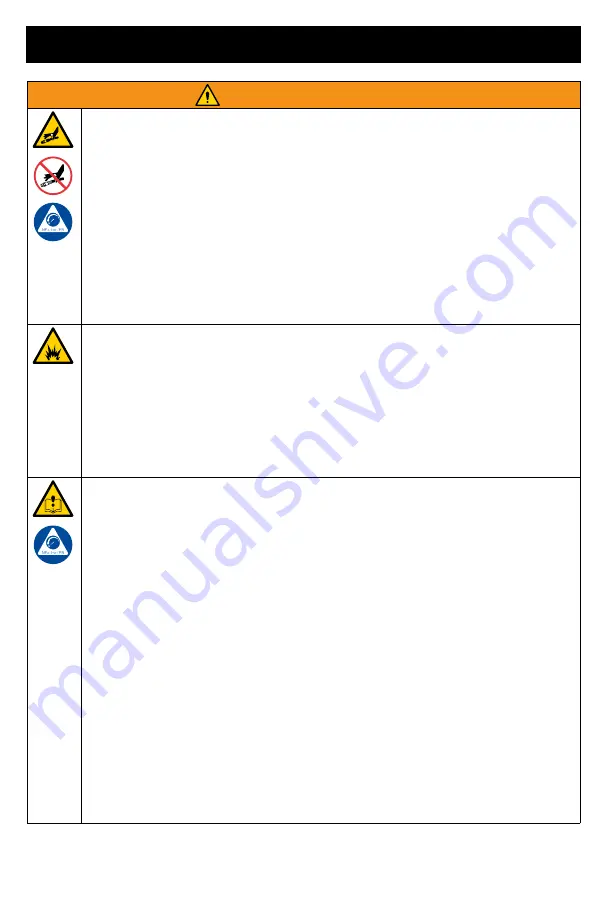
Warnings
3A6884B
5
SKIN INJECTION HAZARD
High-pressure leaks are able to inject oil into the body and cause serious bodily injury that can
result in amputation. In the event that injection occurs,
get immediate surgical treatment.
•
Do not handle pressurized hoses. Escaping oil under pressure can penetrate the skin,
causing serious injury.
•
Do not stop or deflect leaks with your hand, body, glove or rag.
•
Do not leave the unit energized or under pressure while unattended. When the unit is not
in use, turn off the unit and follow the
•
Check hoses and couplings daily. Replace worn or damaged parts immediately.
•
This system is capable of producing 10,000 psi (68.9 MPa, 700 bar). Use Graco replacement
parts or accessories that are rated at a minimum of 10,000 psi (68.9 MPa, 700 bar).
•
Verify that all connections are secure before operating the unit.
•
Know how to stop the unit and bleed pressure quickly. Be thoroughly familiar with the
controls.
FIRE AND EXPLOSION HAZARD
Flammable fumes in work area can ignite or explode. To help prevent fire and explosion:
•
This equipment generates sparks. Do not use in explosive atmospheres or hazardous
(classified) locations.
•
Use only in well-ventilated areas.
•
Do not plug or unplug power cords, or turn power or light switches on or off, when
flammable fumes are present.
•
Keep work area free of debris, including solvent, rags, and gasoline.
•
Keep a working fire extinguisher in the work area.
EQUIPMENT MISUSE HAZARD
Misuse can cause death or serious injury.
•
Do not operate near children. Keep children away from equipment at all times.
•
Do not overreach or stand on an unstable support. Keep effective footing and balance at
all times.
•
Stay alert and watch what you are doing.
•
Do not leave the unit energized or under pressure while unattended. When the unit is not
in use, turn off the unit and follow the
•
Do not operate the unit when fatigued or under the influence of drugs or alcohol.
•
Avoid damaging hydraulic hoses. Avoid sharp bends and kinks when routing hydraulic
hoses. Do not kink or over-bend the hose. Using a bent or kinked hose will cause severe
back-pressure. Sharp bends or kinks will cause internal damage to the hose leading to
premature hose failure.
•
Do not drop heavy objects on hydraulic hoses. A sharp impact may result in internal
damage to the hose. Applying pressure to a damaged hose may cause it to rupture.
•
Do not expose the hose to temperatures or to pressures in excess of those specified by
the hose manufacturer.
•
Do not use the hose as a strength member to pull or lift the equipment.
•
Do not alter or modify equipment. Alterations or modifications may void agency approvals
and create safety hazards.
•
The system operating pressure must not exceed the pressure rating of the lowest rated
piece in the system.
•
Make sure all equipment is rated and approved for the environment in which you are using it.
WARNING