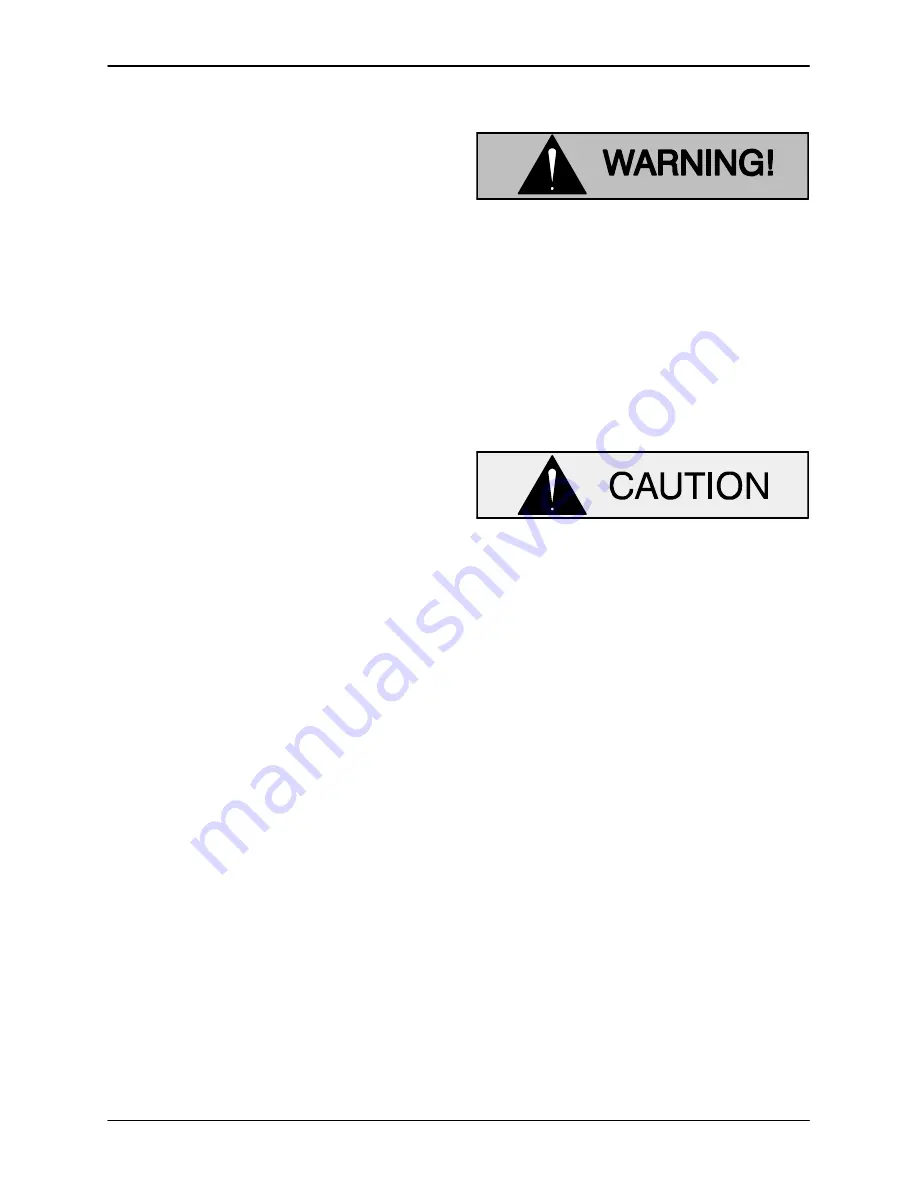
OM--05450
GHS SERIES
PAGE F -- 8
SEAL APPENDIX
Seal Removal
(Figures E-1 and F-3)
See
PUMP DISASSEMBLY
and disassemble the
pump up to and including the
Rotor Adjusting
Sleeve (07)
. As the rotor adjusting sleeve (07AA) is
unscrewed from the backhead (06AA), the seal
stationary element will remain inside the seat
sleeve (07AB).
Remove the seal stationary element and O-ring
from the seat sleeve.
Use caution
not to damage
the stationary element sealing face.
If replacement is required, pry the seat sleeve
(07AB) off the O.D. of the bearing retaining nut
(07AD). Remove the seat sleeve O-ring (07B).
With the head kit (01), idler assembly (02) and rotor
adjusting sleeve (07) removed, push the rotor/
shaft assembly (03A) toward the head end of the
pump until the seal between the shaft and rubber
bellows of the inboard and outboard rotating por-
tion of the seal breaks loose. Slide the rotor/shaft
back into the housing until the rotating portions of
the seal can be grasped. Hold the seal while sliding
the rotor/shaft assembly toward the head end of
the pump until the seal slides completely off the
shaft.
Slide the rotor/shaft assembly out of the housing.
Position the pump on a flat surface with the head
end up and use a dowel to press the inboard sta-
tionary seat out of the inboard seat sleeve (06AK).
Seal Installation
(Figures E-1 and F-3)
See
Pump Reassembly, Section E
, and as-
semble the housing assembly (04), backhead kit
(06) and rotor/shaft assembly (03).
Clean the seal cavity and shaft with a cloth soaked
in fresh cleaning solvent.
Most cleaning solvents are toxic and
flammable. Use them only in a well ven-
tilated area free from flame, sparks, and
excessive heat. Read and follow all pre-
cautions printed on solvent containers.
The seal is not normally reused because wear pat-
terns on the finished faces cannot be realigned
during reassembly. This could result in premature
failure. If necessary to reuse an old seal in an emer-
gency,
carefully
wash all metallic parts in fresh
cleaning solvent and allow to dry thoroughly.
Seal components
must
be kept clean.
Handle seal parts with extreme caution to
prevent damage. Use care not to contami-
nate the precision-finished faces; even fin-
gerprints on the faces can shorten seal life.
If necessary to clean the faces, use a clean
cloth and wipe in a circular pattern.
Inspect the seal components for wear, scoring,
grooves, and other damage that might cause leak-
age. If any components are worn, replace the com-
plete seal;
never mix old and new seal parts
.
If a replacement seal is being used, unwrap the
mechanical seal components. Check that the seal
faces are clean, undamaged and free of any for-
eign matter. Set aside and cover the outboard seal
stationary element and O-ring; it will not be used
until the rotor adjusting sleeve kit (07) is installed.
Place a clean tissue over the seal face of the in-
board seal stationary element, and press the ele-
ment into the bore of the inboard seat sleeve
(06AK) until fully seated.
Position the pump on a flat surface with the drive
end facing up. Lightly oil the shaft of the rotor/shaft
assembly (03A). Position the inboard rotating por-
tion of the seal on the shaft with the sealing face to-
ward the pump end of the shaft.