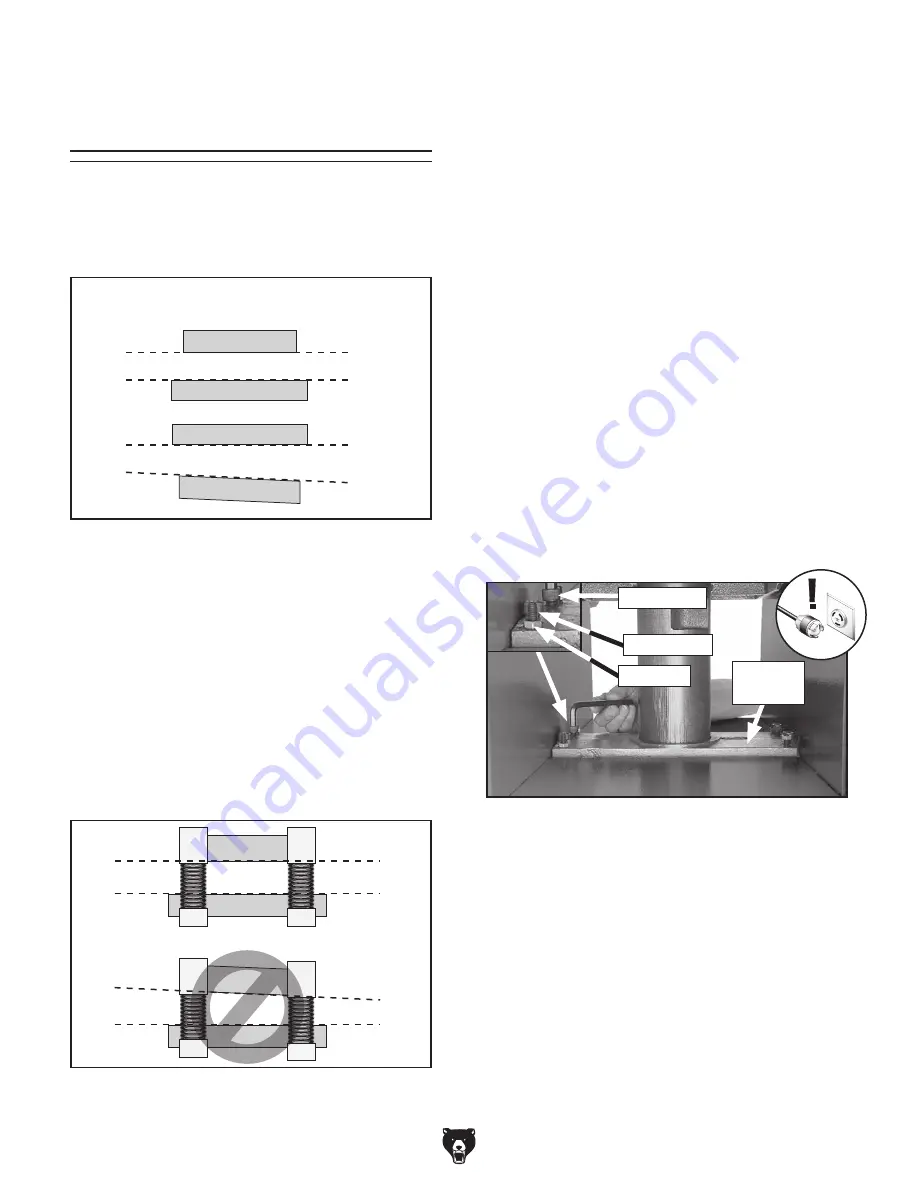
-48-
Model G0634X (Mfd. Since 11/20)
Checking Planer
Table Parallelism
Table Parallelism Inspection
The easiest way to check that your planer table is
parallel with the headstock is to plane a workpiece
and then measure its thickness in multiple loca-
tions. Extra care must be taken to ensure accu-
racy. If the workpiece is tapered from left-to-right
or from front-to-back, then parallelism may be a
problem. If the table is not within the maximum
allowable tolerances, it must be adjusted.
Table Parallelism Adjustments
Items Needed:
Qty
Rotacator ........................................................... 1
Wrench 12mm ................................................... 1
Hex Wrench 4, 8mm ....................................1 Ea.
To adjust table parallelism:
1.
DISCONNECT MACHINE FROM POWER!
2.
Raise planer table as far as possible.
3.
Loosen (4) cap screws on cylinder liner, as
shown in Figure 69.
Table parallelism is critical to the operation of the
planer. As such, it is essential that the planer table
is parallel with the cutterhead (within 0.002") from
side-to-side, as illustrated in Figure 67.
Figure 67.
Side-to-side parallelism of table and
cutterhead.
Cutterhead
Table
Parallel
Parallel
SIDE-TO-SIDE
Table
NOT Parallel
NOT Parallel
(Front View)
Cutterhead
Figure 68.
Front-to-back parallelism.
Table
Table
Head
Head
Parallel
Parallel
Not-Parallel
Not-Parallel
FRONT
BACK
How the planer table sits in relation to the head
casting from front-to-back is also important (see
Figure 68
). The tolerances on the front-to-back
positioning are not as critical as the cutterhead/
table side-to-side positioning. Therefore, the max-
imum allowable tolerance for the front-to-back
parallelism is not more than 0.020".
— If table is not parallel to cutterhead side-to-
side (see Figure 69), loosen (2) lock nuts
on right or left side of cylinder liner. Adjust
set screws to raise or lower table so it is
parallel to cutterhead.
— If table is not parallel to cutterhead front-
to-back (see Figure 69), loosen (2) lock
nuts at front or back of cylinder liner.
Adjust set screws to raise or lower front or
back of table so it is parallel to cutterhead.
4.
Tighten (4) cap screws on cylinder liner.
Figure 69
. Adjusting table parallelism.
Lock Nut
Set Screw
Cap Screw
Cylinder
Liner
Maximum Allowable Tolerances:
Cutterhead/Table Side-to-Side ..................0.002"
Head Casting/Table Front/Back ................0.020"
Содержание G0634X
Страница 68: ......