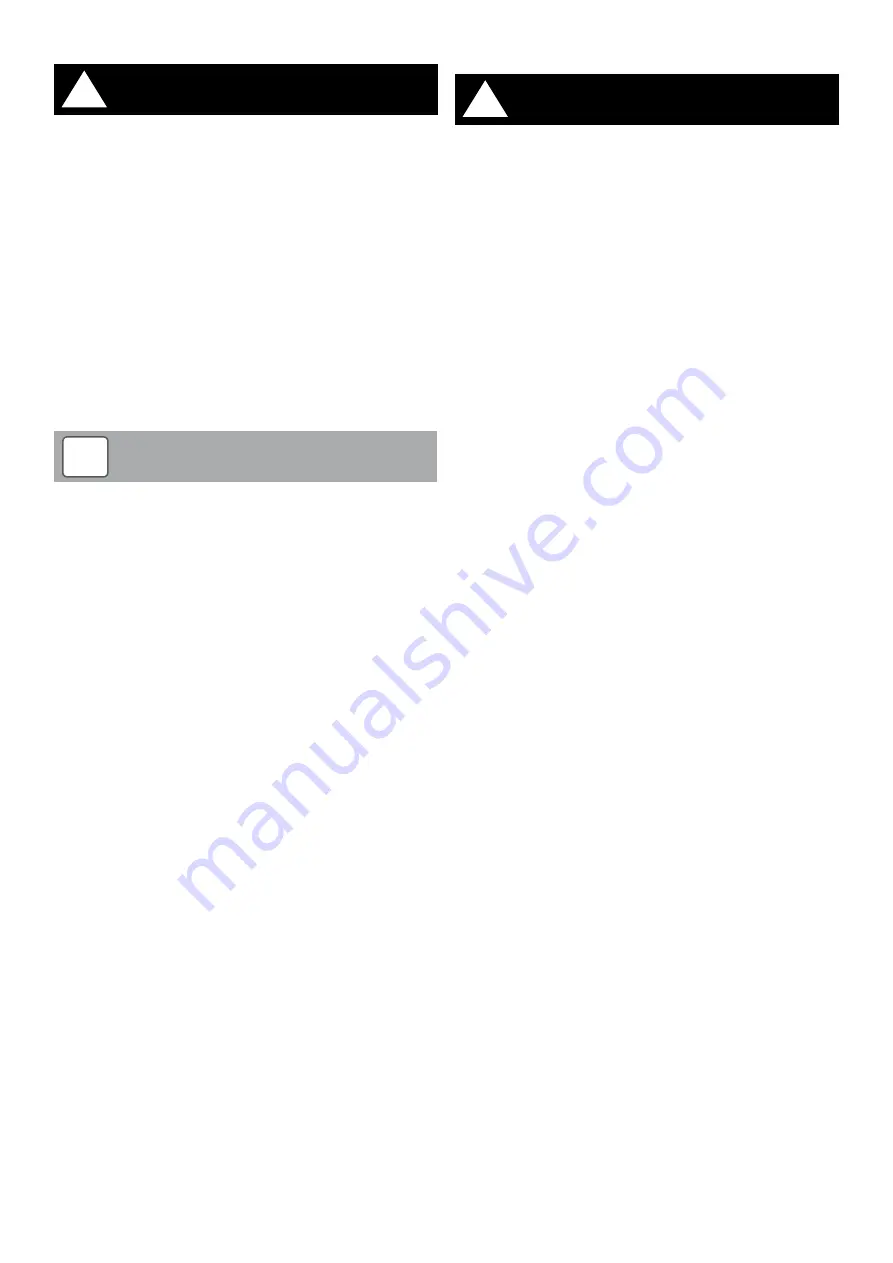
Section 7: Flue System and air Supply
Page 23
all joints in the flue system must be accessible for inspection.
no joints should be located within a wall, floor or ceiling spaces
or any other inaccessible place.
!
WaRninG
7.4.3 adjustable Length
The Grant ‘Biomass’ flue system includes an Adjustable flue
extension. Refer to Section 7.9. This allows any of the straight flue
extension components to be extended in length by between 00mm to
230mm (this does not apply to the 200mm extension). This adjustable
extension must be used in conjunction with any straight extension
(1000mm, 500mm, 333mm or 200mm) to achieve the actual straight
length required.
