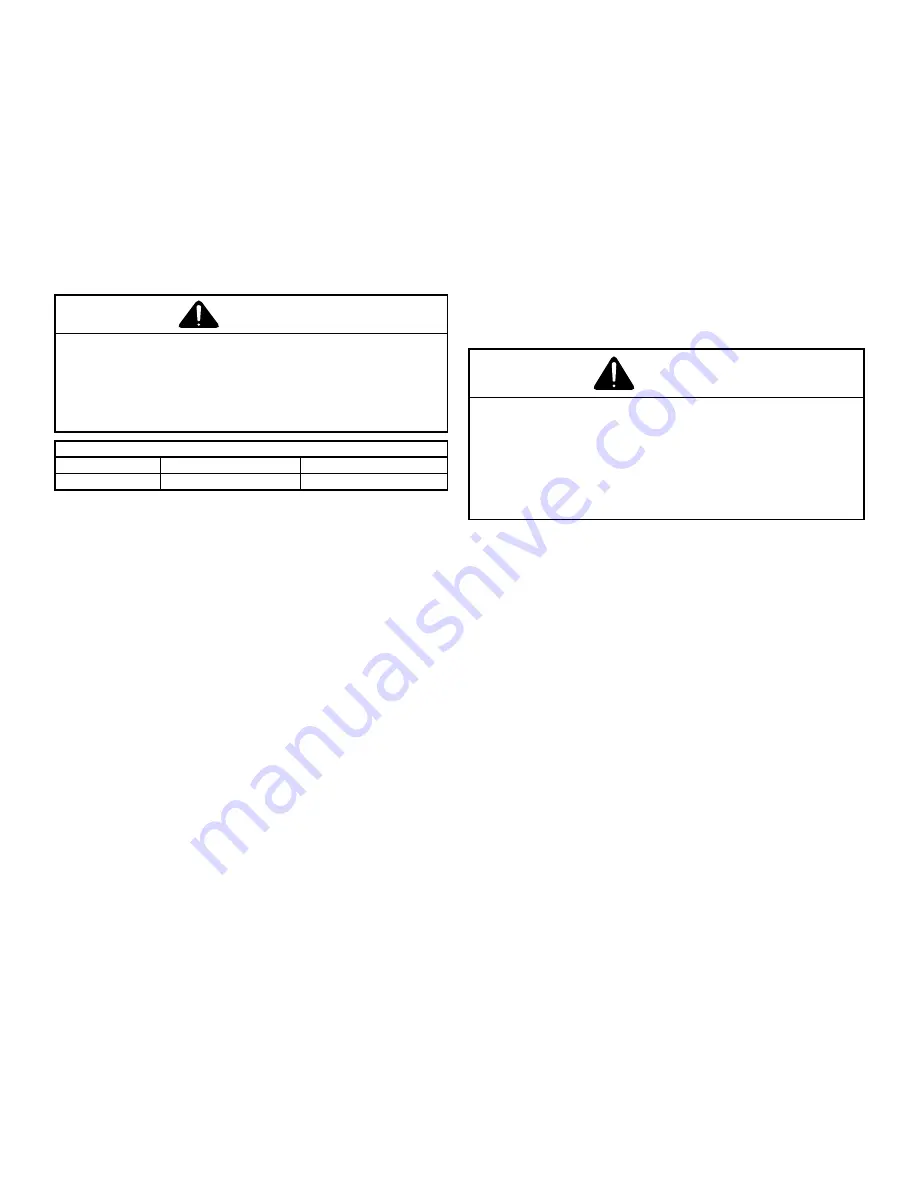
SYSTEM OPERATION
17
Gas Heat Trim Factor Option Menu
Gas Heat airflow may be trimmed from -10% to +10% in
2% increments.
Gas Heat Stage Multiplier Menu (CFM)
This menu allows adjustment of the low fire CFM multiplier.
The default CFM for low fire is 70% of high fire.
Gas Pressure Test Menu
This menu allows 100% firing rate be locked in to check
gas valve pressure.
CAUTION
To prevent unreliable operation or equipment
damage, the inlet gas supply pressure must
be as specified on the unit rating plate with
all other household gas fired appliances
operating.
Inlet Gas Supply Pressure
Natural Gas
Minimum: 4.5” w.c. Maximum: 10.0” w.c.
Propane Gas
Minimum: 11.0” w.c. Maximum: 13.0” w.c.
Gas Supply and Piping
The furnace rating plate includes the approved furnace gas
input rating and gas types. The furnace must be equipped
to operate on the type of gas applied. This includes any
conversion kits required for alternate fuels and/or high
altitude.
Inlet gas supply pressures must be maintained within
the ranges specified in the following table. The supply
pressure must be constant and available with all other
household gas fired appliances operating. The minimum
gas supply pressure must be maintained to prevent
unreliable ignition. The maximum must not be exceeded to
prevent unit overfiring.
High Altitude Derate
When this furnace is installed at high altitude, the
appropriate High Altitude orifice kit must be applied. This is
required due to the natural reduction in the density of both
the gas fuel and combustion air as altitude increases. The
kit will provide the proper design certified input rate within
the specified altitude range.
High altitude kits are purchased according to the
installation altitude and usage of either natural or
propane gas. Consult the furnace Specification Sheet for
appropriate kits.
Do
not
derate the furnace by adjusting the manifold
pressure to a lower pressure than specified on the furnace
rating plate. The combination of the lower air density and
a lower manifold pressure will prohibit the burner orifice
from drawing the proper amount of air into the burner. This
may cause incomplete combustion, flashback, and possible
yellow tipping.
In some areas the gas supplier may artificially derate the
gas in an effort to compensate for the effects of altitude. If
the gas is artificially derated, the appropriate orifice size
must be determined based upon the BTU/ft
3
content of the
derated gas and the altitude. Refer to the National Fuel
Gas Code, NFPA 54/ANSI Z223.1 or CAN/CSA B149.1-15
in Canada, and information provided by the gas supplier to
determine the proper orifice size.
A different pressure switch may be required at high altitude
regardless of the BTU/ft
3
content of the fuel used. Consult
the furnace Specification Sheet for pressure switch.
Propane Gas Conversion
WARNING
Possible property damage, personal injury or
death may occur if the correct conversion kits
are not installed. The appropriate kits must
be applied to ensure safe and proper furnace
operation. All conversions must be performed
by a qualified installer or service agency.
This furnace is configured for natural gas but may be
converted for use with L.P. gas. The prescribed conversion
kit must be used when converting to L.P. gas. Refer
to the Accessory section in this manual or the furnace
Specification Sheet for kit information.
The indicated kits must be used to insure safe and proper
furnace operation. All conversions must be performed by a
qualified installer, or service agency.
Gas Valve
This unit is equipped with a 24 volt gas valve controlled
during furnace operation by the integrated control
module. As shipped, the valve is configured for natural
gas. The valve is field convertible for use with propane
gas by replacing the regulator spring with a propane gas
spring from an appropriate manufacturer’s propane gas
conversion kit. Taps for measuring the gas supply pressure
and manifold pressure are provided on the valve.
The gas valve has a manual ON/OFF control located on
the valve itself. This control may be set only to the “ON”
or “OFF” position. Refer to the lighting instructions label
or
Startup Procedure & Adjustment
for use of this control
during start up and shut down periods.
Always use a back-up wrench when making the connection
to the gas valve to keep it from turning. The orientation
of the gas valve on the manifold must be maintained as
shipped from the factory. Maximum torque for the gas valve
connection is 375 in-lbs; excessive over-tightening may
damage the gas valve.