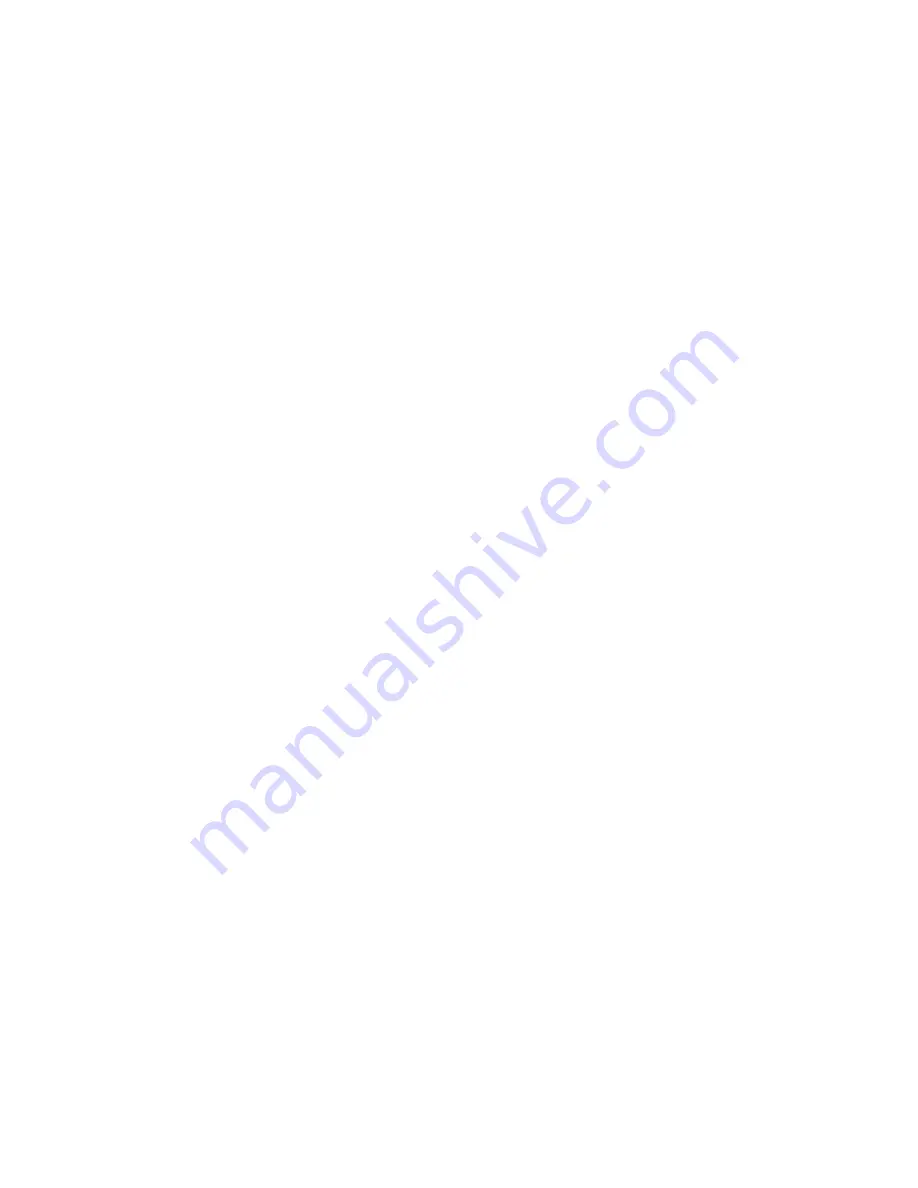
20
External Cleaning
The GSP pump is designed to be washed down with detergent spray and rinse. The
built in motor cover and all stainless steel construction allow plant operators to clean
the outside of the pump with the same procedures used for other processing equipment.
The pump legs allow the floor under the pump to be cleaned as well. In order to
meet 3A 2007, pumps need to have no external seams or rough surfaces which could
encourage bacteria growth or make it difficult to clean. The GSP meets these standards.
Disassembly
Required Tools: The following tools should be available for use during pump
disassembly and assembly.
Wrenches, screwdrivers, lifting sling, rubber mallet, snap-ring pliers, torque wrench
with sockets, allen wrenches, cleaning agents, and feeler gauges.
Warning: Pump components can be heavy. Proper methods of lifting must be employed
to avoid physical injury and/or equipment damage. Steel toed shoes must be worn at all
times.
Warning: The pump may handle hazardous and/or toxic fluids. Proper personal
protective equipment should be worn. Precautions must be taken to prevent physical
injury. Pumpage must be handled and disposed of in conformance with applicable
environmental regulations.
Note: Before disassembling the pump for overhaul, ensure all replacement parts are
available.
Warning: Lock out power supply to driver motor to prevent accidental startup and
physical injury.
1. Shut off all valves controlling flow to and from the pump.
2. Drain liquid from piping and flush pump if necessary.
Warning: Allow all system and pump components to cool before handling them to
prevent physical injury.
3. Disconnect all auxiliary piping and tubing.
4. On close coupled pumps, remove motor hold down bolts.
S1 Series
For the replacement of the mechanical seal a 5 % soap solution is needed.
1. Remove casing bolts.
2. Remove back pull-out assembly from casing . On close coupled units, the back pull
out assembly consists of everything but the casing.
3. On close-coupled units, remove the motor end plug or cover to expose a screwdriver
slot or flats on the end of the motor shaft. Some motors may have flats on the drive
end to be held with an open ended wrench.
4. While restraining the shaft with an appropriate tool (close coupled units) unscrew the
impeller counterclockwise from the shaft. Hold the impeller with a soft cloth during this
process to avoid scratches to the surface. Tapping with a rubber mallet is acceptable if
needed to free the impeller threads. Red Loctite is applied in the factory to the threads.
Some heat may be needed to break it free.
5. Remove the rotary seat by carefully sliding it off the impeller.
Содержание GSP Series
Страница 26: ...26 Notes ...
Страница 27: ...27 Notes ...