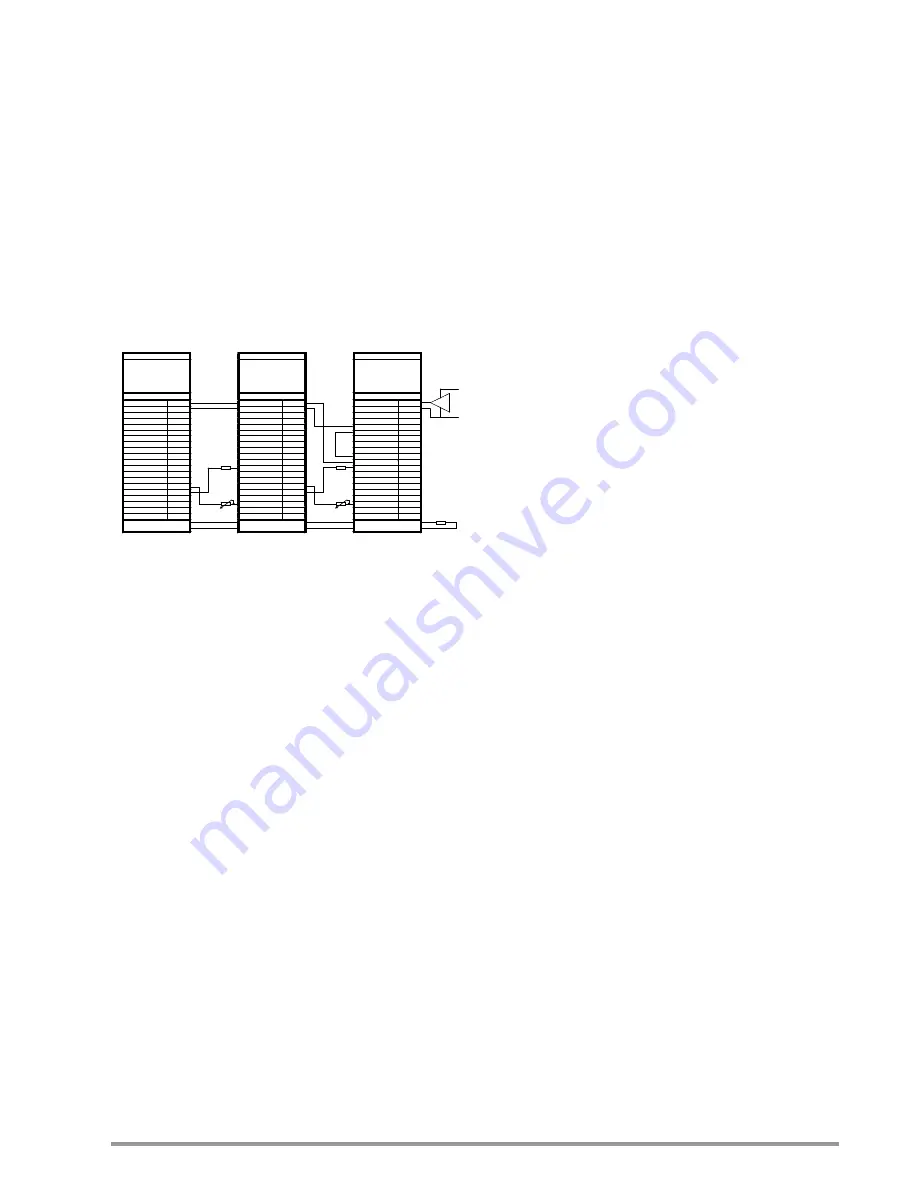
GMC-I Messtechnik GmbH
35
7.9.2
Master-Slave Parallel Connection
Function
As opposed to direct parallel connection, master-slave parallel
connection offers significant advantages:
•
Equally suitable for voltage and current regulation
•
Output parameters (output voltage, cumulative current
limiting) are set entirely by the master device.
•
All interconnected KONSTANTERs are equally loaded.
Wiring
•
Define one power supply as a master device.
•
Connect master and slave devices as shown in figure 7.9.2.
•
Connect the output leads.
•
Balance the individual output current values. Keep connector
cables as short as possible, and use the largest possible
conductor cross-section. Execute balancing with Rsym (set
potentiometer to approx. 2 k
).
Figure 7.9.2 Wiring for Master-Slave Parallel Connection
Settings
Initial power-up:
•
Short circuit the load.
•
Switch the master on (mains) and configure settings:
(Pon rcl) if desired
OUTPUT off
USET = Uset Desired output voltage
ISET = Iset / n
Iset: desired cumulative output current;
n: number of devices
Only valid if nominal data are identical for all
devices, see notes.
•
Switch slave 1 on (mains) and configure:
(Pon rcl) if desired
USET > USET master
The voltage setpoint at the slave devices must
be set at least 1% higher than at the master
device, e.g. to maximum.
ISET = 0 A Deactivate the ISET rotary knob if applicable
by setting ILIM to 0 A.
