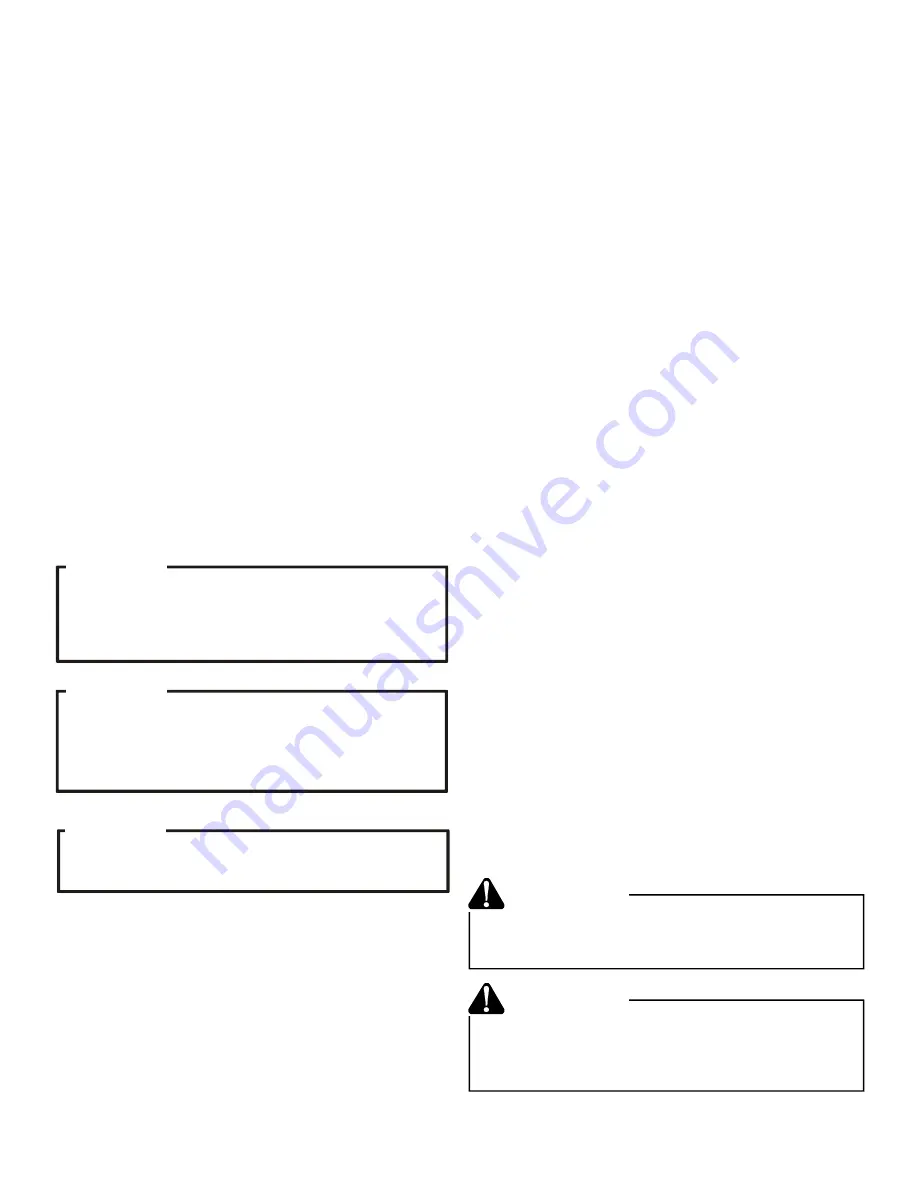
4
Insulation is necessary to prevent condensation from forming
and dropping from the suction line. Armflex (or satisfactory
equivalent) with 3/8” min. wall thickness is recommended. In
severe conditions (hot, high humidity areas) 1/2” insulation may
be required. Insulation must be installed in a manner which
protects tubing from damage and contamination.
Where possible, drain as much residual compressor oil from
existing systems, lines, and traps; pay close attention to low
areas where oil may collect.
