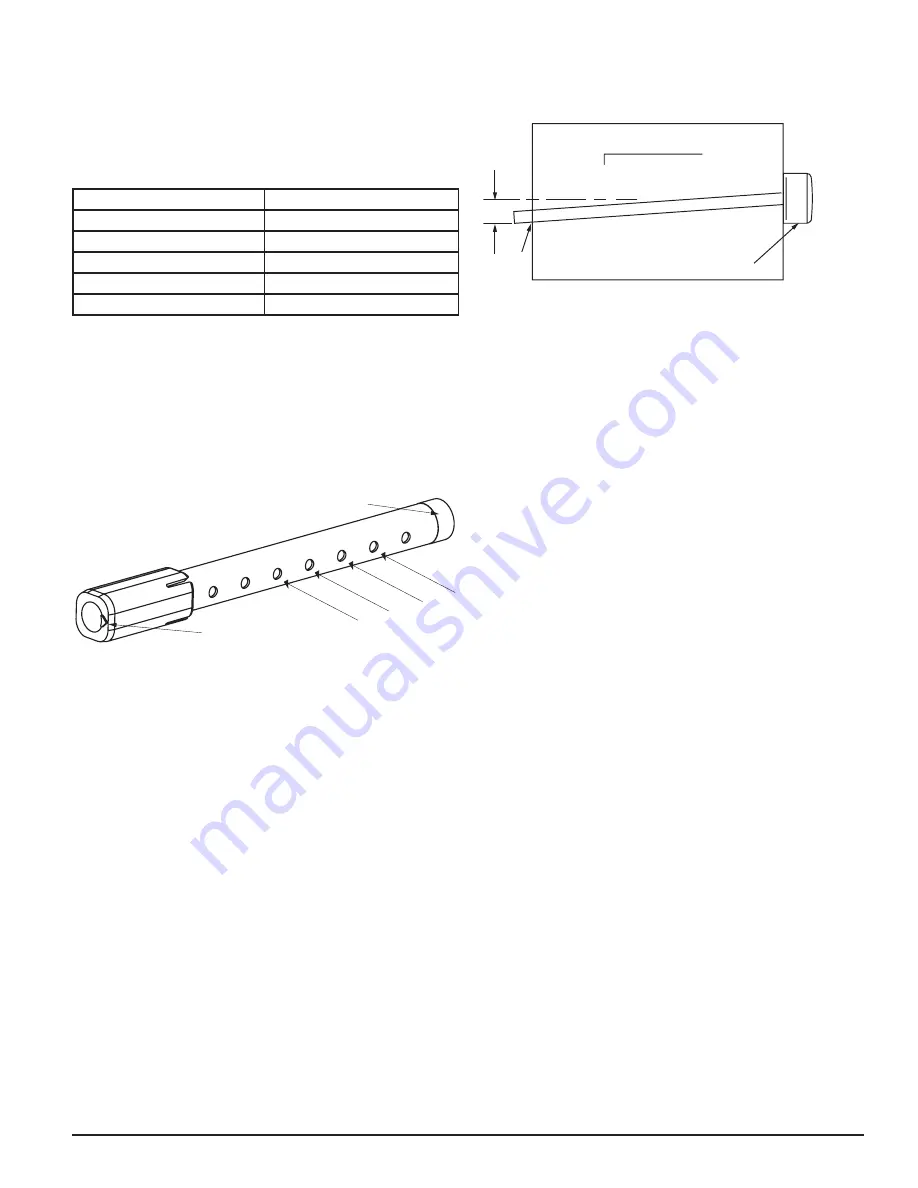
[6] SAMPLING TUBE INSTALLATION
[6.1] SAMPLING TUBE SELECTION
The sampling tube must be purchased separately. Order the correct length, as
specified in
Table 1
, for width of the duct where it will be installed. It is recom-
mended that the sampling tube length extend at least
2
/
3
across the duct width
for optimal performance.
TABLE 1. SAMPLING TUBES RECOMMENDED FOR DIFFERENT
DUCT WIDTHS:
Outside Duct Width
Sampling Tube Recommended*
Up to 1 ft.
DST1
1 to 2 ft.
DST1.5
2 to 4 ft.
DST3
4 to 8 ft.
DST5
8 to 12 ft.
DST10 (2-piece)
*Must extend a minimum of
2
/
3
the duct width.
The sampling tube is always installed with the air inlet holes facing into the
air flow. To assist proper installation, the tube’s connector is marked with an
arrow. Make sure the sampling tube is mounted so that the arrow points into
the airflow as shown in
Figure 3
. Mounting the detector housing in a vertical
orientation is acceptable provided that the air flows directly into the sampling
tube holes as indicated in
Figure 3
. The sampling tube and exhaust tube can be
mounted in either housing connection as long as the exhaust tube is mounted
downstream from the sampling tube.
FIGURE 3. AIR DUCT DETECTOR SAMPLING TUBE:
SAMPLING TUBE ENDCAP
ARROW MUST FACE
INTO AIR FLOW
AIR FLOW
DIRECTION
H0551-00
CAUTION:
The sampling tube end cap, included with the detector, is critical to
proper operation of the duct smoke detector. The end cap is needed to create
the proper air flow to the sensor of the duct smoke detector. Once any sampling
tube length adjustments are made, plug the end of the sampling tube with the
provided end cap.