SEtUP/dPYIF/AI_I on
Activates the analog current setpoint
•
Use the same procedure for additional slave devices.
•
Press the OUTPUT ON key at the slave(s) and the master.
•
Check output current at the slave device displays.
•
Output current at each of the slaves can be precisely matched
to master output current by adjusting Rsym.
•
Changes appear immediately at the respective display.
•
Undo short-circuiting of the load.
From this point on, setting and regulation of (cumulative) output
parameters are controlled entirely by the master device.
Power-up after initial settings:
Devices can be switched on and off in any desired order.
Functional Principle
The master controls output current of the downstream device
(slave 1) via the slave’s current control input with the help of the
current monitoring signal.
Slave 1 functions as a master device for the next downstream
slave (slave 2), and so forth.
Cumulative output current is thus always proportional to master
output current.
Notes
KONSTANTERs with differing nominal values:
The KONSTANTER with the smallest nominal voltage value must
always be used as the master device.
The voltage setting range of the other KONSTANTERs must be
limited to this lowest value using the ULIM parameter.
General
•
The current regulator’s dynamics can be slowed down in
order to achieve more stable performance. Select the
following setting to this end “SEtUP/dEVic/CFG d/C dYn L”.
•
Rsym can be implemented as a 2 k
fixed resistor; adjusting
error for the slaves is increased somewhat as a result.
•
A wire connection can be used instead of Rsym and Rminus
can be omitted, if no precise setpoint value is required for
cumulative output current. In this case, each slave device
supplies slightly more current than the master device.
•
If analog interface connector cables and the sensing leads are
longer than 1 meter, shielded cable should be used. The
shield is connected to the ground terminal on the housing or
to - OUT.
•
The master device’s measuring function acquires commonly
generated output voltage for all interconnected
KONSTANTERs, but only acquires its own output current.
•
The individual measured current values for each of the
interconnected KONSTANTERs must be added together in
order to arrive at cumulative output current.
•
In order to assure that the slaves’ OUTPUT ON status is
activated along with the master’s OUTPUT ON status via the
signal output and trigger input circuit as shown in figure 7.9.2,
“SEtUP/dPYIF/AnIF/SiG-(x1) out” must be selected at the
master and “SEtUP/dPYIF/AnIF/trG-(x2) out” must be
selected at the slaves, (x1) and (x2) in example 1.
The master’s OUTPUT ON status can be optionally controlled
via the trigger input – setting at the master:
“SEtUP/dPYIF/AnIF/trG-(x3) out”, (x3) in example 1.
PSP-KONSTANTER 3
Einstellung
USET = Unenn
ISET = 0 A
OUTPUT ON
SEtUP/dPYIF/AnIF/AI_I
on
(SEtUP/dPYIF/AnIF/trG-1
out
)
Analog Interface
TRG 1 +
1
TRG 1 -
2
TRG 2 +
3
TRG 2 -
4
SIG 1 +
5
SIG 1 -
6
SIG 2 +
7
SIG 2 -
8
SIG 3 +
9
AGND 2
10
+15V 11
AGND 1
12
Uext +
13
Uext -
14
Iext +
15
Iext -
16
U MON
17
I MON
18
SENSE +
19
SENSE -
20
+OUT
í
OUT
PSP-KONSTANTER 2
Einstellung
USET = Unenn
ISET = 0 A
OUTPUT ON
SEtUP/dPYIF/AnIF/AI_I
on
(SEtUP/dPYIF/AnIF/trG-1
out
)
Analog Interface
TRG 1 +
1
TRG 1 -
2
TRG 2 +
3
TRG 2 -
4
SIG 1 +
5
SIG 1 -
6
SIG 2 +
7
SIG 2 -
8
SIG 3 +
9
AGND 2
10
+15V 11
AGND 1
12
Uext +
13
Uext -
14
Iext +
15
Iext -
16
U MON
17
I MON
18
SENSE +
19
SENSE -
20
+OUT
í
OUT
PSP-KONSTANTER 1
Einstellung
USET = Usoll
ISET = Isoll/n
OUTPUT ON
(SEtUP/dPYIF/AnIF/SIG-1
out
)
(SEtUP/dPYIF/AnIF/trG-1
out
)
Analog Interface
TRG 1 +
1
TRG 1 -
2
TRG 2 +
3
TRG 2 -
4
SIG 1 +
5
SIG 1 -
6
SIG 2 +
7
SIG 2 -
8
SIG 3 +
9
AGND 2
10
+15V 11
AGND 1
12
Uext +
13
Uext -
14
Iext +
15
Iext -
16
U MON
17
I MON
18
SENSE +
19
SENSE -
20
+OUT
í
OUT
Last
optional
Us
Rsym
5 k
Rminus
10 k
Rsym
5 k
Rminus
10 k
Slave 2
Master
Slave 1
Содержание P1500
Страница 68: ...68 GMC I Messtechnik GmbH ...
Страница 71: ...GMC I Messtechnik GmbH 71 ...