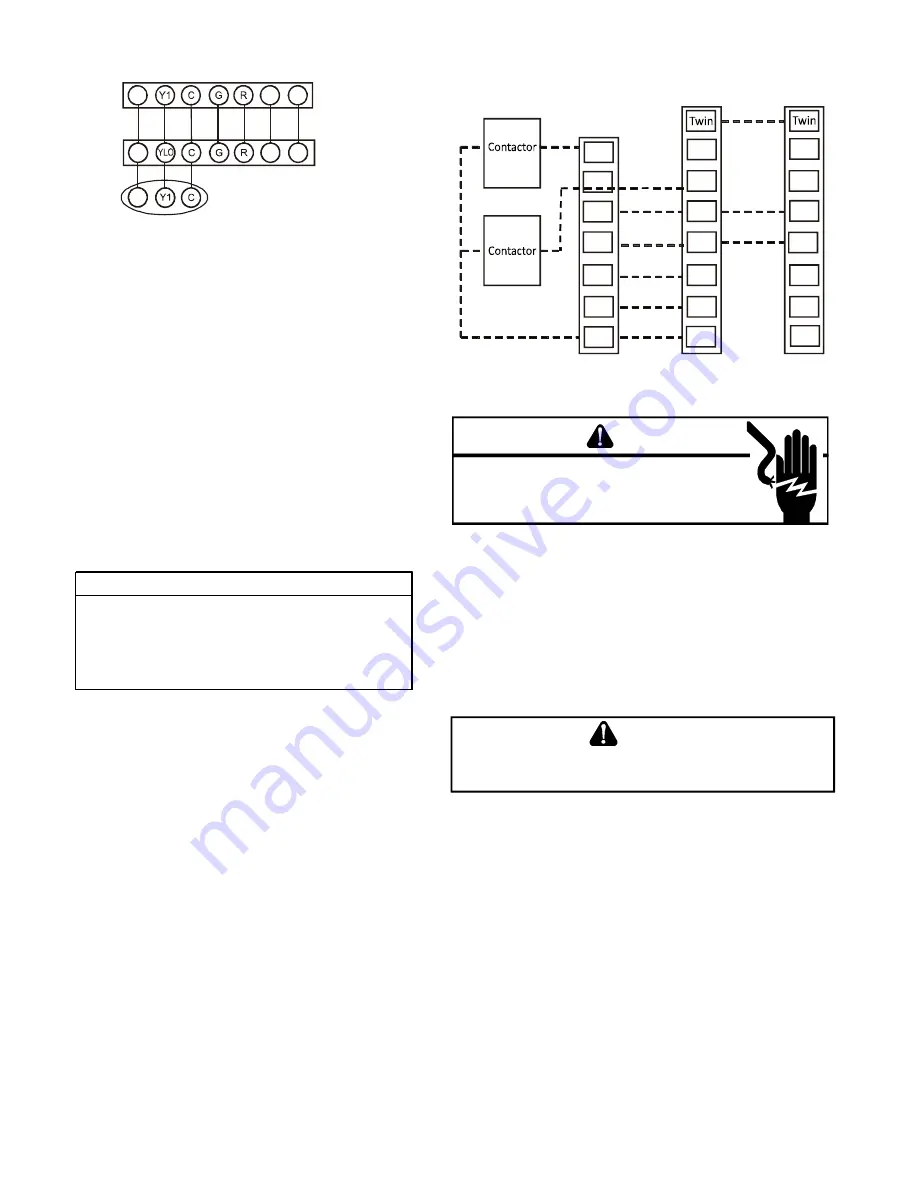
INSTALLATION CONSIDERATIONS
26
W1
W2
Y
Furnace
Integrated
Control
Module
Remote Condensing Unit
(Two-Stage Cooling)
Y2
W1
W2
Y2
Thermostat - Two-Stage Heating with Two-Stage Cooling
Thermostat Wiring Diagrams
S
INGLE
-S
TAGE
H
EATING
T
HERMOSTAT
A
PPLICATION
A single-stage thermostat with only one heating stage may
be used to control this furnace. The application of a single-
stage thermostat offers a
timed
transition from low to high
fire. The furnace will run on low stage for a fixed period of
time before stepping up to high stage to satisfy the
thermostat’s call for heat. The delay period prior to step-
ping up can be set at either a fixed 10 or 20 minute time
delay or a load based variable time between 1 and 12 min-
utes (AUTO mode). If the AUTO mode is selected, the con-
trol averages the cycle times of the previous three cycles
and uses the average to determine the time to transition
from low stage to high stage.
DIP Switch
S1-1
S1-2
Heat Staging
OFF
OFF
2 Stage Stat*
ON
OFF
10 min delay
(factory setting) OFF
ON
AUTO
ON
ON
20 min delay
* no high fire without W2 call
Staging DIP Switches
T
WINNING
Using the “TWIN” terminals and proper wiring enables two
*MEC96 furnaces of the same model and size to be twinned.
Twinning allows simultaneous operation of two furnaces and
forces the indoor blower motors of each furnace to operate
synchronously into a common duct system. Using the twin-
ning function will require only field installed wiring with no
external kits or parts.
·
The staging DIP switches and speed tap DIP switches
must be set the same on both furnaces.
Room
Thermostat
Y2
Y
W
W2
R
G
C
Ylo
Y
W
W2
R
G
C
Ylo
Y
W
W2
R
G
C
Furnace 1
Furnace 2
CIRCULATOR BLOWER SPEED ADJUSTMENT
WARNING
HIGH
VOLTAGE
D
ISCONNECT
ALL
POWER BEFOR CHANGING SPEED TAPS.
M
ULTIPLE POWER SOURCES MAY BE PRESENT.
F
AILURE TO DO
SO MAY CAUSE PROPERTY DAMAGE, PERSONAL INJURY OR DEATH.
This furnace is equipped with a multi-speed ECM motor.
Two wiring harnesses connect the motor to the integrated
control board and furnace power supply. The line voltage
(115 VAC) power supply to the motor is constant and not
switched by the control board. Motor operation is also de-
pendent on a 24 VDC signal on one of the four speed taps
on the motor. The airflow tables for heating and cooling
speeds show the relationship between airflow (CFM) and
external static pressure for each size furnace.
T
O
AVOID
PERSONAL
INJURY
OR
DEATH
DUE
TO
ELECTRICAL
SHOCK
,
TURN
OFF
POWER
TO
THE
FURNACE
BEFORE
CHANGING
SPEED
TAPS
.
WARNING
Circulator Blower Speed Facts
1. Motor speed Tap wiring must remain in factory posi-
tion on the control board and motor.
2. There are 4 speed Tap wires to the motor T1, T2, T3,
T4.
3. There are 5 speeds available, depending on DIP switch
settings and found in air flow table for each size fur-
nace.
4. T1 terminal is always energized for Low Heat / Con-
stant Fan speed.
5. T2 terminal is always energized for High Heat speed.
6. T3 terminal is always energized in Low Cooling.
7. T4 terminal is always energized in High Cooling.