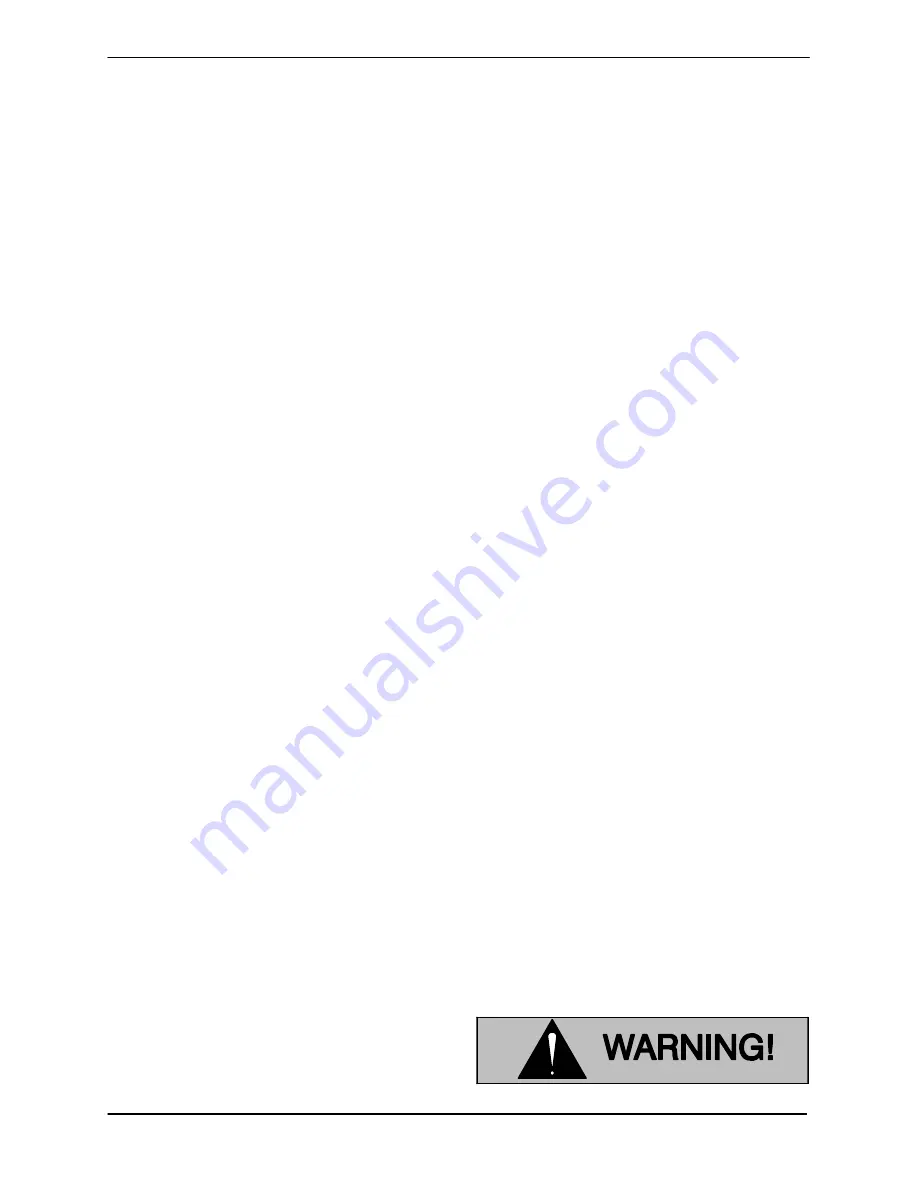
GHS SERIES
OM--05450
PAGE B--4
INSTALLATION
The discharge and suction lines must be inde-
pendently supported to avoid vibration and strain
on the pump. For maximum pumping capacity,
keep the lines as short and straight as possible. El-
bows and fittings used in the lines increase friction
losses; minimize their use. Reducers used in suc-
tion lines should be the eccentric type installed
with the flat part uppermost to avoid creating air
pockets.
Before tightening a connection or flange, align it
exactly with the pump port. Never pull a pipe line
into place by tightening the flange bolts and/or
couplings.
Gauges
Install a vacuum gauge in the suction line and a dis-
charge pressure gauge in the discharge line (both
should be as close as possible to the pump) to
monitor operation and assist in troubleshooting.
Strainers
Because of the close-tolerance moving parts of
this pump, it is recommended that a strainer be in-
stalled in the suction line. The strainer should be
large enough to prevent excessive vacuum, and
capable of operating under high vacuum without
collapsing. The net open area of the strainer
screen depends on liquid viscosity and desired
flow rate; in any case, the sum of the area of all the
holes in the screen should be three to five times the
area of the suction pipe.
Sealing
Even a slight leak will affect priming, head, and ca-
pacity, especially in a suction lift application. Seal
all piping joints, valves and gauges with pipe dope
or teflon tape. The sealing material should be com-
patible with the liquid being pumped.
Valves
To avoid air pockets, install piping valves with the
stem horizontal.
To prevent leakage during shutdown, install a shut-
off valve in the discharge line, particularly on a
flooded suction application. Shutoff valves are not
recommended for suction lines.
It is
not
recommended that a foot valve be installed
at the end of the suction line. If desired to install a
foot valve, consult the factory.
When handling very hot or cold liquids, install a
pressure relief valve in any part of the system that
can be valved off or isolated; this will protect piping
against damage from liquid thermal expansion or
contraction from temperature changes during
shutdown.
Barrier Liquids for Dual Mechanical Seals
Pumps equipped with dual (tandem) mechanical
seals require a barrier liquid to prevent contamina-
tion of the seal assembly by the liquid being
pumped. The barrier liquid must have the following
characteristics:
a. The barrier liquid must have sufficient lubricat-
ing characteristics, including an optimum vis-
cosity of 1 to 5 cSt at the temperature of the
liquid being pumped.
b. The barrier liquid must be compatible in all re-
spects with all pump and seal components to
which it will be exposed.
c. The barrier liquid must be compatible in all re-
spects with the liquid being pumped.
Pumps equipped with dual mechanical seals re-
quire the barrier liquid to be supplied at a continu-
ous pressure equivalent to the maximum dis-
charge pressure in order to avoid inboard seal face
separation. The maximum barrier liquid pressure
that can be applied depends primarily on the maxi-
mum seal design pressure (consult the factory).
Do not
pressurize tandem seals. Pressurizing a
tandem seal will cause the seal faces to separate,
resulting in leakage and/or damage to the seal.
Refer to the appropriate section in
Seal Appendix,
Section F
for your specific seal option for operating
instructions for the barrier liquid reservoir kit.
ALIGNMENT
Make certain that power to the drive unit