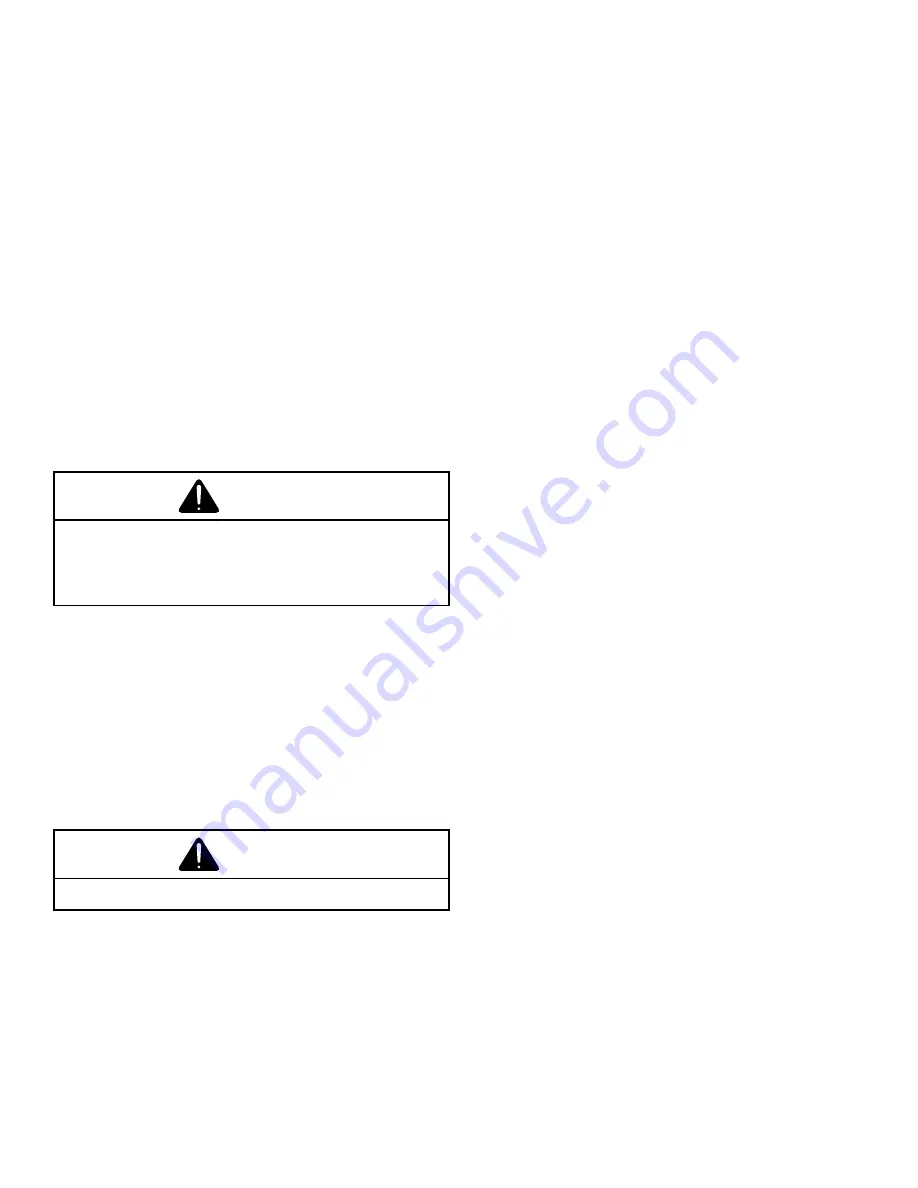
SERVICING
40
If delayed ignition should occur, the following should be
checked. Furnace design makes this extremely unlikely
unless safety controls have been by-passed or tampered
with. Never by-pass or alter furnace controls.
1. Improper gas pressure - adjust to proper pressure.
2. Improper burner positioning - burners should be in
locating slots, level front to rear and left to right.
3. Carry over (lighter tube or cross lighter) obstructed -
clean.
4.
Main burner orifice(s) deformed, or out of alignment to
burner - replace.
CHECKING INTEGRATED IGNITION CONTROL
BOARDS
NOTE: Failure to earth ground the furnace,
reversing the neutral and hot wire connection
to the line (polarity), or a high resistance
connection in the neutral line may cause the
control to lockout due to failure to sense flame.
WARNING
To avoid the risk of electrical shock, wiring
to the unit must be properly polarized and
grounded. Disconnect power before performing
service listed below.
The ground wire must run from the furnace all the way back
to the electrical panel. Proper grounding can be confirmed
by disconnecting the electrical power and measuring
resistance between the neutral (white) connection and the
burner closest to the flame sensor. Resistance should be
less than 2 ohms.
The ignition control is a combination electronic and
electromechanical device and is not field repairable.
Complete unit must be replaced.
WARNING
Line voltage now present
These tests must be completed within a given time frame
due to the operation of the ignition control. The trial for
ignition period is 4 seconds.
The ignition control is capable of diagnosing many furnace
failures to help in troubleshooting. The control utilizes a
dual, 7-segment LED display to indicate diagnostic codes.
When the control is powered up normally the light will be on
continuously. The display wil indicate “ON” when powered
and in standby mode. This can be used to test for 120
volts and 24 volts to the control since both must be present
for the light to be on. If this step fails, check for 120 volts
to the control and check the transformer and its associated
wiring. If this step is successful give the control a call for
heat and wait five (5) seconds or until the furnace goes
into lockout. If the control detects a failure it will now be
shown on the diagnostic indicator light/display. Refer to the
Abnormal Operation section in the Sequence of Operation
section of this manual for more detail on failure codes.
1. Check for 120 volts from Line 1 (Hot) to Line 2 (Neutral)
at the ignition control. No voltage, check the door switch
connections and wire harness for continuity.
2. With the thermostat calling for heat, check for 24 volts
from W to C terminal on the ignition control. No voltage.
Check transformer, room thermostat, and wiring.
If you have 24 volts coming off the transformer but
receive approximately 13 volts on the terminal board
between (C) and (R), check for blown fuse.
3. Check for 120 volts to the induced draft blower
(low-stage) by measuring voltage between Pin 3
and Pin 4 (on the 5-pin connector) located on circuit
board. No voltage, check for loose connection
in the 5-pin connector or replace ignition control.
Check for 120 volts to the induced draft blower (high-
stage) by measuring voltage between Pin 2 and Pin 4 (on
the 5-pin connector) located on circuit board. No voltage,
check for loose connection in the 5-pin connector, no call
for high stage heat or replace ignition control.
4. If voltage is present in Steps 1 through 3 and the induced
draft blower is operating, check for 120 volts to the ignitor
during the preheat cycle. Measure voltage between Pin
1 and Pin 5 (on the 5-pin connector) located on ignition
control. No voltage, check low stage and high stage
pressure switches or replace the ignition control board.
5. After the ignitor warm-up time, begin checking for 24
volts to the gas valve. Voltage will be present for seven
seconds only if proof of flame has been established.
6.
If proof of flame was established voltage will be provided
to the air circulation blower following the heat on delay
period.
a. BEFORE replacing the ECM motor assembly or
the end bell, first check the motor with a Goodman
#UTT-01 UltraCheck-EZTM diaganostic tool . If
the motor runs with the diagnostic tool, the motor
is good. To check the end bell, see the previous
variable speed testing section of this manual before
replacing the end bell.
b. The two-stage variable speed furnaces should have
120 Volts at the motor at all times, even without a
call for cooling or heating. These motors receive their
operational signals through the 4-pin wiring harness,
connected between the motor and integrated control
board.