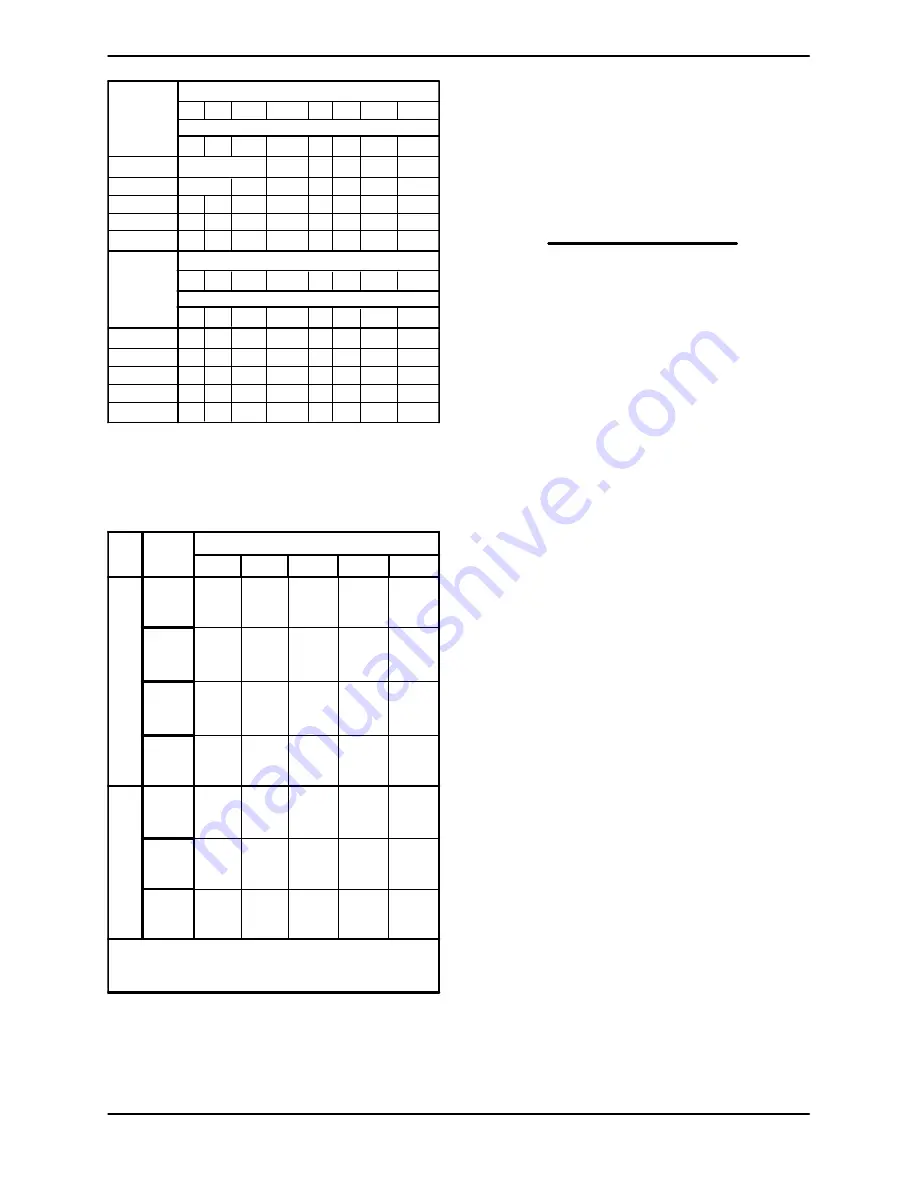
GHS SERIES
OM--05450
PAGE E--11
MAINTENANCE AND REPAIR
GC,GF,GH,GJ
.004
.006
.008 .006
.008
.010
JG,JJ,JL,JP
.004 .006 .008
.010 .006 .008
.010
.012
NK,NM,NP
.006 .006 .008
.010 .006 .008
.010
.012
RM,RP,RR,RS
006 .008 .010
.012 .008 .008
.010
.014
Dimensions are shown in inches. For Viscosities Above
250,000 SSU, or Other Special Applications, Consult Your
Local Gorman-Rupp Distributor or the Factory.
750 2500 25,000 250,000 750 2500 25,000 250,000
225 225 225
225
400 400
400
400
Max. Visc. (SSU)
Max. Temp. (
_
_
_
_
F)
HYD. SIZE
Notes:
GC,GF,GH,GJ .006
.008
.010 .008
.010
.012
JG,JJ,JL,JP
.006 .008 .010
.012 .008 .010
.012
.014
NK,NM,NP
.008 .008 .010
.012 .010 .010
.012
.014
RM,RP,RR,RS
008 .010 .012
.014 .010 .010
.012
.016
750 2500 25,000 250,000 750 2500 25,000 250,000
525 525 525
525
675 675
675
675
Max. Temp. (
_
_
_
_
F)
Max. Visc. (SSU)
HYD. SIZE
Table E-1. End Clearance Based on Hydraulic
Size, Viscosity and Temperature
Rotor
Trim
Code
V
i
s
c
o
s
i
t
y
T
r
i
m
s
Pump Hydraulic Code
Std
.005
.005
.006
.006
.008
D
G
J
N
R
35B
.005
.005
.006
.006
.008
35C
.005
.006
.008
.008
.010
35D
.009
.009
.012
.012
.015
T
e
m
p
T
r
i
m
s
35E
.005
.010
.014
.014
.016
35J
.006
.012
.016
.016
.018
35N
.014
.014
.018
.018
.020
Notes:
For Rotor Trim Codes Not Listed or for Special Applications,
Consult Your Local Gorman-Rupp Distributor or the Factory.
Consult Pump Parts List For Rotor Trim Code.
Table E-2. End Clearance Based on Rotor
Trim Code
RELIEF VALVE DISASSEMBLY
(Figure E-7)
NOTE
If the relief valve is low pressure, it will have one in-
ternal spring (10AE). If the relief valve is high pres-
sure, it will have two internal springs (10AE and
10AF).
Unscrew the cap (10AN) from the bonnet (10AK).
Remove the optional gasket (10AP, if so equipped).
Back off the adjustment capscrew (10AM) to re-
lieve pressure on the spring(s) (10AE and/or
10AF).
Unscrew the bonnet from the valve body (10AA)
and remove the gasket (10AJ) or O-ring (10C). Re-
move the valve (10AD) and spring(s) (10AE and/or
10AF). The spring guide (10AH) is an O-ring fit in
the bonnet. Remove and discard the O-rings.
If the warning plate (10AB) must be replaced, re-
move the drive screws (BM), and remove the plate.