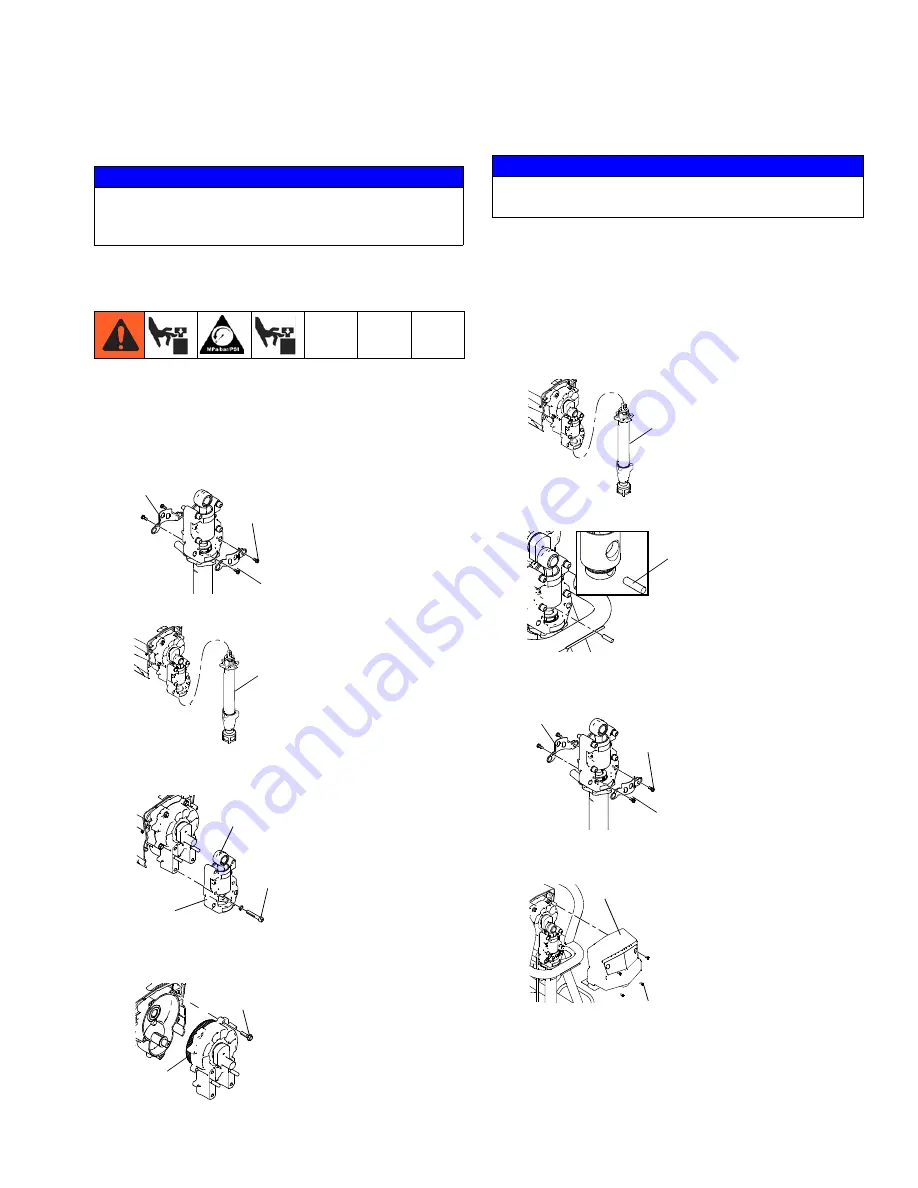
Drive and Bearing Housing
332252A
23
Drive and Bearing Housing
Removal
1.
Perform
Relieve Pressure Procedure
, page 6.
Wait 5 minutes before servicing. Unplug power
cord.
2.
Remove shroud, page 18. Remove screws (31) and
pump rod covers (96).
3.
Remove pump (91).
4.
Remove screws (14), bearing housing (83) and con-
necting rod (85).
5.
Remove screws (7) and separate drive housing (90)
from motor.
Installation
1.
Replace drive housing (90) and tighten screws (7).
Torque to 10.2 - 12.4 N•m (90 - 110 in-lb).
2.
Replace connecting rod (85), bearing housing (83)
and tighten screws (14). Torque to 31.2 - 39.4 N•m
(23 - 29 ft-lb).
3.
Replace pump, page 24.
4.
Lift retaining spring and replace pump pin (44).
5.
Replace pump rod covers (96) and tighten screws
(31). Torque to 4.5 - 5.1 N•m (40 - 45 in-lb).
6.
Replace front shroud (51) and tighten screws (31).
Torque to 4.5 - 5.1 N•m (40 - 45 in-lb).
7.
Replace rear shroud, page 18.
NOTICE
Do not drop gear cluster (89) when removing drive
housing (90). Gear cluster may stay engaged in
motor front end bell or drive housing.
ti13094a
96
31
96
ti13091a
91
ti13089a
83
14
85
ti13090a
7
90
NOTICE
Make sure gear and thrust washers are in place.
Brush grease onto gear teeth.
ti13091a
91
ti13092a
44
ti13094a
96
31
96
ti13079a
51
31