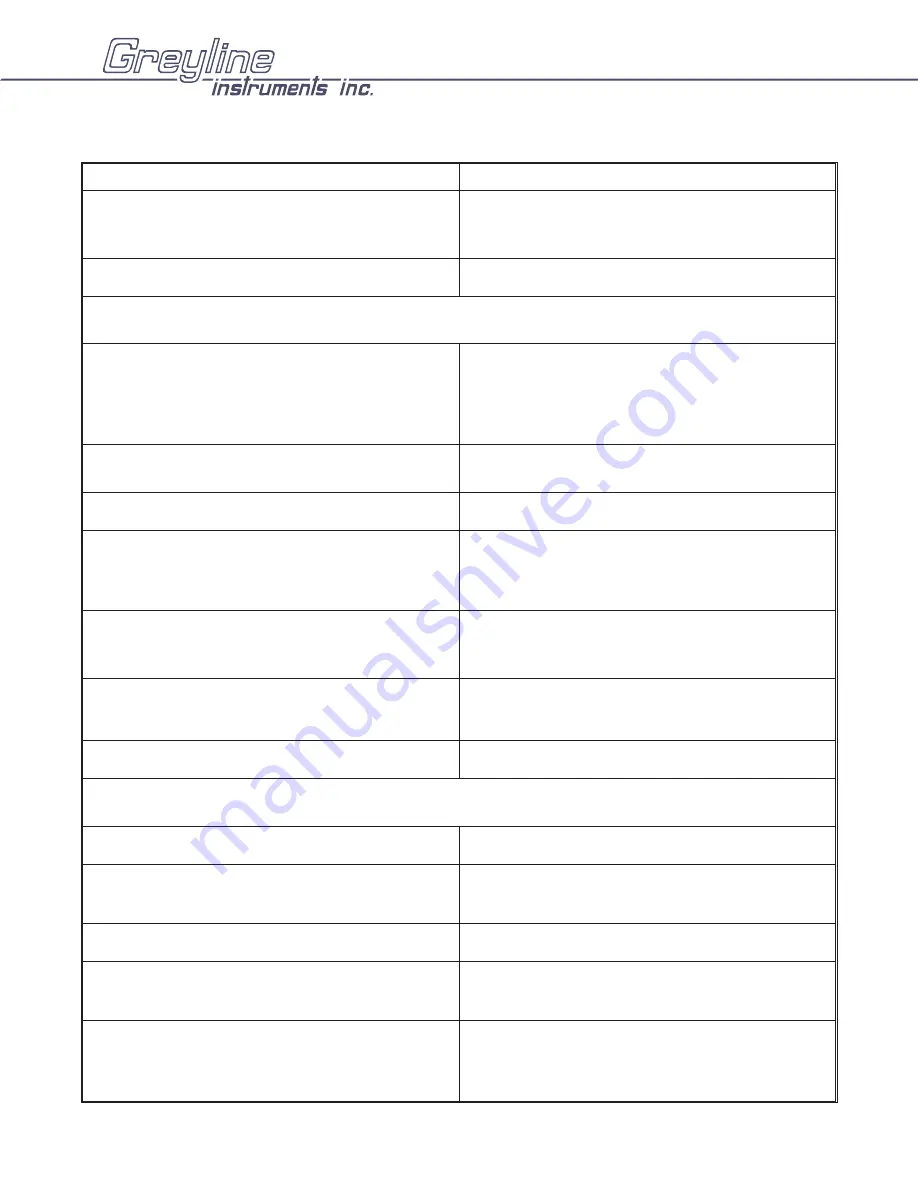
Possible Causes:
Corrective Action:
Valve leak or Reverse flow
·
Test Valve. Relocate Sensor farther from valve
·
Use Backflow Rejection
Sensor connections incorrect
·
Refer to Connections diagram
METER READING ERRATIC
Sensor mounted too close to valve, pump or
elbow
·
Change sensor placement. Recommended 6-10
diameters from elbows, and 30 diameters from
pumps, controlling valves, orifice plates,
nozzles or open pipe discharge
NO FLOW INDICATION
SS
Signal Strength/Sensitivity set too low
·
Increase
SS
/Sensitivity
Not enough suspended particles or gases in the
fluid
·
Relocate sensor in more turbulent pipe section.
Mount sensor at 12 o'clock position on
horizontal pipe
Coupling compound washed out, or sensor loose
on pipe
·
Remount sensor
·
Use Dow Corning Silicone #4
Slave
selected in
SPECIAL FUNCTIONS
menu with no Synchronization input from
Master.
·
Select
Master
in
SPECIAL FUNCTIONS
menu.
Power interruption. No flow.
·
Check fuse/breaker. Confirm flow
METER READING TOO HIGH
Calibration error
·
Review UNITS/MODE menu and Pipe ID
Vibration or noise on the pipeline
·
Decrease Sensitivity. Install in another
location.
Pipe is not full
·
Remount Sensor on vertical pipe
Nearby velocity increasing device (pump, valve,
orifice plate)
·
Relocate sensor >30 pipe diameters from
velocity increasing device
Local electrical noise
·
Ensure all Flowmeter wiring is in METAL
conduit and sensor cable shield is connected to
Ground stud
DFM-IV Doppler Flow Meter
Manual Series A.6
Page 20