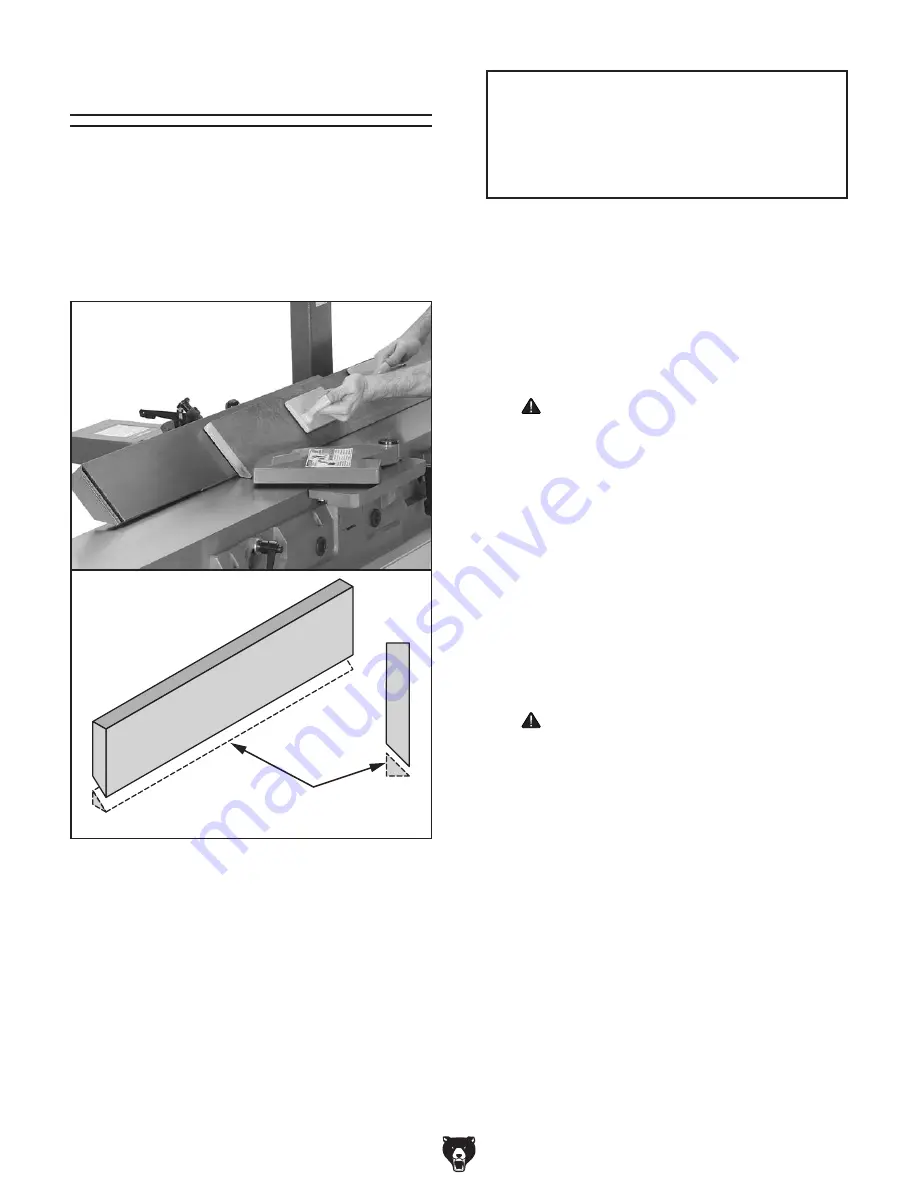
-28-
Model G0495X (Mfd. Since 07/19)
Bevel Cutting
Figure 23. Example photo of fence set up for a
bevel cut of 45°.
Removed
Surface
To bevel cut on jointer:
1. Inspect stock to ensure it is safe and suitable
for the operation
(see Stock Inspection &
Requirements section).
2. Set infeed table height to cutting depth
desired for each pass.
CAUTION: Cutting depth for bevel cuts is
typically between
1
⁄
16
" and
1
⁄
8
", depending on
hardness and width of stock.
3. Set fence tilt to desired angle of cut.
4. Place workpiece against fence and infeed
table with concave side face down.
5. Start jointer.
6. With a push block in your leading hand, press
workpiece against table and fence with firm
pressure, and feed workpiece over cutter-
head with a push block in your trailing hand.
CAUTION: When your leading hand gets
within 4" of the cutterhead, lift it up and over
cutterhead, and place push block on portion
of the workpiece once it is 4" past cutterhead.
Now, focus your pressure on outfeed end
of the workpiece while feeding, and repeat
same action with your trailing hand when it
gets within 4" of cutterhead. To help keep
your hands safe, DO NOT let them get closer
than 4" from moving cutterhead at any time
during operation!
7. Repeat cutting process, as necessary, until
you are satisfied with the results.
NOTICE
If you are not experienced with a jointer,
set depth of cut to 0", and practice feeding
workpiece across tables as described. This
will help you prepare for actual operations.
Bevel cuts (see example
Figures below) can be
made by setting the fence at the desired angle
and feeding the workpiece firmly along the fence
face, with the bottom inside corner firmly against
the table. The cutting process typically requires
multiple passes or cuts to bevel the entire edge
of a workpiece.