940 (Mfd. Since 12/20)
-19-
Dust Collection
To connect a dust collection hose:
1. Fit 2 " dust hose over dust port and secure
with hose clamp (see
Figure 12).
Recommended CFM at Dust Port: 150 CFM
Do not confuse this CFM recommendation with
the rating of the dust collector. To determine the
CFM at the dust port, you must consider these
variables: (1) CFM rating of the dust collector,
(2) hose type and length between the dust col-
lector and the machine, (3) number of branches
or wyes, and (4) amount of other open lines
throughout the system. Explaining how to cal-
culate these variables is beyond the scope of
this manual. Consult an expert or purchase a
good dust collection "how-to" book.
This machine creates a lot of wood chips/
dust during operation. Breathing airborne
dust on a regular basis can result in perma-
nent respiratory illness. Reduce your risk
by wearing a respirator and capturing the
dust with a dust-collection system.
Test Run
Once assembly is complete, test run the machine
to ensure it is properly connected to power and
safety components are functioning correctly.
If you find an unusual problem during the test run,
immediately stop the machine, disconnect it from
power, and fix the problem BEFORE operating the
machine again. The
Troubleshooting table in the
SERVICE section of this manual can help.
DO NOT start machine until all preceding
setup instructions have been performed.
Operating an improperly set up machine
may result in malfunction or unexpect-
ed results that can lead to serious injury,
death, or machine/property damage.
Serious injury or death can result from
using this machine BEFORE understanding
its controls and related safety information.
DO NOT operate, or allow others to operate,
machine until the information is understood.
The test run consists of verifying the following:
1) The motor powers up and runs correctly, and
2) the safety disabling mechanism on the switch
works correctly.
Figure 12. Dust hose installed onto dust port.
2. Tug hose to make sure it does not come off.
Note: A tight fit is necessary for proper
performance.