NOTE:
If changing refrigerant
types, ensure the indoor coil and metering device is compat-
ible with the type of refrigerant being used; otherwise, the in-
door coil must be replaced.
Burying Refrigerant Lines
If burying refrigerant lines can not be avoided, use the following
checklist.
1. Insulate liquid and suction lines separately.
2. Enclose all underground portions of the refrigerant lines
in waterproof material (conduit or pipe) sealing the ends
where tubing enters/exits the enclosure.
3. If the lines must pass under or through a concrete slab,
ensure lines are adequately protected and sealed.
Refrigerant Line Connections
NOTICE
THIS UNIT IS SHIPPED WITH A NITROGEN/HELIUM
HOLDING CHARGE ONLY. UNIT MUST BE EVACUATED
AND CHARGED PER INSTALLATION INSTRUCTIONS
WITH REFRIGERANT LISTED ON SERIAL RATING PLATE.
NOTICE
UNITS SHIPPED WITH A HOLDING CHARGE ARE
INTENDED FOR COMPONENT REPLACEMENT ONLY ON
EXISTING SYSTEMS, AND NOT INTENDED FOR USE IN
NEW SYSTEMS OR NEWLY CONSTRUCTED HOMES.
NOTICE
UNITS MUST ONLY BE USED AS REPLACEMENT
COMPONENTS FOR PRE-2010 INSTALLED SYSTEMS.
NOTE:
Holding charge must be removed before brazing. Open
service valves slowly to remove holding charge. Close valves
before brazing to prevent contaminants from entering system.
IMPORTANT
To avoid overheating the service valve, TXV valve, or filter
drier while brazing, wrap the component with a wet rag, or
use a thermal heat trap compound. Be sure to follow the
manufacturer’s instruction when using the heat trap
compound. Note: Remove Schrader valves from service
valves before brazing tubes to the valves. Use a brazing
alloy of 2% minimum silver content. Do not use flux.
Torch heat required to braze tubes of various sizes is
proportional to the size of the tube. Tubes of smaller size
require less heat to bring the tube to brazing temperature
before adding brazing alloy. Applying too much heat to
any tube can melt the tube. Service personnel must use
the appropriate heat level for the size of the tube being
brazed. Note: The use of a heat shield when brazing is
recommended to avoid burning the serial plate or the finish
on the unit.
1. The ends of the refrigerant lines must be cut square, de-
burred, cleaned, and be round and free from nicks or dents.
Any other condition increases the chance of a refrigerant
leak.
2. “Sweep” the refrigerant line with nitrogen or inert gas dur-
ing brazing to prevent the formation of copper-oxide in-
side the refrigerant lines. This may cause a blockage or
failure of the metering device.
3. After brazing, quench the joints with water or a wet cloth
to prevent overheating of the service valve.
4. Ensure the filter drier paint finish is intact after brazing. If
the paint of the steel filter drier has been burned or chipped,
repaint or treat with a rust preventative. This is especially
important on suction line filter driers which are continu-
ally wet when the unit is operating.
NOTE:
Be careful not to kink or dent refrigerant lines. Kinked
or dented lines will cause poor performance or compressor
damage.
Do NOT make final refrigerant line connection until plugs are
removed from refrigerant tubing.
NOTE:
Before brazing, verify indoor piston size by checking
the piston kit chart packaged with indoor unit.
Leak Testing (Nitrogen or Nitrogen-Traced)
To avoid the risk of fire or explosion, never use
oxygen, high pressure air or flammable gases for leak
testing of a refrigeration system.
WARNING
To avoid possible explosion, the line from the
nitrogen cylinder must include a pressure regulator
and a pressure relief valve. The pressure relief valve
must be set to open at no more than 150 psig.
WARNING
Содержание GSC13018
Страница 10: ...10 THIS PAGE INTENTIONALLY LEFT BLANK...
Страница 11: ...11 THIS PAGE INTENTIONALLY LEFT BLANK...