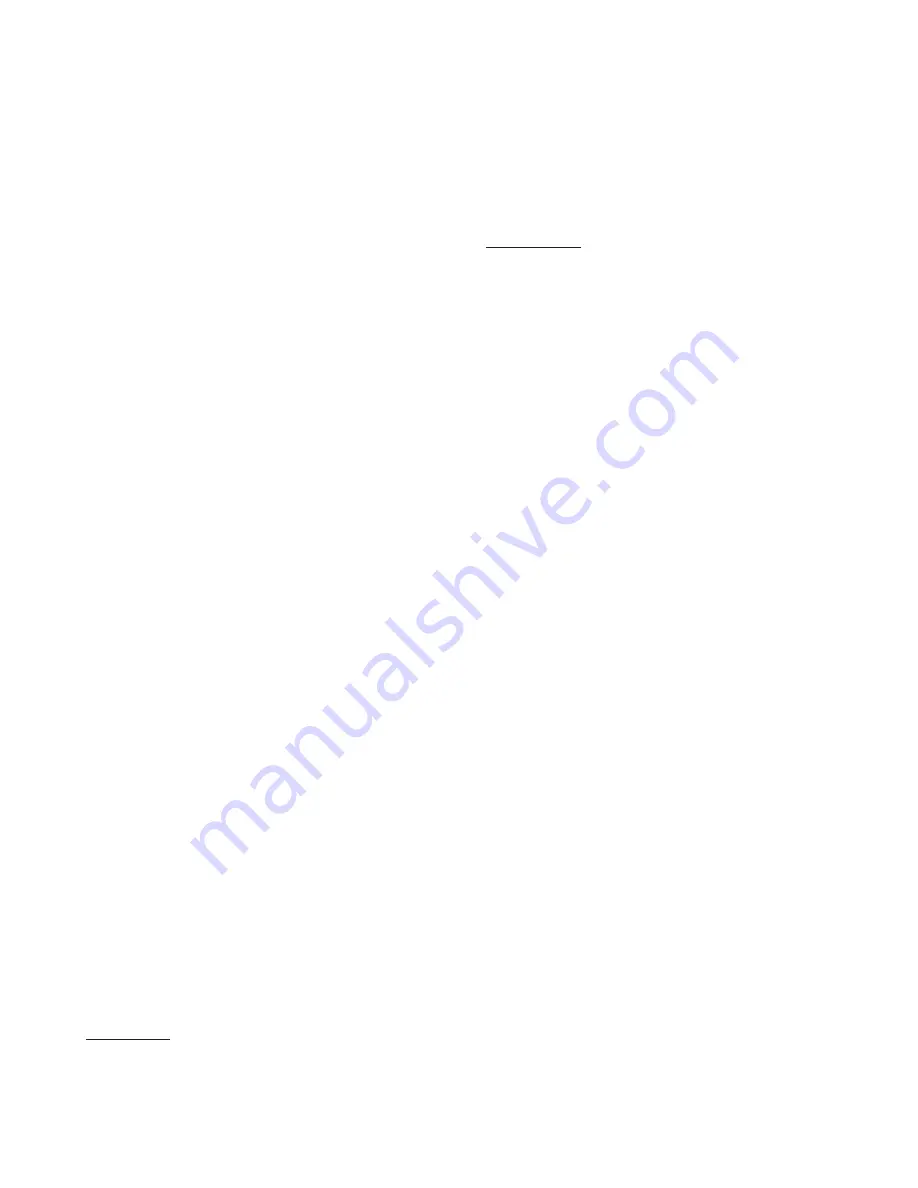
SYSTEM OPERATION
31
UPRIGHT FILTER INSTALLATIONS
Depending on the installation and/or customer preference,
differing filter arrangements can be applied. Filters can be
installed in the central return register and a side panel exter-
nal filter rack kit (upflow filter kit # EFR02 As an alternative a
media air filter or electronic air cleaner can be used as the
requested filter. Refer to the following minimum filter require-
ment charts for determination of the minimum filter area to
ensure proper unit performance. The following figures show
possible filter locations.
