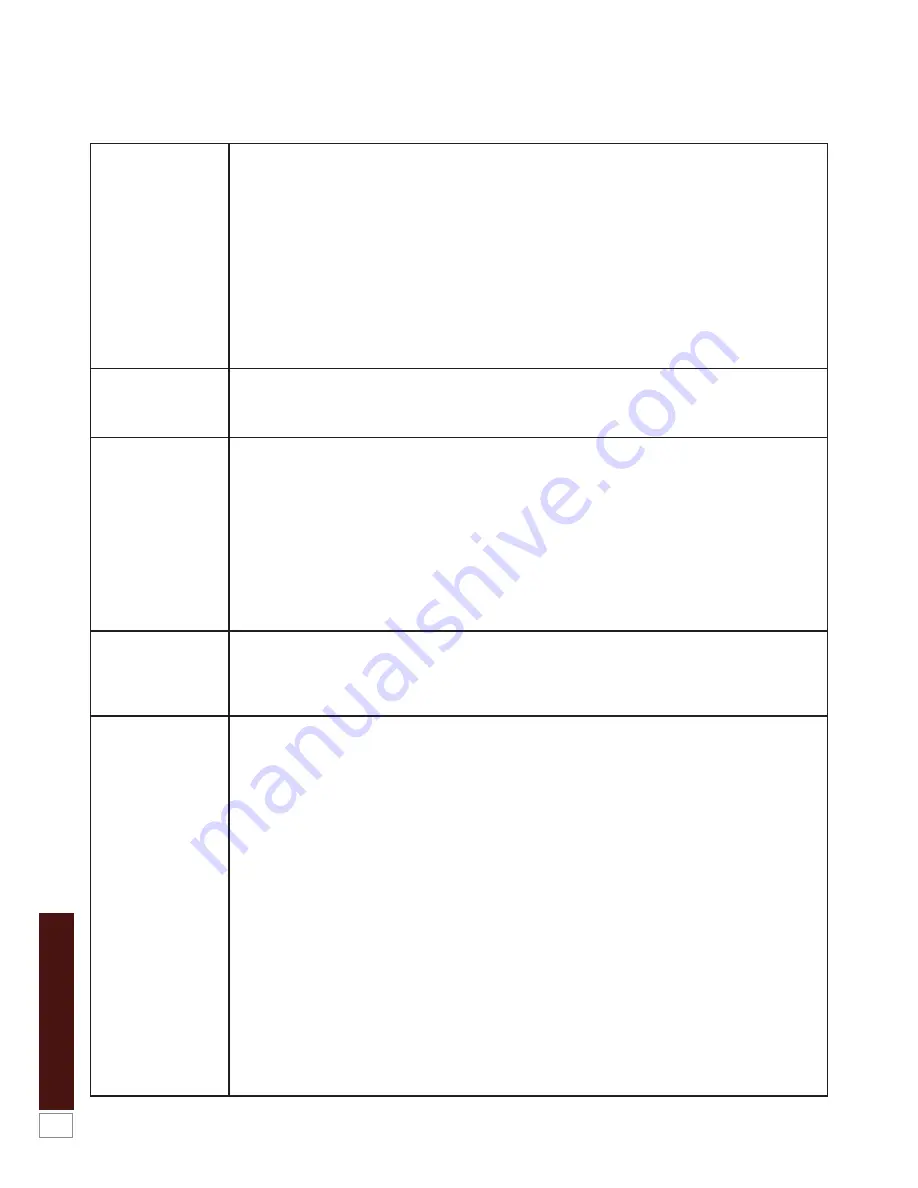
10
9 If your Boiler Fails to Light
If you experience a problem with your boiler, it may be due to something quite simple and by making a few checks you can quickly rectify it for
yourself. If your boiler fails to light, please follow the procedure given below, starting with STEP 1:
STEP 1
Is the burner control panel display blank?
NO - go to STEP 2
YES – Check the following:
•
Is the electrical supply to boiler and heating system controls switched on at fused spur?
•
Has the fuse in the fused spur blown?
•
Are all the plugs at the rear of the hopper, the rear of the boiler and the side of the burner fitted correctly?
•
Is the combustion chamber door closed and the catch fully engaged?
•
Has the boiler overheat thermostat tripped? Remove cap to check. If yes, press the reset button. Refer to
Section 4. If this does not rectify the problem, contact your Installer.
•
Has the pellet feed tube thermostat tripped? Reset the thermostat. Refer to Section 6 – Pellet Feed Tube
Thermostat for details. If this does not rectify the problem, contact your Installer.
If, after checking the above, there is still a problem then contact your Installer for assistance.
STEP 2
Is one of the four ERROR MESSAGES scrolling across the bottom of the burner control panel display?
YES – go to STEP 4
NO – go to STEP 3
STEP 3
Is there a cursor next to the ‘Heating Demand’ symbol on the burner display?
YES – Check the temperatures on the burner display.
•
Is the H2O value on the display higher than the set point temperature value plus 5°C. If so, there is NO fault
but the boiler is waiting for the system temperature to drop before firing again.
NO – Check the following:
•
Is the burner STANDBY/ON switch set to the ON position? If not, then set it to ON.
•
Is there a sufficient quantity of pellets in the pellet hopper? If not, top up the hopper with pellets.
•
Are the heating system controls (programmer, room thermostat, etc.) ‘calling’ for heat? If not, set controls to
call for heat.
If, after checking the above, there is still a problem then contact your Installer for assistance.
STEP 4
Which one of the four ERROR MESSAGES is scrolling across the bottom of the burner control panel display?
•
FAILED PELLET LIGHTING – go to STEP 5
•
SERVO MOTOR BLOCKED – go to STEP 6
•
PROBE FAULT – go to STEP 7
•
AIR PRESSURE ERROR – go to STEP 8
STEP 5
FAILED PELLET LIGHTING is scrolling across the bottom of the burner control panel display.
Check the following:
•
Is there a sufficient quantity of pellets in the pellet hopper? If not, top up the hopper.
•
Is the pellet auger fully primed? If not, prime the auger. Refer to Section 7.
•
If there is a bulk pellet store, Are there pellets in the bulk store? Refer to Section 2 – Bulk pellet stores.
•
Is the bulk store auger (if fitted) fully primed? Refer to Section 2 – Bulk pellet stores.
•
If a Grant SpiraVAC vacuum system is fitted, is it delivering pellets to the pellet hopper? Refer to Instructions
supplied with the SpiraVAC system.
•
Are pellets being delivered to the burner by the pellet hopper auger? If not, check the following:
a) Is the auger rotating? If not, check if the auger power supply lead is correctly plugged in to the burner.
If it is still not rotating then contact your Installer.
b) Is there a build-up of dust in the bottom of the hopper? If so, this dust MUST be removed from the hopper
and auger, and the auger then must be re-primed. Refer to Section 7.
NOTE
Pellets that contain an excessive amount of dust will prevent the auger from pulling the pellets out of the hopper.
The hopper will need to be cleaned of any dust.
•
With the burner STANDBY/ON switch set to the STANDBY position, remove the pellet feed tube from the
burner and open the combustion chamber door.
•
Is the brazier blocked with ash/clinker? If yes, is the correct grade of pellets being used? If not, empty the
hopper and refill with correct grade of pellet.
If, after checking the above, there is still a problem then contact your Installer for assistance.