To fit the adjustable extension, first remove insulation from between
the inner and outer walls of the component, as necessary. Fit the
open end over the ‘male collar’ end of the fixed extension and adjust
to achieve the required overall length. Secure the two components
together using the wide locking band supplied.
the adjustable section is nOt loadbearing, therefore adequate
support of the flue system MUSt be provided immediately
above the adjustable extension.
nOtE
!
7.4.4 Support Components
The weight of the flue system is considerable. It must NOT be carried
by the flue connection on the appliance, but requires independent
support using one or more of the various flue support options
available in the Grant ‘Biomass’ flue system.
intermediate top Plate (product code: WPB/tP)
Flue systems running up against an external wall surface can be
supported using the Intermediate Top Plate. This is mounted on either
a pair of Wall Support Side Plates (product code: WPB/WS or WPB/
WS) or a pair of Cantilever brackets (product code: WPB/CANT),
which are fastened to the wall, to provide support at either the base,
or part way up a vertical section of flue.
The ‘female collar’ (on the underside of the plate) is fitted into the flue
below and the ‘male collar’ (on the upper side of the plate) is a twist-
lock connection into the flue above. Both joints are secured using the
clamp bands provided.
Wall Brackets (product codes: WPB/WB60 and WPB/WB300)
Both the Wall bracket and the Adjustable Wall Bracket (Grant Ref.
WPB/WB60 and WPB/WB300) are NOT load-bearing but are designed
to give lateral support only. Wall brackets should be fitted with a
maximum spacing of 3m on straight runs of flue and at any offset to
ensure the system is rigidly supported.
Structural Locking Band (product code: WPB/LBEXt)
A height of up to 3m above the last support at the roof can be
achieved, without the need for guy wires, by using an extended
Structural locking band at the joint immediately below, and at every
joint above, the last flue support.
7.4.5 Flue inspection Pipe (product code: WPBOM/iP)
Failure to maintain a clean flue can result in the emission of
flue gases into the dwelling or damage from fire in the flue.
Refer to Section 11.4.
!
WaRninG
The Building Regulations Approved Document J requires a flue
system to have the means to be inspected and cleaned as required.
To meet this requirement, a Flue Inspection Pipe incorporating an
inspection hatch and combustion test point is available as part of the
Grant ‘Biomass’ flue system. This must be fitted directly to the boiler
flue connector with the inspection hatch facing to the LEFT.
7.4.6 Elbows
Two elbows are available - 30° (product code: WPB/30) and 45°
(product code: WPB/45). To allow for alignment, the female collars of
these elbows do NOT have the twist lock flutes, but the locking band
MUST still be used to secure the two flue components together.
There should be no more than 2 elbows – of maximum angle 45°
from the vertical – fitted between the inspection hatch of the flue
Inspection pipe (at the boiler) and the terminal. This can be increased
to a maximum of four elbows (maximum 45°) between the boiler and
terminal if there is a second flue Inspection Pipe fitted between the
second and third elbows. Any Inspection hatch must be accessible for
checking and cleaning purposes.
Roof Cowl (product code: WPB/RC)
The Rain Cap type terminal is fitted either directly to the Intermediate
Top Plate on the top of the flue or, if necessary (i.e. to achieve the
required distance between the terminal and the roof surface), to a
length of flue that is, in turn, connected to the Intermediate Top Plate.
Fit the Terminal to either the Intermediate Top Plate or flue extension
and twist through 1/6 of a turn to lock in place. Ensure that the
locking band (supplied with the terminal) is correctly fitted to secure
the terminal in place. Refer to Section 7.4.2 for further details on
connecting the flue components.
7.5 Flue testing
Once installed, the flue system should be tested in accordance with
the requirements of The Building Regulations Approved Document J,
Appendix E, Section E13 – Smoke Test I.
7.6 Flue notice Plate
The Building Regulations Approved Document J requires a notice
plate that conveys essential information regarding the flue installed
to be permanently displayed. A suitable self-adhesive notice plate
is supplied with the Grant ‘Biomass’ flue system and this must be
completed by the installer and displayed in an unobtrusive but
obvious position within the building concerned, e.g. on the inside of
the boiler door.