Refer to Minimum Filter Area tables to determine filter area
requirement.
NOTE:
Filters can also be installed elsewhere
in the duct system such as a central return.
Horizontal Installations
Filter(s) must be installed external to the furnace casing for
horizontal installations. For most installations it is prefer-
able to use a central return with filters installed in the duct
behind the return air grill. In this way filter replacement is
relatively simple by merely removing the grille, rather than
going into the attic or crawl space.
ADDITIONAL FILTERING ACCESSORIES
External Filter Rack Kit (EFR02)
The external filter rack kit is intended to provide a location
external to the furnace casing, for installation of a perma-
nent filter on upflow model furnaces. The rack is designed to
mount over the indoor blower compartment area of either
side panel, and provide filter retention as well as a location
for attaching return air ductwork.
Electronic Air Cleaner (ASAS and GSAS) or Media Air
Cleaner (AMU and GMU)
The electronic air cleaner and media air cleaner are multi-
positional high efficiency air filtration devices that can be
installed in any position, except with the access door facing
down. The best location for the air cleaner is in the return air
duct next to the blower compartment. Before installing the
air cleaner, consider the application. The electronic air cleaner
must be readily accessible for periodic inspection and clean-
ing of the pre-filters and electronic cells while the media air
cleaner must be readily accessible for periodic inspection
and replacement of the Media Air Cleaner (AMU and GMU)
filter cartridge (3 per carton) M0-1056, M1-1056, M2-1056,
M8-1056, to maintain maximum efficiency and trouble-free
operation. Carbon Filters 1156-3 and 1856-3 (set of 3) are
also available. See Product Catalog for exact filter for your
model. A full line of air filtration and indoor air quality prod-
ucts are available and can be seen at www.goodmanmfg.com.
SEQUENCE OF OPERATION
POWER UP:
·
When power is supplied, the control will energize the
Red LED, microcomputer runs its self-check routine.
·
The control will check the status of the gas valve cir-
cuitry.
·
Line polarity is checked.
·
The control then enters standby waiting for a call for
heat or cool.
·
The Furnace status LED will display a slow green
flash signaling standby mode
HEAT MODE:
Call For 1st Stage Heat
·
On a call for first stage heat, the thermostat contacts
close signaling the control module.
· The microcomputer runs its self-check routine.
·
The Amber LED will display a slow flash signaling
normal heat operation.
·
The control module checks the high limit (and/or aux-
iliary limit) switch(es) for normally closed contacts.
·
The control checks the low pressure switch for a
shorted condition.
·
The gas valve relay status is checked for proper op-
eration. Once the low pressure switch is detected
open, the inducer blower is energized at high speed
and the humidifier is enabled.
·
The low pressure switch is checked for closure.
·
Once the low pressure switch is closed, the pre-purge
period begins. The inducer will be energized at high
speed for the pre-purge period.
·
Following the completion of pre-purge, the inducer
switches to low speed and the igniter warm up period
begins.
·
After completion of the igniter warm up period:
- Trial for ignition begins.
- The first stage of the gas valve is energized.
·
The igniter is de-energized when flame is sensed or
at the conclusion of the ignition activation period (IAP),
whichever comes first.
·
When flame is sensed, the delay to heat on period
begins timing.
·
Retry counter is zeroed, if after 10 seconds the flame
is sensed:
- Control enters normal operating loop where all
inputs are continuously checked.
·
After the delay to heat on period, the circulator fan is
energized at the low heat speed.
·
The air cleaner will be energized with the circulator.
·
If the call for heat is lost while the control is in the trial
for ignition period without flame being detected, the
control will turn off the gas valve and igniter. The con-
trol then enters the post-purge routine. The post-purge
time will be increased to 60 seconds. After complet-
ing the post-purge, the control resumes normal op-
eration.