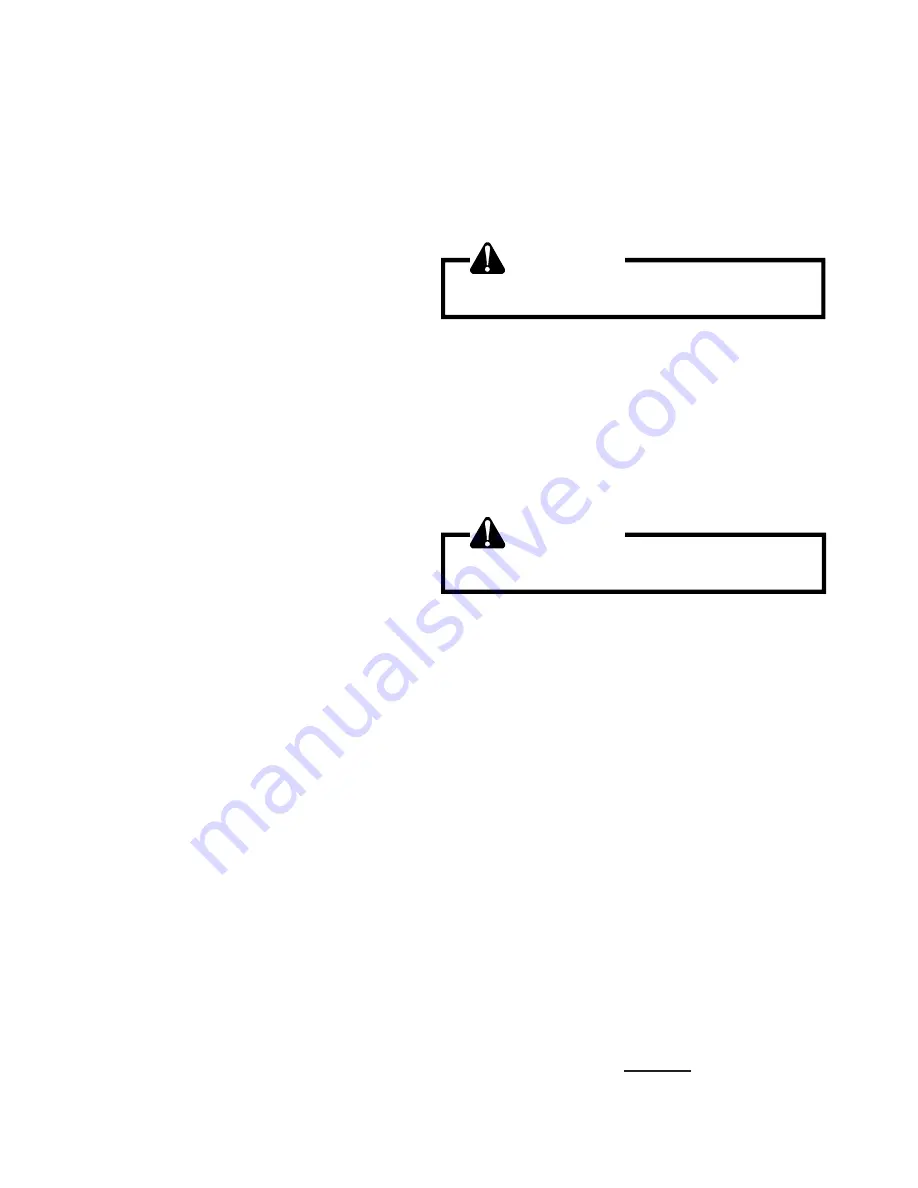
SERVICING
50
S-112 CHECKING RESTRICTED LIQUID LINE
When the system is operating, the liquid line is warm to the
touch. If the liquid line is restricted, a definite temperature
drop will be noticed at the point of restriction. In severe cases,
frost will form at the restriction and extend down the line in the
direction of the flow.
Discharge and suction pressures will be low, giving the
appearance of an undercharged unit. However, the unit will
have normal to high subcooling.
Locate the restriction, replace the restricted part, replace
drier, evacuate and recharge.
S-113 OVERCHARGE OF REFRIGERANT
An overcharge of refrigerant is normally indicated by an
excessively high head pressure.
An evaporator coil, using an expansion valve metering device,
will basically modulate and control a flooded evaporator and
prevent liquid return to the compressor.
An evaporator coil, using a fixed orifice restrictor device
(flowrator) metering device, could allow refrigerant to return to
the compressor under extreme overcharge conditions.
Also with a fixed orifice restrictor device (flowrator) metering
device, extreme cases of insufficient indoor air can cause
icing of the indoor coil and liquid return to the compressor, but
the head pressure would be lower.
There are other causes for high head pressure which may be
found in the "Service Problem Analysis Guide."
If other causes check out normal, an overcharge or a system
containing non-condensables would be indicated.
If this system is observed:
1. Start the system.
2. Remove and capture small quantities of refrigerant as
from the suction line access fitting until the head pressure
is reduced to normal.
3. Observe the system while running a cooling performance
test. If a shortage of refrigerant is indicated, then the
system contains non-condensables.
S-114 NON-CONDENSABLES
If non-condensables are suspected, shut down the system
and allow the pressures to equalize. Wait at least 15
minutes. Compare the pressure to the temperature of the
coldest coil since this is where most of the refrigerant will be.
If the pressure indicates a higher temperature than that of the
coil temperature, non-condensables are present.
Non-condensables are removed from the system by first
removing the refrigerant charge, replacing and/or installing
liquid line drier, evacuating and recharging.
S-115 COMPRESSOR BURNOUT
When a compressor burns out, high temperature develops
causing the refrigerant, oil and motor insulation to decom-
pose forming acids and sludge.
If a compressor is suspected of being burned-out, attach a
refrigerant hose to the liquid line dill valve and properly remove
and dispose of the refrigerant.
NOTICE
Violation of EPA regulations may result in fines
or other penalties.
Now determine if a burn out has actually occurred. Confirm
by analyzing an oil sample using a Sporlan Acid Test Kit, AK-
3 or its equivalent.
Remove the compressor and obtain an oil sample from the
suction stub. If the oil is not acidic, either a burnout has not
occurred or the burnout is so mild that a complete clean-up
is not necessary.
If acid level is unacceptable, the system must be cleaned by
using the clean-up drier method.
CAUTION
Do not allow the sludge or oil to contact the skin.
Severe burns may result.
NOTE:
The Flushing Method using R-11 refrigerant is no
longer approved by Amana
®
Brand Heating-Cooling.
Suction Line Drier Clean-Up Method
The POE oils used with R410A refrigerant is an excellent
solvent. In the case of a burnout, the POE oils will remove any
burnout residue left in the system. If not captured by the
refrigerant filter, they will collect in the compressor or other
system components, causing a failure of the replacement
compressor and/or spread contaminants throughout the
system, damaging additional components.
Use part number RF000127 suction line filter drier kit. This
drier should be installed as close to the compressor suction
fitting as possible. The filter must be accessible and be
rechecked for a pressure drop after the system has operated
for a time. It may be necessary to use new tubing and form
as required.
NOTE:
At least twelve (12) inches of the suction line
immediately out of the compressor stub must be discarded
due to burned residue and contaminates.
1. Remove compressor discharge line strainer.
2. Remove the liquid line drier and expansion valve.
3
Purge all remaining components with dry nitrogen or
carbon dioxide until clean.
4. Install new components
including
liquid line drier.
5. Braze all joints, leak test, evacuate, and recharge sys-
tem.