A plastic exhaust tube is included with the unit to be installed if needed. Install
into the housing connection that is downstream from the sampling tube connec-
tion. The exhaust tube can be installed from the front or back of the detector.
A longer 1 foot exhaust tube, model ETX, is available as an accessory in cases
where the molded exhaust tube does not extend at least 2 inches into the duct.
[6.2] SAMPLING TUBE INSTALLATION
1. For tubes shorter than the width of the duct, slide the sampling tube,
with installed end cap, into the housing connection that meets the airflow
first. Position the tube so the arrow points into the airflow as shown in
Figure 3
. Per NFPA sampling tubes over 3 feet long should be supported at
the end opposite the duct detector. In ducts wider than 8 feet, work must
be performed inside the duct to couple the other section of the sampling
tube to the section already installed using the
1
/
2
inch conduit fitting. Make
sure that the holes on both sections of the air inlet sampling tube are lined
up and facing into the airflow.
2. For tubes longer than the width of the duct, the tube should extend out
of the opposite side of the duct. Drill a
3
/
4
inch hole in the duct opposite
the hole already cut for the sampling tube. Ensure that the sampling tube
is angled downward from the duct smoke detector to allow for moisture
drainage away from the detector. The sampling tube should be angled
at least 1/4” downward for every 12” of duct width per
Figure 4
. There
should be 10 to 12 holes spaced as evenly as possible across the width of
the duct. If there are more than 2 holes in the section of the tube extending
out of the duct, select a shorter tube using
Table 1
. Otherwise, trim the
tube to leave approximately 1 to 2 inches extending outside the duct. Plug
the end with the end cap and tape closed any holes in the protruding sec-
tion of tube. Be sure to seal the duct where the tube protrudes.
FIGURE 4.
DETECTOR
3
/
4
˝
HOLE
12˝
1
/
4
˝
2˝
H0215-00
NOTE:
Air currents inside the duct may cause excessive vibration, especially
when the longer sampling tubes are used. In these cases, a 3 inch floor flange
(available at most plumbing supply stores) may be used to fasten the sampling
tube to the other side of the duct. When using the flange/connector mounting
technique, drill a 1 to 1
1
/
4
inch hole where the flange will be used.
[6.3] MODIFICATIONS OF SAMPLING TUBES
There may be applications where duct widths are not what is specified for the
installation. In such cases, it is permissible to modify a sampling tube that is
longer than necessary to span the duct width.
Use a 0.193 inch diameter (#10) drill and add the appropriate number of holes
so that the total number of holes exposed to the air flow in the duct is 10 to 12.
Space the additional holes as evenly as possible over the length of the tube.
NOTE:
This procedure should only be used as a temporary fix and is not in-
tended as a substitute for ordering the correct length tubes.
[6.4] REMOTE SAMPLING TUBE INSTALLATION
The detector arrangement can also incorporate remote mounting of the sam-
pling tube and/or exhaust tube. In this case both the detector, sampling tube
and exhaust tube (if included) should be rigidly mounted to withstand the pres-
sure and vibrations caused by the air velocity. The location of the detector’s
sampling tube should be such that there is uniform airflow in the cross section
area.
The pressure differential across the sampling and exhaust ports in the detector
housing shall be verified to be between 0.01 and 1.11 inches of water. Do so
by measuring the pressure difference between the inlet and outlet ports on the
detector housing using a manometer as described in
Section 7.1
.
[7] MEASUREMENT TESTS
[7.1] AIR FLOW
The DSD120 is designed to operate over an extended air speed range of 100
to 4000 FPM. To verify sufficient sampling of ducted air, turn the air handler
on and use a manometer to measure the differential pressure between the two
sampling tubes. The differential pressure should measure at least 0.01 inches of
water and no more than 1.11 inches of water. Because most commercially avail-
able manometers cannot accurately measure very low pressure differentials, ap-
plications with less than 500 FPM of air speed may require one of the following:
1) the use of a current-sourcing pressure transmitter (Dwyer Series 607) per
Section 7.2, or 2) the use of aerosol smoke per section 11.4.2.
[7.2] LOW FLOW AIR FLOW TEST USING DWYER SERIES 607
DIFFERENTIAL PRESSURE TRANSMITTER
Verify the air speed of the duct using an anemometer. Air speed must be at least
100 FPM. Wire the Dwyer transmitter as shown in
Figure 5
. Connect the leads
of the meter to either side of the 1000
Ω
resistor. Allow unit to warm up for 15
seconds. With both HIGH and LOW pressure ports open to ambient air, measure
and record the voltage drop across the 1000
Ω
resistor (measurement 1), 4.00
volts is typical. Using flexible tubing and rubber stoppers, connect the HIGH
side of the transmitter to the sampling tube of the duct smoke detector hous-
ing, and the LOW side of the transmitter to the exhaust tube of the duct smoke
detector housing. Measure and record the voltage drop across the 1000
Ω
resistor
(measurement 2). Subtract the voltage recorded in measurement 1 from the
voltage recorded in measurement 2. If the difference is greater than 0.15 volts,
there is enough air flow through the duct smoke detector for proper operation.
IN-GE-DSD120-01-01 3
I56-9201-000
5/6/2019