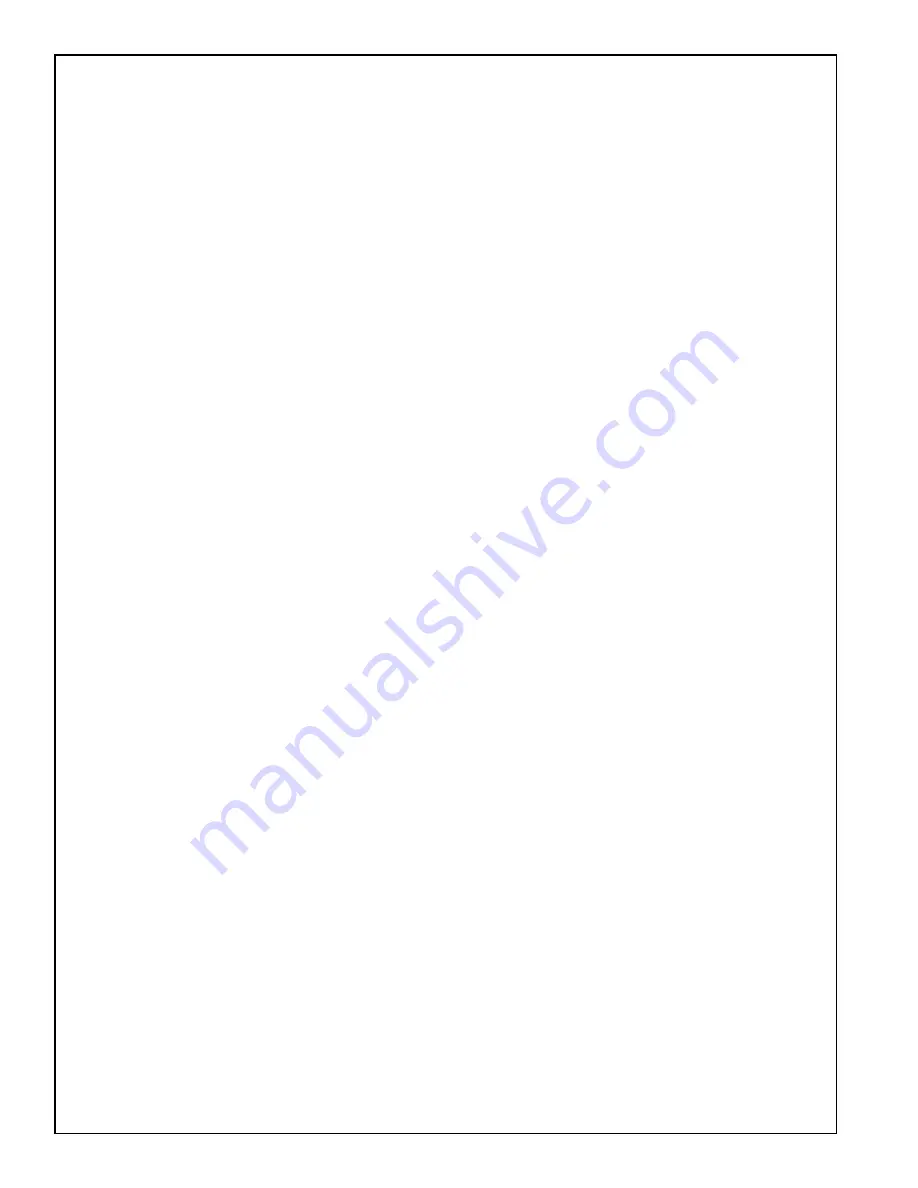
Glentek Inc. 208 Standard Street, El Segundo, California 90245, U.S.A. (310) 322-3026
64
Omega Series Digital PWM Amplifier Manual
Hall Commutation Initialization
Hall commutation initialization is a method that relies on sensors to give an approximation of the initial
commutation angle of a motor. Hall initialization uses Hall sensors or commutation tracks (simulated
Hall sensors built into the shaft encoder) to determine the rotor angle. In a brushless motor three Hall
sensors are used to detect rotor position. The three Hall sensors employed are commonly named U, V
and W; S1, S2 and S3; or A, B and C. The l sensors are digital (on/off) devices and therefore the com-
bination of the three can result in eight different states. The sensors are aligned with the motor in a
way that causes the output of the sensors to transition through six of the eight possible states as the
motor is rotated through 360 electrical degrees. Each Hall state corresponds to 60 electrical degrees.
Only one sensor changes states at any given transition.
At power up, the servo drive reads the state of the Hall sensors and from this state can determine
within ±30 electrical degrees where the motor shaft is located. This is close enough to start commutat-
ing the motor, so the servo drive uses this approximation as the actual rotor position. Once motion is
commanded (position, velocity or torque), the servo drive starts commutating with this value and
watches for a transition of the Halls state. Upon this transition, the servo drive knows the exact loca-
tion of the rotor shaft and updates the commutation angle based on this known location.
This method, unlike Twang or Dither, does not move the rotor shaft at power up. Instead, it uses a
non-optimal commutation angle at start-up and corrects to the optimal commutation angle upon the first
Hall state transition once motion is commanded.
Phase Lead
Phase lead is a gain applied to the commutation angle based on the velocity of the motor. Units are
usually in degrees of commutation angle per 1000 rpm (degrees/krpm). Usually the phase angle is ad-
vanced for a positive velocity. An ideal phase lead at a given rpm in a specific application will minimize
current in the motor. Phase lead is useful in applications where a velocity is held constant for a long
period of time, particularly if the velocity is held at or near the rated speed of the motor. Spindle motors
are a good application where phase lead is used. Appropriately used phase lead will reduce power
consumption. This being said, most applications do not make use of phase lead.
Sinusoidal Commutation
In sinusoidal commutation a sinusoidal current is applied to each phase of the motor to cause the mo-
tor to rotate. In a three phase motor, the relationship of the currents applied in the three phases for a
positive rotation of the rotor is:
IR(
θ
e) = I * sin(
θ
e),
IS(
θ
e) = I * sin(
θ
e - 120°),
IT(
θ
e) = I * sin(
θ
e - 240°);
where:
IR, IS, and IT are the currents applied to phase R, S, and T respectively,
I is the amplitude of the commanded current,
θ
e is the “electrical angle” of the applied currents.
The relationship between the electrical angle,
θ
c, and the mechanical angle (the angle of the rotor),
θ
m, is:
θ
m =
θ
c x 2/N,
where
N is the number poles in the motor.
For example, a 4-pole motor (two North poles and two South poles) will rotate 180 me-
chanical degrees as the currents applied are varied through 360 electrical degrees.
Содержание Omega SMC9930
Страница 73: ...Glentek Inc 208 Standard Street El Segundo California 90245 U S A 310 322 3026 73 Appendix K...
Страница 75: ...Glentek Inc 208 Standard Street El Segundo California 90245 U S A 310 322 3026 75 Appendix K...
Страница 77: ...Glentek Inc 208 Standard Street El Segundo California 90245 U S A 310 322 3026 77...