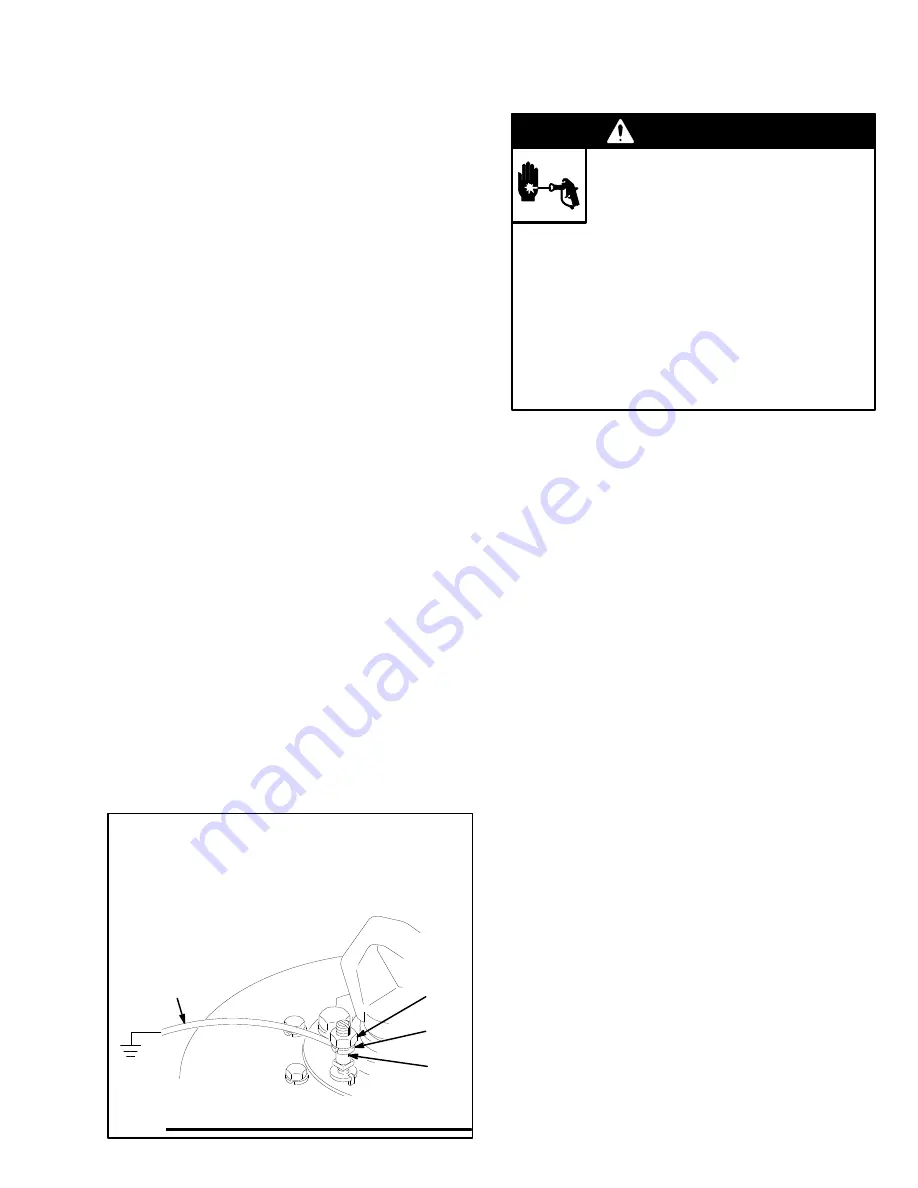
5
307-930
Installation
Grounding
To reduce the risk of static sparking, ground the pump
and all other spray equipment used or located in the
spray area. Check your local electrical code for de-
tailed grounding instructions for your area and type of
equipment. Be sure to ground all of this spray equip-
ment.
1.
Pump: use a ground wire and clamp (Fig 1).
2.
Air hoses: use only electrically conductive air
hoses.
3.
Fluid hoses: use only electrically conductive fluid
hoses.
4.
Air compressor: follow manufacturer’s recommen-
dations.
5.
Spray gun or dispensing valve: grounding is ob-
tained through connection to a properly grounded
fluid hose and pump.
6.
Object being sprayed: according to your local
code.
7.
Fluid supply container: according to your local
code.
8.
All solvent pails used when flushing, according to
local code.
Use only metal pails, which are con-
ductive, placed on a grounded surface. Do not
place the pail on a non-conductive surface such as
paper or cardboard, which interrupts the grounding
continuity.
W
X
Z
Y
To ground the pump, loosen the grounding lug locknut (W)
and washer (X). Insert one end of a 12 ga. (1,5 mm
2
) mini-
mum ground wire (Y) into the slot in the lug (Z) and tighten
the locknut securely. See Fig 1. Connect the other end of
the wire to a true earth ground. Order Ground Wire and
Clamp 222–011.
Fig. 1
04940
INJECTION HAZARD
The system pressure must be manually
relieved to prevent the system from
starting or spraying accidentally. Fluid
under high pressure can be injected through the
skin and cause serious injury. To reduce the risk of
an injury from injection, splashing fluid, or moving
parts, follow the
Pressure Relief Procedure
whenever you:
are instructed to relieve the pressure,
stop spraying,
check or service any of the system equipment,
or install or clean the spray tip.
WARNING
Pressure Relief Procedure
1. Engage the spray gun or dispensing valve safety
latch.
2. Turn off the air to the motor.
3. Close the bleed-type master air valve (required).
4. Disengage the safety latch. Hold a metal part of
the gun or valve firmly to a grounded metal pail.
Trigger the gun or valve to relieve pressure.
5. Engage the safety latch.
6. Open the pressure drain valve. Leave the pressure
drain valve open until you are ready to spray
again.
If you suspect that the spray tip or hose is completely
clogged, or that pressure has not been fully relieved
after following the steps above, VERY SLOWLY loos-
en the tip guard retaining nut or hose end coupling to
relieve pressure gradually, then loosen completely.
Now clear the tip or hose obstruction.
Flushing
Before flushing, be sure the entire system and flushing
pails are properly grounded. Refer to
Grounding, at
the left. Follow the
preceding Pressure Relief Proce-
dure and remove the spray tip before flushing. Hold a
metal part of the gun firmly to the side of a metal pail
and use the lowest possible fluid pressure during flush-
ing.