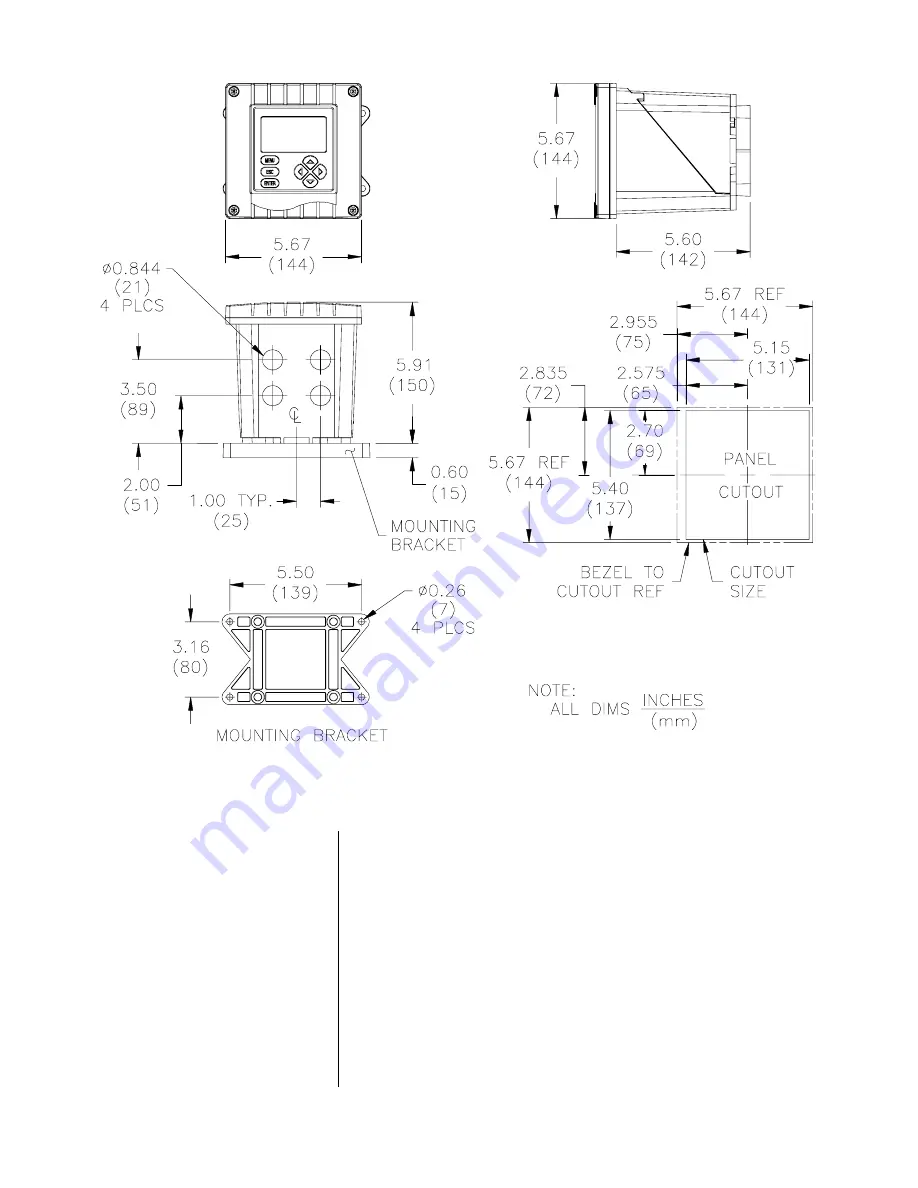
PART TWO - INSTALLATION
SECTION 2 - MECHANICAL REQUIREMENTS
Accu4™ Low-range Turbidimeter System
Rev. 2-300
24
FIGURE 2-7 Analyzer Installation Dimensions Details
2.6 Sensor and Analyzer
Conduit Hole
Requirements
☞
Recommendation:
Run all wiring to the sensor and ana-
lyzer in 1/2-inch, grounded metal conduits. If using only
shielded cables, appropriate strain reliefs or cable grips are
required. (GLI sells accessory cable grips, part number
3H1091, and watertight locknuts, part number 3H1230, for
cable entries.) Seal unused cable entry holes with appropri-
ate plugs.
NOTE:
Use NEMA 4 (
≅
CSA type 4;
≅
IP65) rated fittings
and plugs to maintain the watertight integrity of the
NEMA 4X sensor and analyzer enclosures, and to
comply with Div. 2 hazardous area requirements.