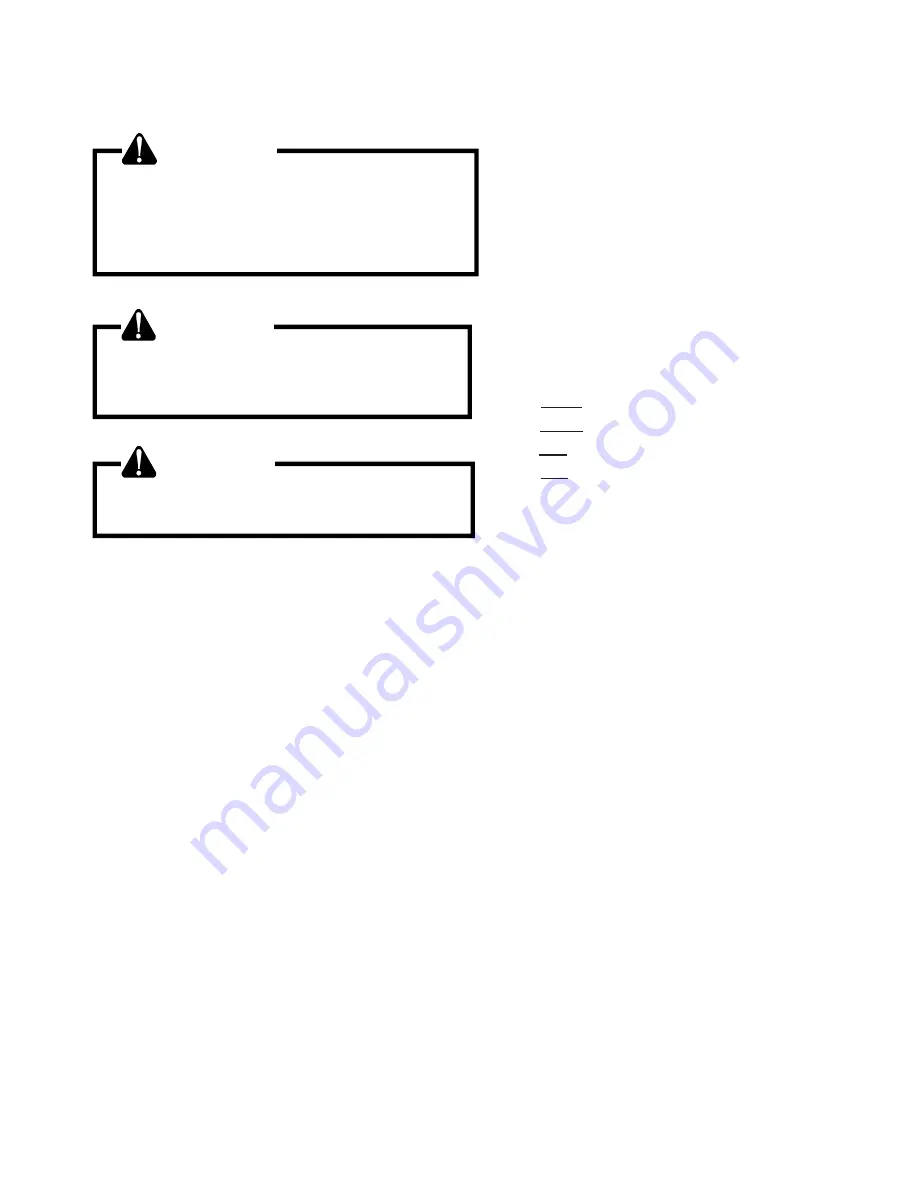
SERVICING
45
S-103 CHARGING
WARNING
REFRIGERANT UNDER PRESSURE!
* Do not overcharge system with refrigerant.
* Do not operate unit in a vacuum or at negative
pressure.
Failure to follow proper procedures may cause
property damage, personal injury or death.
CAUTION
Use refrigerant certified to ARI standards. Used
refrigerant may cause compressor damage and will
void the warranty. Most portable machines cannot
clean used refrigerant to meet ARI standards.
CAUTION
Operating the compressor with the suction valve
closed will void the warranty and cause serious
compressor damage.
Charge the system with the exact amount of refrigerant.
Refer to the specification section or check the unit name-
plates for the correct refrigerant charge.
An inaccurately charged system will cause future prob-
lems.
1. Using a quality set of charging scales, weigh the proper
amount of refrigerant for the system. Allow liquid refriger-
ant only to enter the high side.
2. After the system will take all it will take, close the valve
on the high side of the charging manifold.
3. Start the system and charge the balance of the refrigerant
through the low side.
NOTE: R410A should be drawn out of the storage container
or drum in liquid form due to its fractionation properties, but
should be "Flashed" to its gas state before entering the
system. There are commercially available restriction devices
that fit into the system charging hose set to accomplish this.
DO NOT
charge liquid R410A into the compressor.
4. With the system still running, close the valve on the
charging cylinder. At this time, you may still have some
liquid refrigerant in the charging cylinder hose and will
definitely have liquid in the liquid hose. Reseat the liquid
line core. Slowly open the high side manifold valve and
transfer the liquid refrigerant from the liquid line hose and
charging cylinder hose into the suction service valve port.
CAREFUL: Watch so that liquid refrigerant does not
enter the compressor.
Due to their design, Scroll compressors are inherently more
tolerant of liquid refrigerant.
NOTE: Even though the compressor section of a Scroll
compressor is more tolerant of liquid refrigerant, continued
floodback or flooded start conditions may wash oil from the
bearing surfaces causing premature bearing failure.
S-104 CHECKING COMPRESSOR EFFICIENCY
The reason for compressor inefficiency is broken or damaged
scroll flanks on Scroll compressors, reducing the ability of
the compressor to pump refrigerant vapor.
The condition of the scroll flanks is checked in the following
manner.
1. Attach gauges to the high and low side of the system.
2. Start the system and run a “Cooling Performance Test.
If the test shows:
a. Below normal high side pressure.
b. Above normal low side pressure.
c. Low temperature difference across coil.
d. Low amp draw at compressor.
And the charge is correct. The compressor is faulty - replace
the compressor.
S-105B THERMOSTATIC EXPANSION VALVE
The expansion valve is designed to control the rate of liquid
refrigerant flow into an evaporator coil in exact proportion to
the rate of evaporation of the refrigerant in the coil. The
amount of refrigerant entering the coil is regulated since the
valve responds to temperature of the refrigerant gas leaving
the coil (feeler bulb contact) and the pressure of the refriger-
ant in the coil.
This regulation of the flow prevents the return of liquid
refrigerant to the compressor.
The three forces which govern the operation of the valve are:
(1) the pressure created in the power assembly by the feeler
bulb, (2) evaporator pressure, and (3) the equivalent pressure
of the superheat spring in the valve.
0% bleed type expansion valves are used on the indoor coils.
The 0% valve will not allow the system pressures (High and
Low side) to equalize during the shut down period. The valve
will shut off completely at approximately 100 PSIG Pressure.
Good thermal contact between the feeler bulb and the
suction line is essential to satisfactory valve control and
performance.
The bulb must be securely fastened to a clean straight
section of the suction line. Application of the bulb to a
horizontal run of line is preferred. If a vertical installation
cannot be avoided the bulb should be mounted so that the
capillary tubing comes out at the top.
THE VALVES PROVIDED ARE DESIGNED TO MEET THE
SPECIFICATION REQUIREMENTS FOR OPTIMUM PROD-
UCT OPERATION.
DO NOT USE SUBSTITUTES.